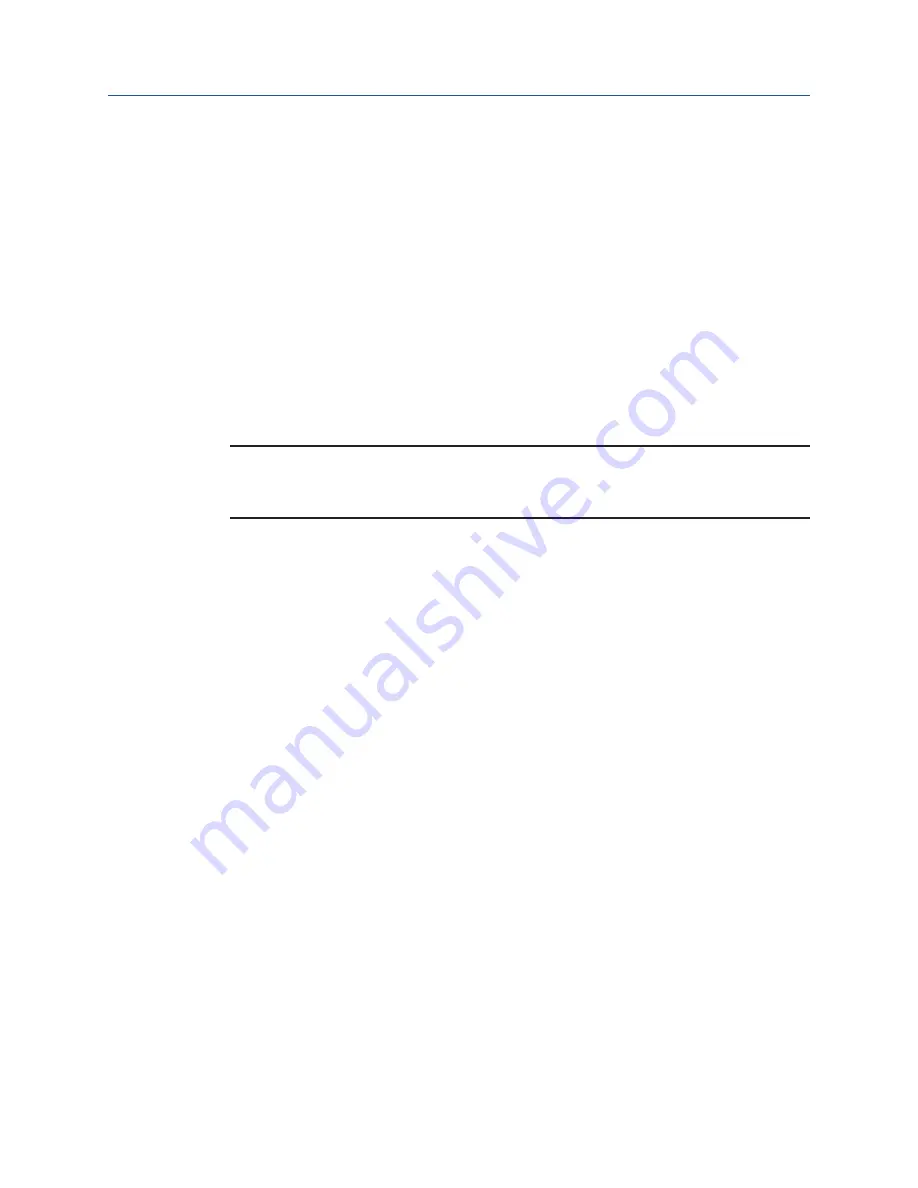
Installation, Operation and Maintenance Manual
DOC.IOM.RG.US Rev. 11
November 2021
13
Section 7: Scheduled Maintenance and Operational Testing
Scheduled Maintenance and Operational Testing
e.
Place both filter/strainer seals item (2) on to the ends of the reassembled outer
and inner filters and insert into the manifold body item (1).
f.
Using a generous amount of grease or hydraulic fluid on the two hex cap o-rings
item (6) screw the hex caps into the body until the hex cap bottoms out. No
specific torque is required for tightening since the hex cap design is a straight
thread/o-ring sealing designed component.
Note:
before re-installing the hex caps (2) and o-rings (6), visually inspect the
o-rings (6) for any nicks or abrasions. Replace o-rings if worn or cuts are observed.
Notes:
-
Recommended replacement period for both filter/strainer elements 5 years.
-
Recommended cleaning for both filter/strainer elements annually, or more often based on
power gas cleanliness.
2.
Drain contaminants from gas/hydraulic tank(s) and refill to proper tank levels.
Refer to Figure 6.
NOTE:
If equipped with additional gas filters, check elements and consider replacing them as it may be
clogged with contaminants.
3.
Refer to Section 2 to ensure that proper method of operation is followed.
4.
Check manual operation with handpump, refer to Section 2.
a.
There should be noticeable suction on the suction stroke, decreasing as the pump
cylinder fills, indicating suction lines are open and full of fluid.
b.
Handle effort on the pressure stroke will depend on line pressure and line
valve position.
c.
Pressure stroke should be smooth and feel solid, not spongy, indicating pressure
lines are open and full of fluid.
d.
At the end of operator stroke (line valve open or closed) the handle should
stop solid on the pressure stroke, indicating no bypass flow in operator or hydraulic
components.
e.
Test by applying 150 lb force for two minutes to the pump handle provided with
the unit.
f.
Press relief knob to move clevis and handle in the down position.