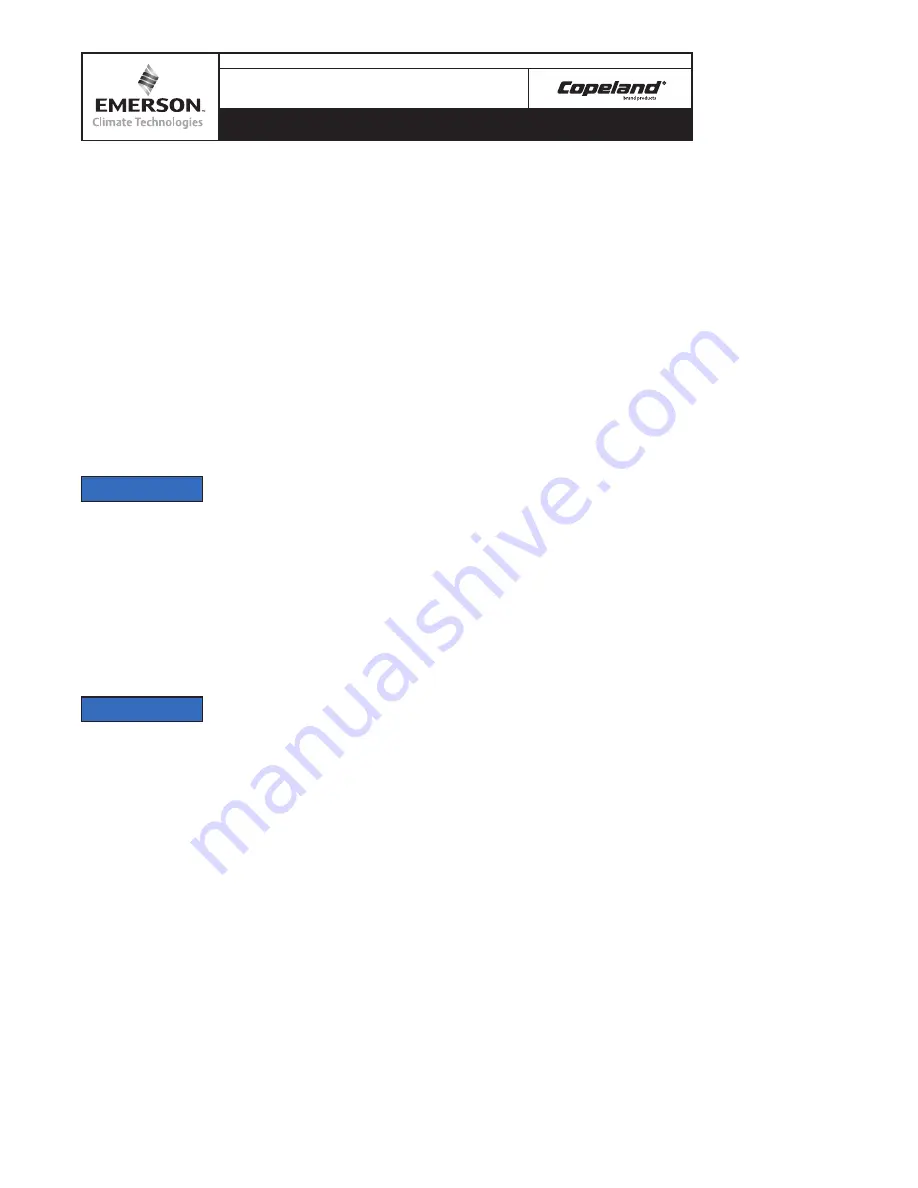
7
© 2011 Emerson Climate Technologies
Printed in the U.S.A.
AE8-1384 R1
Application Engineering
B
U
L
L
E
T
I
N
The history status messages give the order in which the
Warning/Alert
has happened, with the total compressor
run time. Information about the
Warning/Alert
occurrence during the last 7 days and the cumulative
Warning/Alert
counter are also available.
For more information on CoreSense
™
Communications
features and to request Modbus maps please contact
your Application Engineer.
DIP Switch Con
fi
guration
DIP switch selection for the Modbus address, baud rate,
parity, and other operating conditions simplify service
and start-up procedures.
Table 5
lists the purpose of
each switch. See
Figures 5
and
6
for more information
on DIP switch settings. A "darkened" switch setting in
the illustrative
fi
gures indicates the switch setting is
depressed or in the "down" position.
NOTICE
The module must be reset after changing any of
the DIP switch settings for changes to take effect.
CoreSense Communications modules are shipped from
the factory with the DIP switches set to default settings
for standalone operation. Default settings are shown
in
Figure 5
. Switch 1 is turned “on” as part of a quality
control check to verify communications capability of the
module before it leaves the compressor manufacturing
plant. Switch 9 is also turned “on” for TE* motor code. All
other DIP switch default settings are in the “off” position.
NOTICE
If DIP switch settings are inadvertently changed,
the compressor will operate, but could have some
loss of protection. Scroll temperature protection
and short cycle protection could be disabled
.
The following steps cover the DIP switch settings
throughout the commissioning process for a multiple
compressor system with communications.
1. Switches 1 through 5 are used for setting
the device address. DIP switch 1 is the least
signi
fi
cant bit (LSB) and switch 5 is the most
signi
fi
cant bit (MSB). DIP switch addresses
0 through 31 are shown in
Figure 6
. Each
CoreSense Communications module that is daisy
chained and connected to a master controller
must have a unique node address (as determined
by the DIP switch settings).
2. Switch 6 de
fi
nes the communication baud rate for
the CoreSense Communications module. If the
switch is “off”, the baud rate is 19200. If the switch
is “on” the baud rate is 9600. The baud rate of
each CoreSense Communications module should
be set to match the master controller baud rate.
3. Switch 7 de
fi
nes the communications parity.
The default parity setting for the CoreSense
Communications module is no parity. If the switch
is set to “on” the module will communicate using
even parity. The parity setting must match the
parity setting of the master controller.
4. Switch 8 defines the control mode. The
default setting is standalone mode (off). If
communications with a master controller is
desired, switch 8 should be turned “on” to
network.
5. Switch
9
de
fi
nes the thermistor con
fi
guration. If
the compressor has a voltage code of TE*, the
compressor has PTC and NTC thermistors for
motor and scroll temperature protection. If the
compressor voltage code is TW*, the compressor
has only PTC thermistors for motor and scroll
temperature protection. The default setting is “on”
for PTC and NTC thermistor types.
6. Switch 10 enables short cycling protection if
turned “on”. The default setting is “off”.
Jumper Setting
CoreSense Communications modules are shipped
with the jumper installed. For standalone operation
the jumper should remain installed. For daisy chained
applications the jumper should remain installed for
the modules on the ends of the daisy chain. All other
jumpers in the sequence of daisy chained modules
should be removed. The jumper can be removed using
miniature electronics needle nose pliers
PC Interface Software
PC interface software is available from Emerson Climate
Technologies, Inc. The PC interface software allows
the design engineer access to status, con
fi
guration,
history, and data logging via a computer. This method of
connecting and communicating with CoreSense is very
helpful during the unit development stage if CoreSense
is in stand-alone mode and not communicating with a
master controller.
The RS-485/USB adapter used to connect the laptop
to the CoreSense is B & B Electronics model number
USOPTL4.
Figure 7
illustrates the wiring and DIP switch
settings necessary to enable communications.
For more information on the PC interface software, how
to obtain it, and a tutorial on its use, please contact your
Application Engineer.