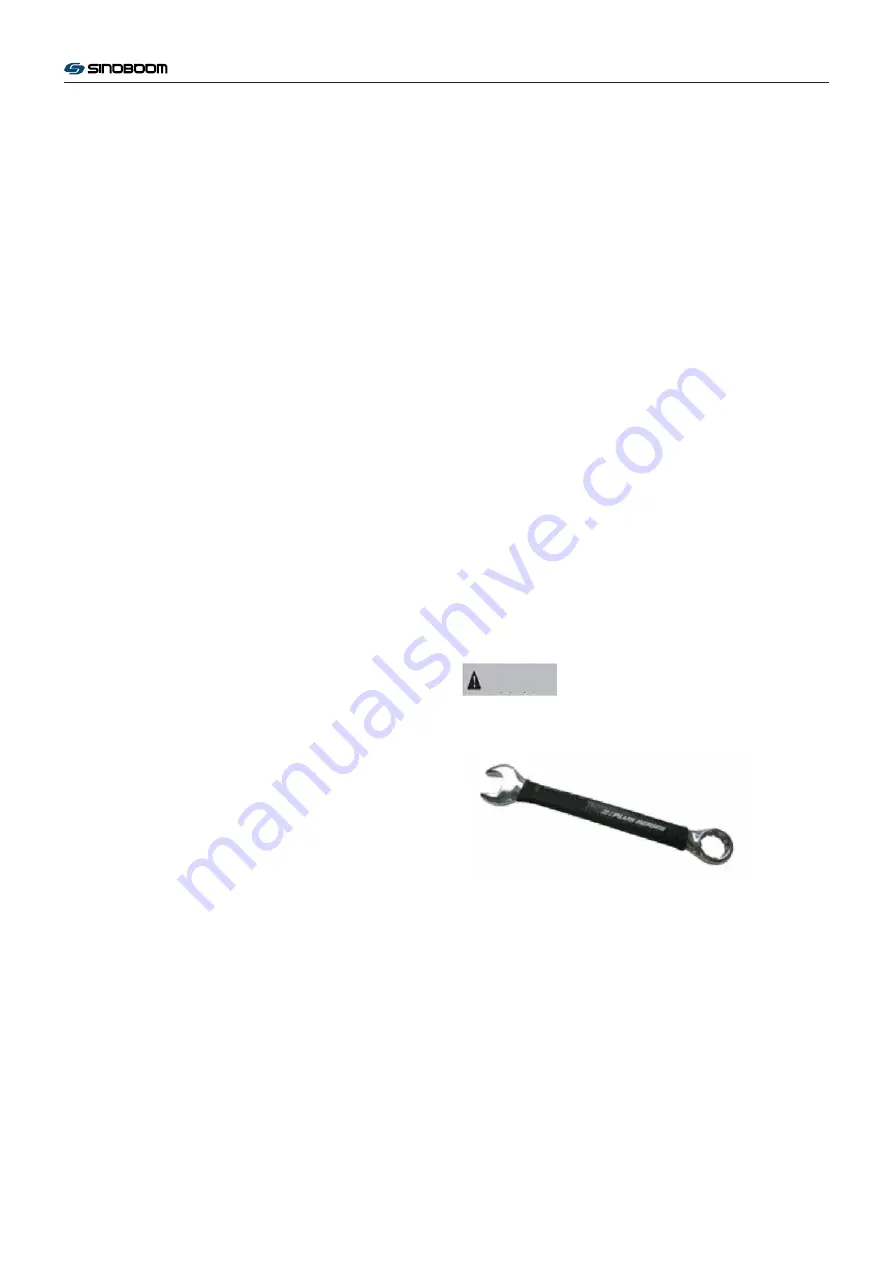
Electrical System
5-1 Use and Maintenance of Lead-Acid Storage
Battery
a.
Required Equipment
Protective goggles and gloves
Wrench with rubber handle
Sodium bicarbonate
Terminal post protector (i.e. petroleum
jelly and corrosion prevention spray etc.)
Voltmeter (in allusion to flooded/wet
battery, colloid and AGM battery)
Distilled water and purified water
(deionized water and reverse osmosis
water etc.)
Discharge tester (if any)
Specific gravity hydrometer (in allusion to
flooded/wet battery)
b.
Safety Instructions for Battery Installation
It is necessary to always wear protective
clothing, gloves and goggles when handling the
battery.
Do not smoke near the battery, and keep the
battery away from spark, flame and metal
objects.
It is necessary to use wrench with rubber handle
when connecting the battery.
The electrolyte is the mixed solution of acid and
water. thus, prevent it contacting with the skin.
It is necessary to wash immediately with water
when the acid is in contact with the skin or the
eyes.
Inspect whether the cable of the terminal is
connected reliably; the terminal posts may get
damaged, molten or catch fire if the connection
is too tight or too low.
Do not put any object on the battery for
avoiding short circuit.
The wet lead-acid battery will release little gas
in the process of use, particularly in the charging
process; thus, it is necessary to charge the
battery in a well-ventilated place.
Do not add acid into the battery.
Always keep the battery vertical. The electrolyte
in the battery may flow over if the batter is
placed sidelong or tilting.
c.
Instructions for Battery Connection
1.
Battery Cable and Torque Value
The battery cable could provide connection
among and between battery, equipment and
charging system. It is necessary to connect the
battery, the charging system and the equipment
with flexible cable. improper connection might
lead to poor performance or damaged, molten or
burning terminals.
Tightening torque of cable fixing nut:
M8 Tightening torque 9
~
11/Nm
,
M10 Tightening torque 18
~
23/ Nm
。
The terminal may be damaged if the terminal is
connected too tightly; the terminal may be
molten or catch fire if the terminal is connected
too loosely.
It is necessary to use the wrench with rubber
handle with connecting the battery.
2.
Terminal Protection
The terminal may get corroded continuously if it is
not kept clean and dry. For preventing corrosion, it is
necessary to apply a thin layer of petroleum jelly or
use terminal protector.
Warning
35
GTJZ1412 & GTJZ1414
Maintenance Manual