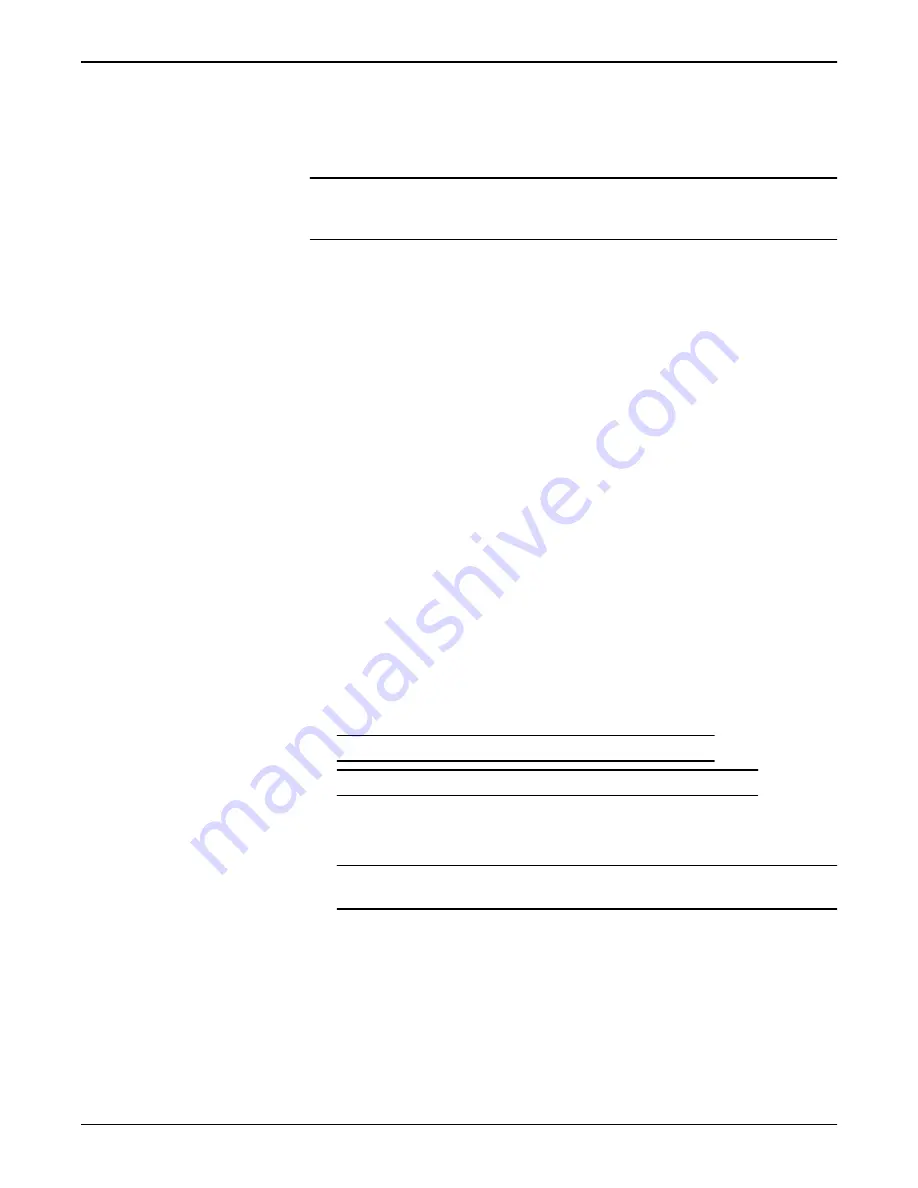
Installation
Install the valve and Advantage actuator
Note: The actuator size and configuration can limit the actual operating pressure.
Consult the engineering catalog for actuator sizing. Consult the factory or engineering
catalog for vacuum operation.
Consider the following information before installing the actuator:
• The series 3, 5, 8, or 16 stainless steel bonnet Advantage Actuator can have the air inlets positioned in
any quadrant.
• Maximum valve operating pressure is 150 PSIG (10.34 bar). This pressure is applicable up to 100º F
(38º C). Valves at maximum pressure cannot be used at maximum temperatures.
To install the valve and Advantage Actuator, complete the following procedure:
1. If welding manually, remove the actuator.
2. If welding end valves for schedule 10 or heavier pipe, remove the actuator prior to welding in line.
3. If welding end valves for schedule 5 or lighter pipe and tubing, welding with automatic equipment is
acceptable. In this situation, complete the following steps prior to performing the weld.
a) Do not remove the actuator.
b) Set the valve to the open position.
c) Properly purge the valve with an inert gas.
4. Install the valve stem between 0 and 30 degrees above horizontal for horizontal piping systems to be
drained through the valve.
The proper valve orientation differs depending upon the valve type.
• Dia-Flo diaphragm valves can be installed in any orientation.
• Pure-Flo valves have either raised hash marks (castings) or small machined dots (forgings) on the
valve body to indicate the correct drain angle. Position these marks at the 12 o’clock position to
achieve the optimum drain angle.
5. Prior to pressurization (with the valve slightly open), follow the steps in the Tighten the bonnet
fasteners.
6. For series 33 and 47 actuators, prepare an eye bolt with a 0.625" -18 female thread to attach to the
adjusting bushing.
Note: Do not lift series 33 and 47 actuators by their air fittings.
Note: If the actuator is a series 47 actuator, use a hoist to lift the valve.
7. Connect the air line.
Connection size is 1/8" NPT for series 3, 5, 8 and 16 actuators and 1/4" NPT for series 33 and 47
actuators.
Note: Air line connections should be made with care so as not to damage the
plastic actuator covers.
8. Cycle the valve two to three times to verify smooth operation.
Install diaphragm
1. Unscrew the diaphragm from the compressor by turning counterclockwise.
a) Periodically inspect the valve compressor pin for excessive wear. Replace the pin or compressor if
excessive wear or axial pin movement is found.
The replacement diaphragm should be identical in size and grade to the original diaphragm.
2. For PTFE assemblies only:
Installation
Advantage
®
Actuator Installation and Operation Manual
7
Designed and Manufactured by ITT