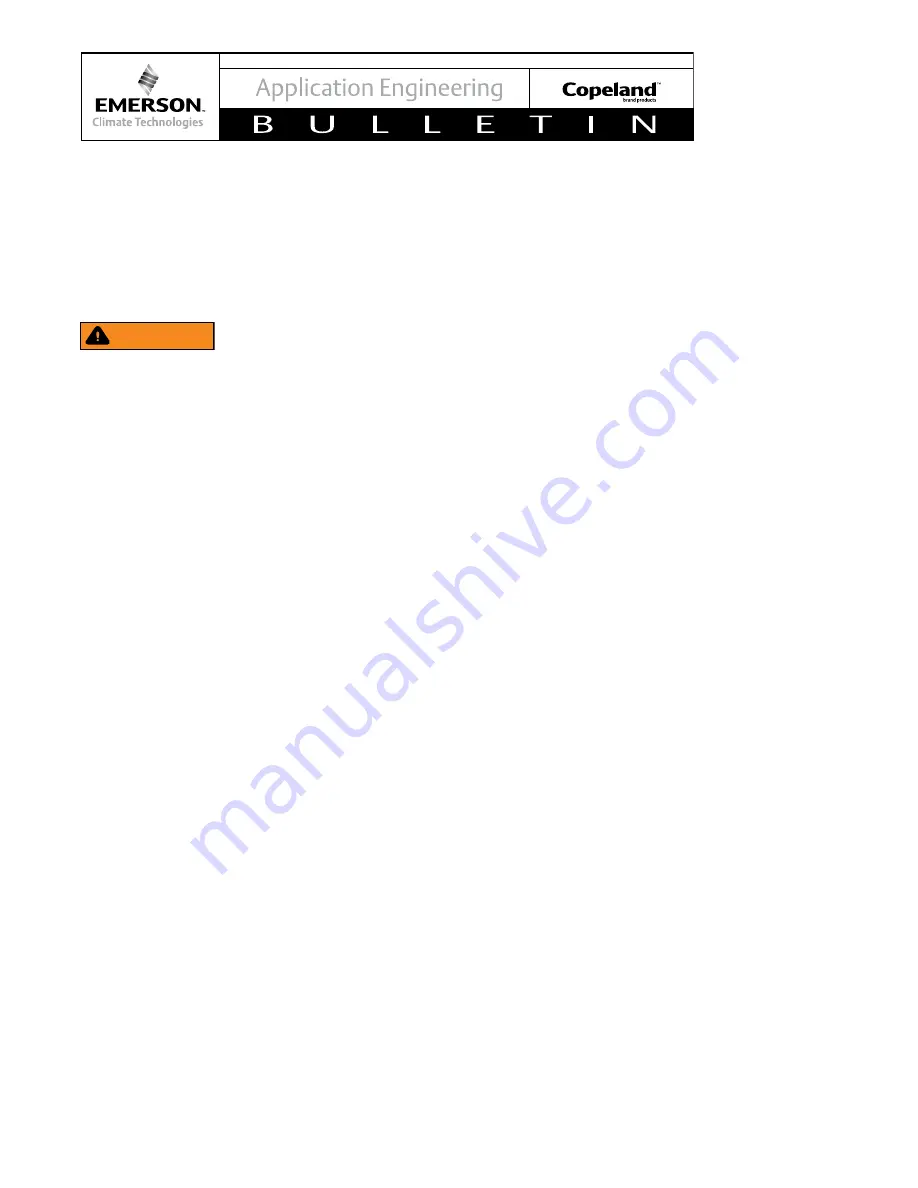
13
© 2016 Emerson Climate Technologies, Inc.
AE4-1402 R4
with high compression ratios and/or long test times.
Copeland Scroll compressors are designed for use
with refrigerant, and testing with nitrogen may result in
a situation where the compressor does not develop a
pressure differential (no pump condition). When testing
with nitrogen, the compressor must be allowed to cool
for several minutes between tests.
Unbrazing System Components
WARNING
Before attempting to braze, it is important to
recover all refrigerant from both the high and low
side of the system.
If the refrigerant charge is removed from a scroll-
equipped unit by recovering one side only, it is very
possible that either the high or low side of the system
remains pressurized. If a brazing torch is then used
to disconnect tubing, the pressurized refrigerant and
oil mixture could ignite when it escapes and contacts
the brazing flame. Instructions should be provided
in appropriate product literature and assembly (line
repair) areas. If compressor removal is required, the
compressor should be cut out of the system rather than
unbrazed. See
Figure 5
for proper compressor removal
procedure.
SERVICE PROCEDURES
The drive offers a two wire 485 interface. This enables
the drive set-up, operation and monitoring to be carrier
out with a PC or controller if required. The drive only
supports Modbus RTU protocol. Refer to the Emerson
EVC1 drive user guide for more information.
Electrical Troubleshooting
CAUTION The compressor must always have the
green ground wire attached to the ground. The
other end of the green wire must be connected to
the appropriate ground terminal on the drive.
The BPM motors used in the variable speed scrolls
are three-phase. The winding resistance for each
compressor-motor is published in the
Online Product
Information
. The three windings should always have
line to line continuity because there is no internal
overload at the center of the motor windings to open and
take the motor off-line. If one or more of the windings
shows continuity to ground, the compressor must be
replaced.
CAUTION Energizing a variable speed scroll with a
grounded winding can cause irreversible damage
to the drive.
Measuring the current in the three individual wires
feeding the compressor will provide no useful
information to the service technician, other than to show
that each winding of the compressor is drawing current.
The more appropriate measurement is the current input
to the drive. Current input to the drive can be compared
to the published values of MCC and RLA.
Compressor Replacement After a Motor Burn
In the case of a motor burn, the majority of contaminated
oil will be removed with the compressor. The rest of the
oil is cleaned with the use of suction and liquid line filter
driers. A 100% activated alumina suction filter drier is
recommended but must be removed after 72 hours. See
AE24-1105
for clean up procedures and
AE11-1297
for
liquid line filter-drier recommendations.
NOTICE
It is
highly recommended that the suction accumulator
be replaced if the system contains one.
This is
because the accumulator oil return orifice or screen may
be plugged with debris or may become plugged shortly
after a compressor failure. This will result in starvation of
oil to the replacement compressor and a second failure.
Start-Up of a New or Replacement Compressor
It is good service practice, when charging a system with
a scroll compressor, to charge liquid refrigerant into
the high side only. It is not good practice to dump liquid
refrigerant from a refrigerant cylinder into the crankcase
of a stationary compressor. If additional charge is
required, charge liquid into the low side of the system
with the compressor operating.
CAUTION
Do not
start the compressor while the system is in a deep
vacuum.
Internal arcing may occur when any type of
compressor is started in a vacuum.
NOTICE Do not
operate the compressor without enough system
charge to maintain at least 55 psig (3.8 bar) suction
pressure. Do not operate with a restricted suction
or liquid line. Do not operate with the low pressure
cut-out disabled.
Allowing suction pressure to drop
below 55 psig (3.8 bar) for more than a few seconds
may overheat the scrolls and cause early drive bearing
damage. Never install a system in the field and leave
it unattended with no charge, a holding charge, or with
the service valves closed without securely locking out
the system. This will prevent unauthorized personnel
from accidentally ruining the compressor by operating
with no refrigerant flow.