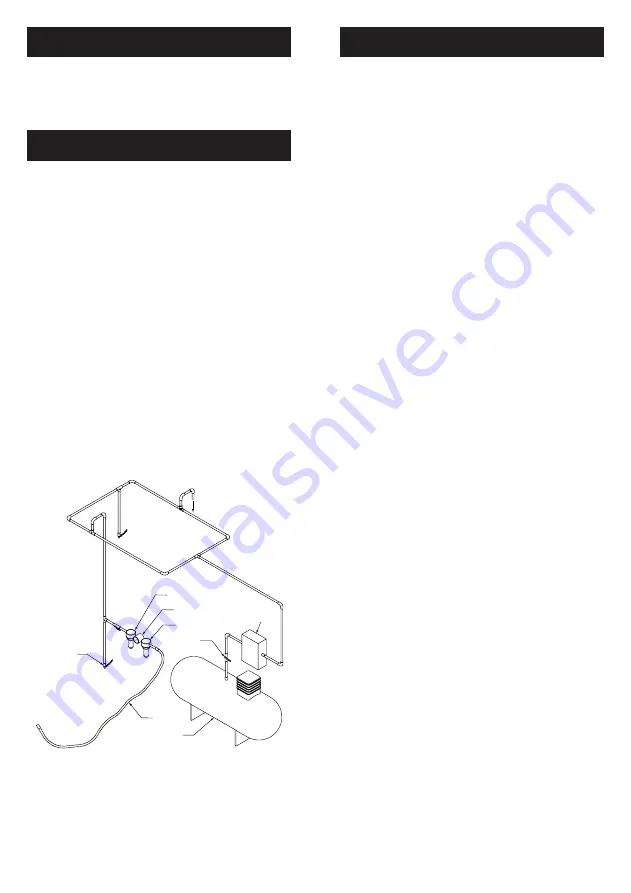
DOC EATDS60S1P
6
Revision 08/19/20
Work Stations
Putting the Tool into Service
Safety Information
The tool is intended to be operated as a hand held tool. It is
always recommended that the tool be used when standing
on a solid floor. It can be in any position but before any such
use, the operator must be in a secure position having a firm
grip and footing and be aware that the tool can develop a
torque reaction. See the section “Safety Information”.
Use a clean lubricated air supply that will give a measured
air pressure at the tool of 90 psig (6.2 bar) when the tool is
running with the lever fully depressed. It is recommended
to use an approved 3/8 in. (10 mm) x 25 ft (8 m) maximum
length airline. It is recommended that the tool be connected
to the air supply as shown in Figure 1.
Do not connect the tool to the airline system without incorpo-
rating an easy to reach and operate air shut off valve. The air
supply should be lubricated. It is strongly recommended that
an air filter, regulator and lubricator (FRL) be used as shown
in Figure 1 as this will supply clean, lubricated air at the
correct pressure to the tool. Details of such equipment can
be obtained from your supplier. If such equipment is not used
then the tool should be manually lubricated
To manually lubricate the tool, disconnect the airline and put
2 to 3 drops of suitable pneumatic motor lubricating oil such
as Fuji Kosan FK-20, Mobil ALMO 525 or Shell TORCULA®
32 into the hose end (inlet) of the machine. Reconnect tool to
the air supply and run tool slowly for a few seconds to allow
air to circulate the oil. If the tool is used frequently, lubricate
it on a daily basis or lubricate it if the tool starts to slow or
lose power.
It is recommended that the air pressure at the tool be 90 PSI
(6.2 Bar) while the tool is running so the maximum RPM is not
exceeded. The tool can be run at lower pressures but should
never be run higher than 90 PSI (6.2 Bar). If run at lower pres-
sure the performance of the tool is reduced.
Closed Loop Pipe System
Sloped in the direction
of air flow
Drain Leg
Ball Valve
To Tool Station
Filter
Drain Valve
Regulator
Lubricator
Ball
Valve
Ball Valve
Air Flow
Air Dryer
Air Compressor
and Tank
Air Hose
To Coupler
at or near Tool
Figure 1
1) Read all instructions before using this tool. All operators
must be fully trained in its use and aware of these safety
rules. All service and repair must be carried out by
trained personnel.
2) Never direct air at yourself or anyone else.
3) Install air fitting into inlet bushing of tool.
4) Always remove the air supply to the tool before fitting,
adjusting or removing the abrasive/accessory.
5) Always wear required safety equipment when using this
tool.
6) When operating always place the tool on the work then
start the tool. Always remove the tool from the work
before stopping. This will prevent gouging of the work
due to excess speed of the abrasive/accessory.
7) Always adopt a firm footing and/or position and be aware
of torque reaction developed by the tool.
8) Use only correct spare parts.
9) Always ensure that the workpiece is firmly fixed to pre
-
vent its movement.
10) Check hose and fittings regularly for wear. Do not carry
the tool by its hose; always be careful to prevent the tool
from being started when carrying the tool with the air
supply connected.
11) Dust can be highly combustible. Keep working area
clean.
12) Dust from some work processes can cause cancer, birth
defects or other respiratory diseases. Risk assessment
of these hazards and implementation of appropriate
controls is essential.
13) Direct the exhaust so as to minimized disturbance of dust
in a dust filledenvironment
14) Do not operate the tool in explosive atmospheres, such
as in the presence of flammableliquids, gases, or dust.
The abrasives are able to create sparks when working
material, resulting in the ignition of the flammabledust
or fumes.
15) Do not exceed maximum recommended air pressure.
Use safety equipment as recommended.
16) The tool is not electrically insulated. Do not use where
there is a possibility of coming into contact with live
electricity, gas pipes, water pipes, etc. Check the area of
operation before operation.
17) Take care to avoid entanglement with the moving parts
of the tool with clothing, ties, hair, cleaning rags, etc. If
entangled, it will cause the body to be pulled towards the
work and moving parts of the machine and can be very
dangerous.
18) Keep hands away from rotating or reciprocation acces-
sories, spindles or other moving parts during use.
19) If the tool appears to malfunction, remove from use im-
mediately and arrange for service and repair.
20) Do not allow the tool to free speed without taking precau-
tions to protect any persons or objects from the loss of
the abrasive/accessory.
21) Do not allow tool to free run for an extended period of
time as this will shorten its life.