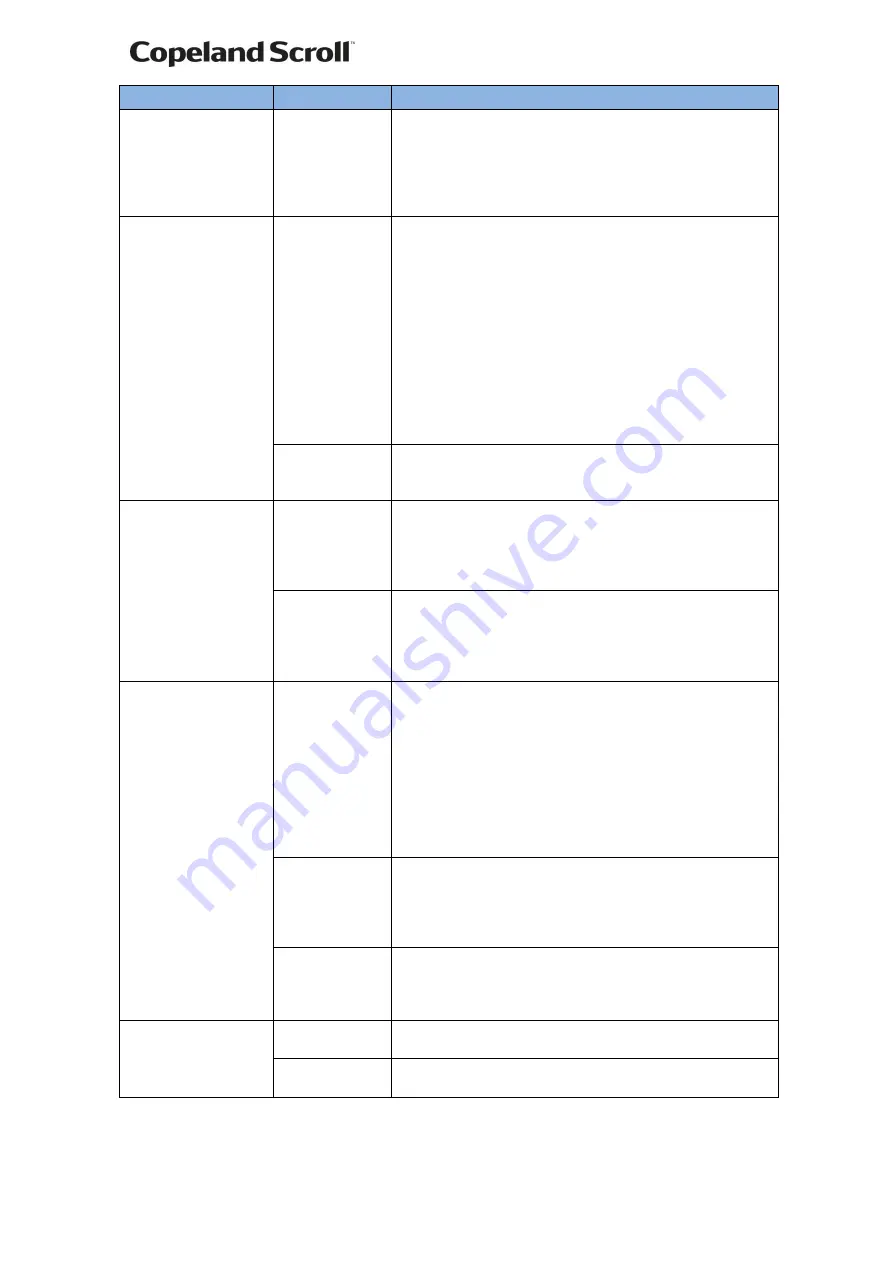
30
C6.2.26/1013-1116/E
Condition
Cause
Corrective action
Defective
motor
protector
If all operating conditions are normal, the voltage
supply at the compressor terminals is balanced and
within limits, the compressor crankcase temperature is
within normal limits, and the amperage drawn is within
the specified range, the motor protector may be
defective.
Excessive discharge
temperature
Insufficient
cooling
medium
injected
For compressors using vapour injection, make sure the
expansion valve is connected at a distance between
150 mm and 200 mm from the economizer inlet and at
a position not lower than inlet connection. The injection
line economizer to compressor should be properly
sized to avoid pressure drop. For good refrigerant
distribution in the economizer respect the
recommendations especially those regarding the inlet
pipes for the vapour injection according to BHE-
manufacturer. The liquid line from the BHE to the
expansion valve(s) need to be well insulated as well. A
solenoid valve should be installed on the liquid line to
prevent refrigerant migration.
Too high
compressor
superheat
Make sure the compressor operates within the
acceptable superheat range published by Emerson.
The Scroll
compressor runs
continuously
Excessive
cooling/heating
load or
inadequate
insulation
Check the load design; make sure that proper
insulation is applied. Correct it as necessary.
Control circuit
inoperative
Check the thermostat, measure the temperature of the
room and compare with the thermostat; replace or re-
calibrate the thermostat.
Check the LP control switch and replace it if it is found
defective.
Compressor
lubrication problem
Oil trap due to
incorrect
piping layout /
sizing
Check the piping layout design. Installations of pipe
being routed over or around obstacles can inadvertently
create unwanted traps for the oil return. As much as
possible the refrigerant line should travel a direct and
straight course between the evaporator and
compressor. It should also be remembered that the
entire system will be coated in oil to some extent. Oil
viscosity changes with temperature. More oil stays in
the system than was originally expected. Make sure the
line is correctly sized.
Oil pump out
due to high
cycling rate
A high cycling rate will pump oil into the system and
lead to lubrication failure. Oil leaves the compressor at
start-up and the short running time is insufficient to
return the oil to the compressor via the suction side. Try
to limit the number of cycles to maximum 10 per hour.
Low gas
velocity
System gas velocity changes depending on
temperature and load (capacity control). In low load
conditions gas velocity may not be high enough to
return oil to the compressor.
Low discharge
pressure
Low ambient
temperature
Fit a fan cycling control system.
Refrigerant
undercharge
Check the system for leaks. Observe sight glass for
bubbles. Add refrigerant until the sight glass is clear.