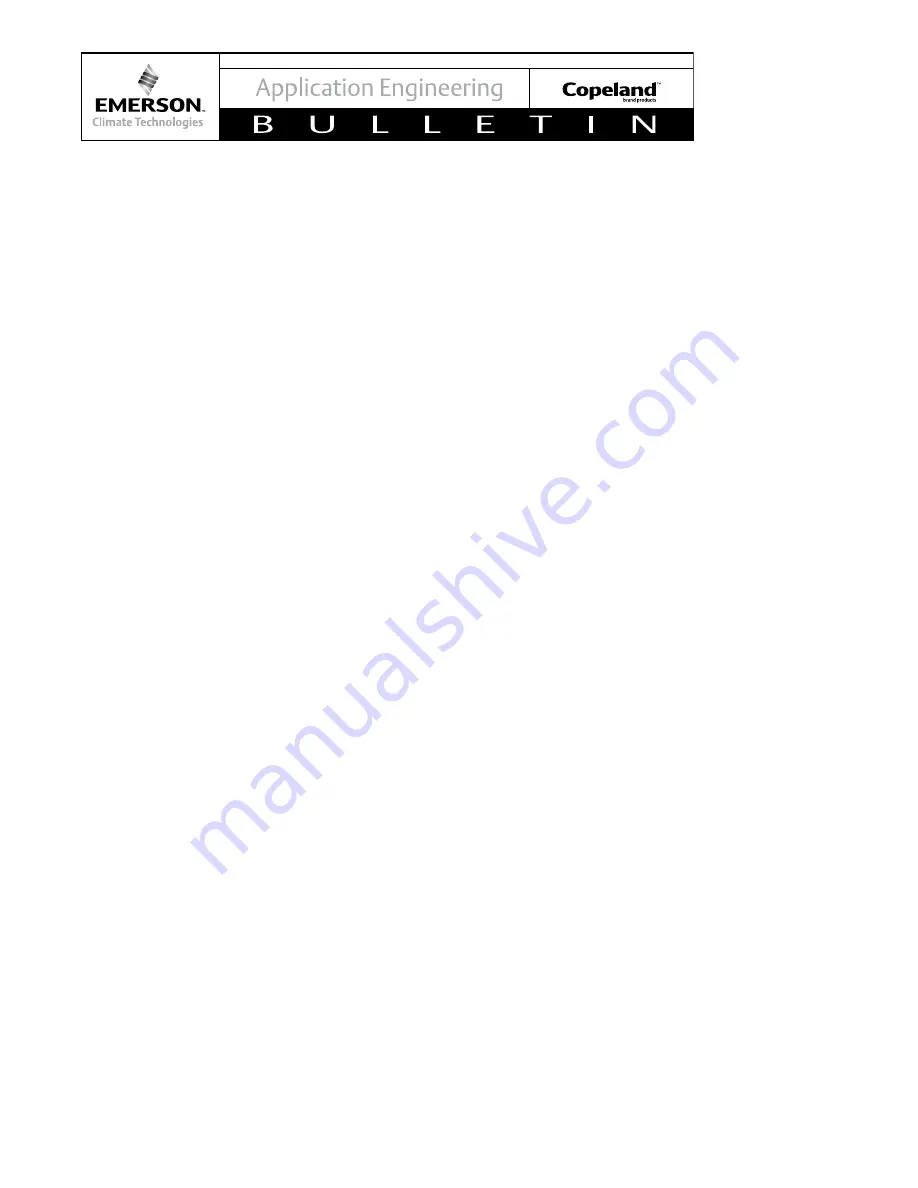
6
© 2016 Emerson Climate Technologies, Inc.
AE4-1303 R15
more effective it may be. If adequate attenuation is not
achieved, use a muffler with a larger cross-sectional
area to inlet-area ratio. The ratio should be a minimum
of 20:1 with a 30:1 ratio recommended. The muffler
should be from four to six inches (10 -15 cm) long.
Compressor Cycling
There is no set answer to how often scroll compressors
can be started and stopped in an hour, since it is
highly dependent on system configuration. There
is no minimum off time because Copeland Scroll
compressors start unloaded, even if the system has
unbalanced pressures. The most critical consideration
is the minimum run time required to return oil to the
compressor after startup. To establish the minimum
run time, obtain a sample compressor equipped with
a sight tube (available from Emerson) and install
it in a system with the longest connecting lines
that are approved for the system. The minimum on
time becomes the time required for oil lost during
compressor startup to return to the compressor sump
and restore a minimal oil level that will assure oil pick
up through the crankshaft.
The minimum oil level
required in the compressor is 1.5" (40 mm) below
the center of the compressor sight-glass.
Cycling
the compressor for a shorter period than this, for
instance to maintain very tight temperature control,
will result in progressive loss of oil and damage to the
compressor. See
AE17-1262
for more information on
preventing compressor short cycling.
Long Pipe Lengths / High Refrigerant Charge
Some systems may contain higher than normal
refrigerant charges. Systems with large reheat coils,
low ambient condenser flooding, or systems with
multiple heat exchangers are among some system
configurations that may require additional lubricant. For
compressors with sight-glasses for oil level viewing,
the oil level should always be checked during OEM
assembly, field commissioning, and field servicing. An
estimation of the amount of additional lubricant to add
to the compressor(s) when the circuit charge exceeds
20 pounds of refrigerant is as follows:
Single compressor application: 0.5 fluid ounce of oil per
pound of refrigerant over initial 20 pounds.
Tandem compressor application: 0.7 fluid ounce of oil
per pound of refrigerant over initial 20 pounds.
Trio compressor application: 1.0 fluid ounce of oil per
pound of refrigerant over initial 20 pounds.
Other system components such as shell and tube
evaporators can trap significant quantities of oil and
should be considered in overall oil requirements.
Reheat coils and circuits that are inactive during part of
the normal cycle can trap significant quantities of oil if
system piping allows the oil to fall out of the refrigerant
flow into the inactive circuit. The oil level must be
carefully monitored during system development, and
corrective action should be taken if the compressor
oil level falls more than 1.5" (40 mm) below the center
of the sight-glass.
The compressor oil level should
be checked with the compressor "off" to avoid the
sump turbulence when the compressor is running.
These compressors are available to the OEM with a
production sight-glass that can be used to determine the
oil level in the compressor in the end-use application.
These compressors are also available to the OEM with
an oil Schrader fitting on the side of the compressor to
add additional oil if needed because of long lengths of
piping or high refrigerant charge.
No attempt should
be made to increase the oil level in the sight-glass
above the 3/4 full level. A high oil level is not
sustainable in the compressor and the extra oil will
be pumped out into the system causing a reduction
in system efficiency and a higher-than-normal oil
circulation rate.
Suction & Discharge Line Noise and Vibration
Copeland Scroll
™
compressors inherently have low
sound and vibration characteristics. However, the sound
and vibration characteristics differ in some respects from
those of reciprocating compressors. In rare instances,
these could result in unexpected sound complaints.
One difference is that the vibration characteristics of
the scroll compressor, although low, include two very
close frequencies, one of which is normally isolated from
the shell by the suspension of an internally suspended
compressor. These frequencies, which are present in all
compressors, may result in a low level “beat” frequency
that may be detected as noise coming along the suction
line into the building under some conditions. Elimination
of the “beat” can be achieved by attenuating either
of the contributing frequencies. The most important
frequencies to avoid are 50 and 60 Hz power supply
line. This is easily done by using one of the common
combinations of design configuration described in
Table
3.
The scroll compressor makes both a rocking and
torsional motion, and enough flexibility must be provided
in the line to prevent vibration transmission into any lines