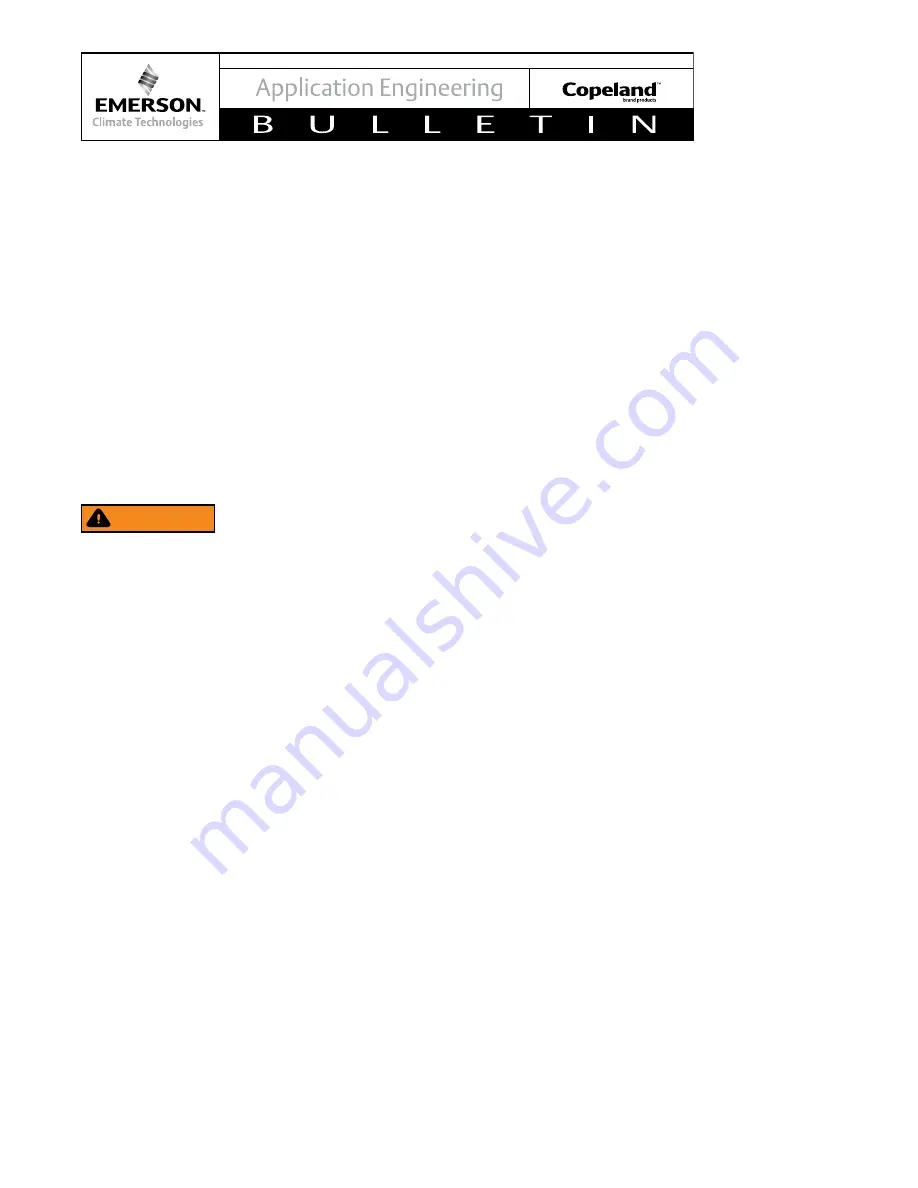
16
© 2016 Emerson Climate Technologies, Inc.
AE4-1303 R15
Compressor Replacement after Motor Burn
In the case of a motor burn, the majority of
contaminated oil will be removed with the compressor.
The rest of the oil is cleaned through use of suction
and liquid line filter dryers. A 100% activated alumina
suction filter drier is recommended but must be
removed after 72 hours. See
AE24-1105
for clean up
procedures and
AE11-1297
for liquid line filter-drier
recommendations.
NOTICE It is highly recommended that the suction
accumulator be replaced if the system contains
one.
This is because the accumulator oil return orifice
or screen may be plugged with debris or may become
plugged shortly after a compressor failure. This will
result in starvation of oil to the replacement compressor
and a second failure.
Manifolded Compressor Replacement
WARNING
When lifing manifolded compressor assemblies,
all compressors must be lifted by their respective
lifting rings. Use care and exercise extreme caution
when lifting and moving compressors. Personal
safety equipment must be used.
Should a compressor fail in a manifolded set, only the
failed compressor should be replaced and not both
compressors. The oil from the failed compressor will
stay mostly in the failed compressor. Any contaminated
oil that does enter the tandem circuit will be cleaned by
the liquid line filter drier, and when used, the suction
line filter drier.
The suction and discharge manifolds can be reused
if the failed compressor is carefully removed and the
manifolds are cut in such a way that a coupling and short
piece of copper can reconnect the new compressor. A
new oil equalization line can be field fabricated using
3/8" (10mm) OD AC&R tubing, if one is needed. The
replacement oil equalization line should be formed to
exactly the same outline and dimensions as the line that
is being replaced. To reconnect the oil equalization line
to the compressor, the oil in one or both compressors
will have to be lowered below the oil fitting on the
compressor. To do this, oil should either be removed
from the compressors or the compressors should be
tilted back a minimum of 12 degrees from horizontal
to move the oil away from the fitting (see
Figure 10
).
Start-up of a New or Replacement Compressor
It is good service practice, when charging a system
with a scroll compressor, to charge liquid refrigerant
into the high side only. It is not good practice to dump
liquid refrigerant from a refrigerant cylinder into the
crankcase of a stationary compressor. If additional
charge is required, charge liquid into the low side of
the system with the compressor operating.
WARNING!
Do not start the compressor while the system is in
a deep vacuum.
Internal arcing may occur when any
type of compressor is started in a vacuum.
NOTICE
Do
not operate the compressor without enough system
charge to maintain at least 55 psig (3.8 bar) suction
pressure for R-410A and 20 psig (1.4 bar) for R-22
& R-407C. Do not operate with a restricted suction
or liquid line. Do not operate with the low pressure
cut-out disabled.
Never install a system in the field and
leave it unattended with no charge, a holding charge, or
with the service valves closed without securely locking
out the system. This will prevent unauthorized personnel
from accidentally ruining the compressor by operating
with no refrigerant flow.
As mentioned in the
Manifolded Applications
section,
attention must be given to compressor oil levels
when commissioning a new system and servicing an
existing system. Oil levels should be checked with the
compressor "off" and after the oil has had a chance
to equalize between the compressors (for manifolded
applications). If oil can't be seen in the sight-glass of the
compressor, add oil until the sight-glass is approximately
half full.
Field Trouble Shooting the Kriwan Module
Follow the steps listed below to trouble shoot the
module in the field. See wiring diagram
Figure 3
or in
terminal box cover.
1. De-energize control circuit and module power.
Remove the control circuit wires from the module
(Terminals M1 & M2). Connect a jumper across
these “control circuit” wires. This will bypass the
“control contact” of the module.
CAUTION ! The motor protection system within
the compressor is now bypassed. Use this
configuration to temporarily test module only.
Re-energize the control circuit and module power.
If the compressor will not operate with the jumper
installed, then the problem is external to the solid
state protection system.