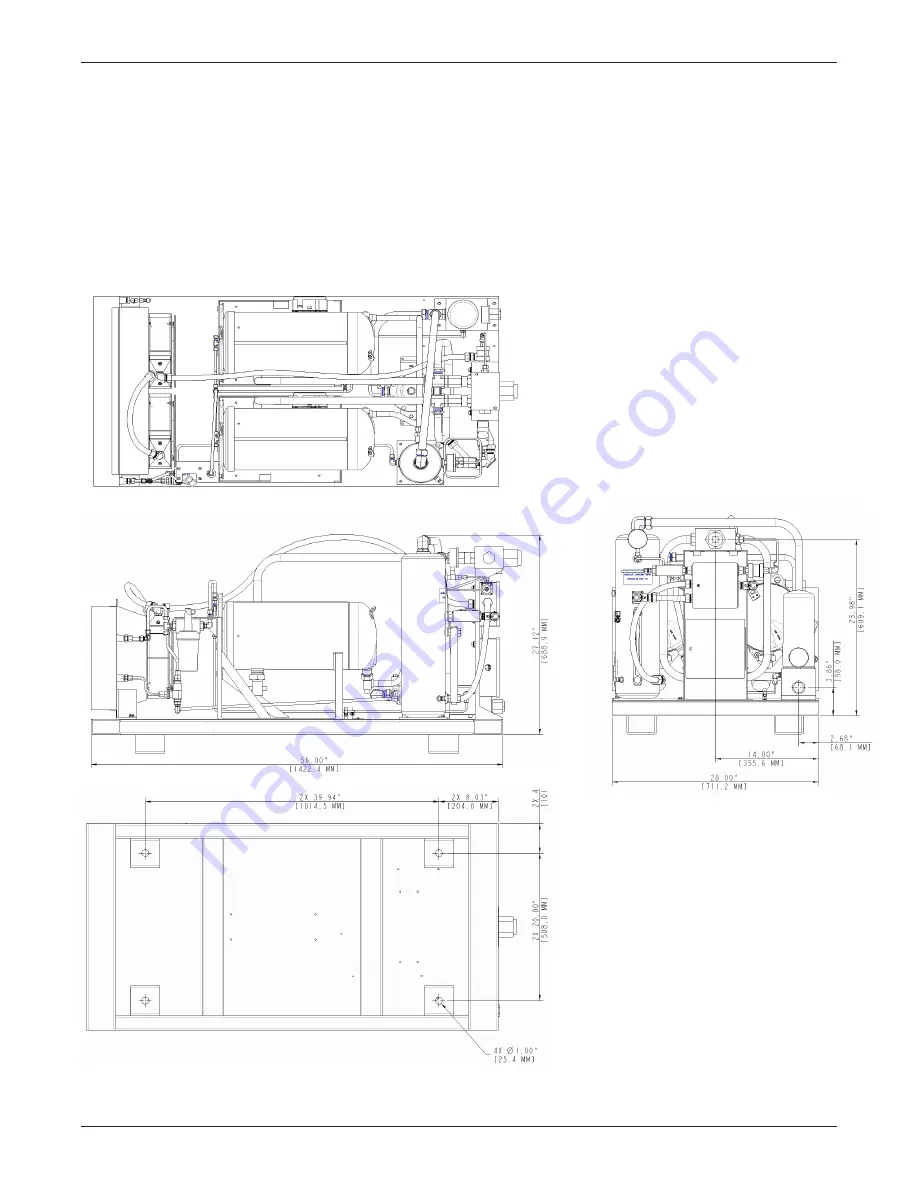
7
2006SSD-75 R4 (10/10)
6
2006SSD-75 R4 (10/10)
Dual-Compressor Module
Installation
TOP
VIEW
FRONT
VIEW
SIDE
VIEW
BOTTOM
VIEW
2.4 Installation Clearance and Dimensions
Allow sufficient clearance on all sides for service access, especially for gas and electrical connections at
the rear of the Compressor Module. Check applicable national and local electrical codes.
Cooling air flow is back to front—from the gas connection end to the oil cooler end. Do not block or restrict
the cooler fans or oil cooler.
Refer to
Figure 4
for the dimensions of the Compressor Module.
Figure 4 Compressor Module Dimensions, in. (mm)
Summary of Contents for Copeland Scroll SZO44
Page 2: ......
Page 34: ...Dual Compressor Module Technical Support and Service 28 2006SSD 75 R4 10 10 ...
Page 40: ......
Page 41: ......