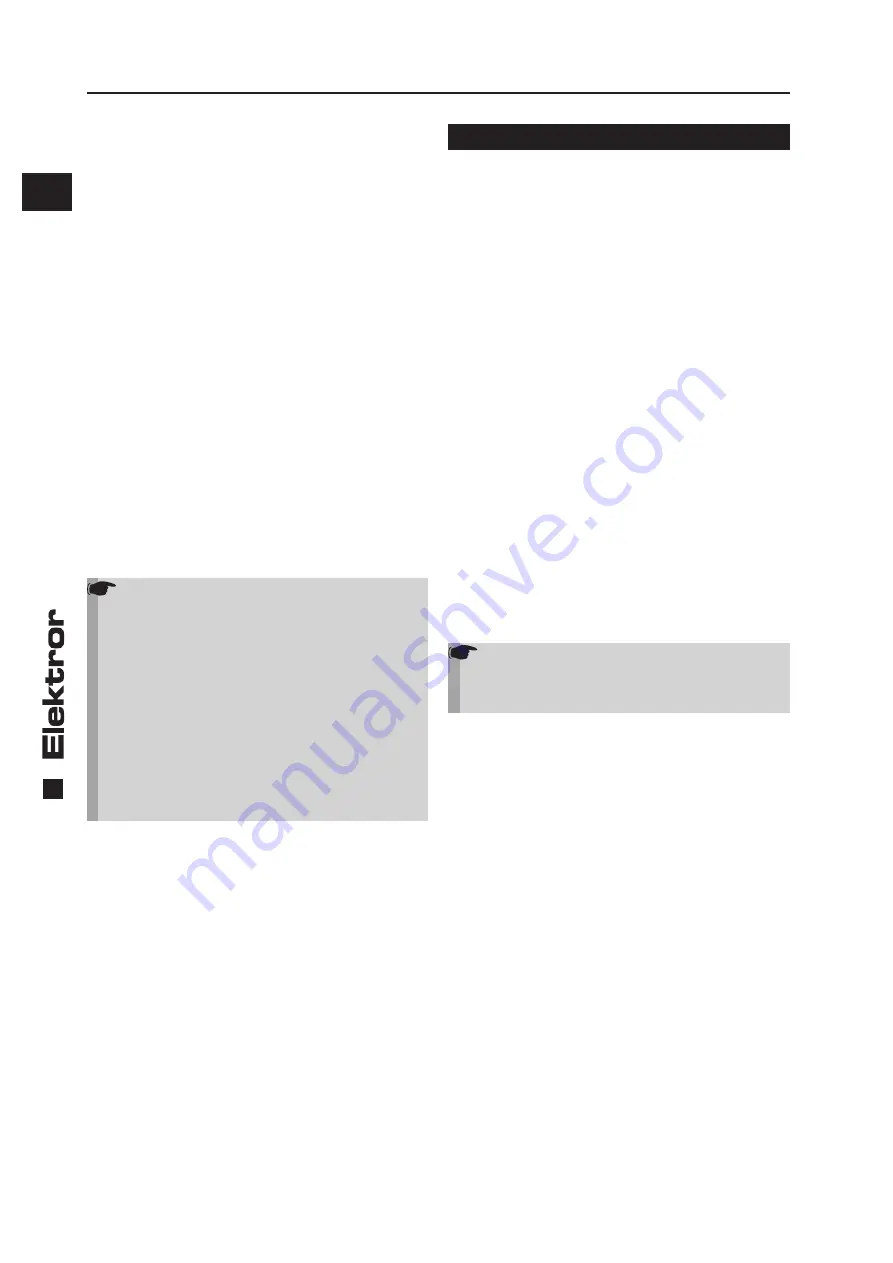
20
EN
Operating and assembly instructions HRD FU-ATEX
www.elektror.com
9016330 01.20/08
After protective shutdowns, e.g. tripping of the motor circuit-
breaker, activation of the PTC evaluation unit by motors with a
PTC resistor sensor, or after a protective shutdown of the fre-
quency converter during FC applications, the appliance must
not be restarted until the problem has been troubleshooted.
If the blower cannot be operated over the whole range of the
characteristic curve, the motor may overload if the system
resistance is too low (excessive current consumption). The
volumetric air
fl
ow should be reduced in this case by means
of a throttle valve
fi
tted on the intake or discharge side.
The blower must not be subjected to vibration or impact
loads.
4.2 Frequency converter operation
A frequency converter is used, allowing a wide range of speed
adjustments. There is only a small, load-related di
ff
erence in
rpm between idle state and the max. load of the blowers and
the lateral channel blower. Setting work that requires inter-
vention in the converter parameters (e.g. speed adjustment)
must be carried out (and documented) by quali
fi
ed techni-
cians because incorrect values in a few critical converter pa-
rameters (e.g. the cut-o
ff
frequency of the converter output
characteristic curve) can result in increased power consump-
tion, overheating, winding damage and/or malfunction of the
ATEX application.
Please also note the instructions under 3.3 (
ff
).
If they are not observed, the motor current will increase
disproportionately and the drive motor will fail to achieve its
rated speed.
Note!
Do not set the converter to a higher frequency
(rpm) than the frequency (f
B
) speci
fi
ed on the
nameplate, because this can overload the motor
or irreparably damage the blower due to over-
speeding. Similarly, a so-called boost must never
be set at the converter because this would result
in excessive heating of the drive motor. The
temperature sensors must be connected to the
relevant converter inputs in order to protect the
drive motor.
To ensure safe and trouble-free operation of the
frequency converter, the installation and safety
instructions provided by the frequency converter
supplier in the operating or application manuals
must be strictly adhered to.
Protection by residual-current-operated circuit breaker
(FI circuit-breaker):
The present IGBT frequency converters produce discharge
currents of >=3.5 mA due to their design principle. These dis-
charge currents can lead to unwanted tripping in systems
protected by a 30 mA-FI circuit-breaker.
If a fault occurs, fault currents can also discharge through the
PE conductor as direct current. If protection is needed on the
supply side by means of an FI circuit-breaker, then an ACDC
sensitive (type B) FI circuit-breaker must be used. Use of an
FI circuit-breaker other than type B can cause death or seri-
ous injury if a fault occurs.
To meet the EN 61800-5-1 standard, the PE conductor must
be duplexed and routed through separate terminals or have
a cross-section of at least 10 mm² Cu.
Operation and connection to public grids:
Most frequency converters are designed to operate on indus-
trial grids. If the converter is connected directly to and oper-
ated on a public grid, then additional interference suppres-
sion measures, such as a mains choke, must be built into the
mains feeder. For further information, refer to the converter
manufacturer’s speci
fi
cations.
5 INSTRUCTIONS FOR MAINTENANCE
5.1 Basic information
Before and after maintenance/service measures, repairs or
replacement of parts, an Elektror ATEX blower may only be
employed as intended (see 1.1).
Before commencing with the maintenance/service measure,
repair or replacement of parts ensure that the blower impel-
ler has stopped and the blower has been secured reliably to
prevent start-up. For instance, electric power supply to the
blower must be interrupted, ideally by separation at the ter-
minals.
At no point during maintenance, cleaning, service or repair
may an explosion hazard exist or arise.
Wear parts are subject to the recommend maintenance in-
tervals (see 5.2 to 5.7 ). The service life of wearing parts
(ball bearings and
fi
lters) depends on the operating hours,
the load and other in
fl
uences, such as temperature, etc.
Accessibility for regular maintenance must be ensured.
Maintenance and servicing may only be performed by per-
sons with the necessary expertise and regular training. In ad-
dition to the appliance’s operating instructions and the regu-
lations and recommendations for the system as a whole, the
following points should be observed:
5.2 Inspection and maintenance intervals:
The operator must set the cleaning, inspection and mainte-
nance intervals himself according to operating hours, load
and operating conditions.
Immediate inspection and maintenance
The blower must be inspected immediately if vibrations or
reduced air
fl
ow are observed.
Note!
We recommend to have repairs carried out by the
manufacturer. We cannot accept any liability for
repairs carried out by third parties.
Perform the following tasks in course of every inspec-
tion/maintenance job as well as upon repair and replace-
ment of parts:
• Visually inspect all movable parts of the blower, such as
impeller, blower housing cover / intake nozzle for possible
damage, scoring, wear,
fi
ssures, cracks, deformation;
proper condition of all earthing connections, radial shaft
seals etc.
• Inspect the gap between the impeller nozzle and the intake
nozzle at the blower cover.
ATEX machine type HRD 7 FU:
Minimum gap 3.0 mm
All other HRD ATEX machine types:
Minimum gap 2.0 mm
• If ATEX blowers are stored for replacement, note that some
components installed have a limited storage life. This espe-
cially applies to the ball bearings, e.g. concerning the life of
the grease lubrication. The storage life depends on the type
of storage and the unit type as well as on the conditions and
duration of storage of the Elektror product. Type-related in-
formation can be acquired from Elektror Product manage-
ment.
• Inspection and service work must be documented chrono-
logically and fully stating the name of the person responsi-
ble. In particular, operating errors, measures implemented
as well as compliance with all applicable regulations and the
manufacturer’s speci
fi
cations must be documented. It is rec-
ommended that this documentation be kept in a report book
and safely stored.