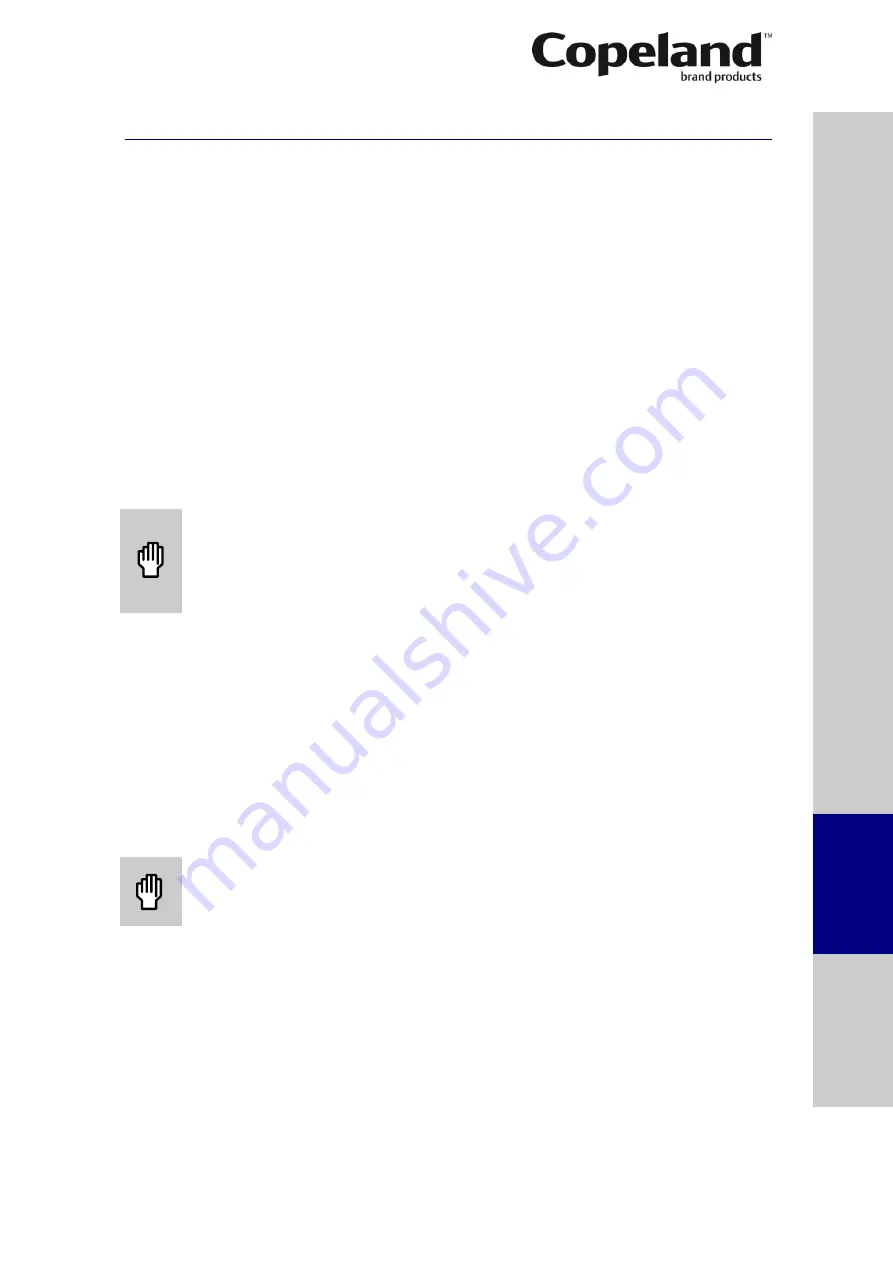
C6.3.1/0116-0716/E
21
6
Maintenance & repair
6.1 Exchanging the refrigerant
Qualified refrigerants and oils are given in Chapter 2.5.1.
It is not necessary to replace the refrigerant with new unless contamination due to an error such
as topping up the system with an incorrect refrigerant is suspected. To verify correct refrigerant
composition, a sample can be taken for chemical analysis. A check can be made during shut
down by comparing the refrigerant temperature and pressure using precision measurements at a
location in the system where liquid and vapour phases are present and when the temperatures
have stabilised.
In the event that the refrigerant needs replacing, the charge should be recovered using a
suitable recovery unit.
In the event that R22 in a system with mineral oil is to be replaced with an HFC refrigerant, the
oil must also be changed.
NOTE: Please refer to Technical Information CC7.26.1 "Refrigerant Changeover from
HCFC to HFC Refrigerants" and CC7.26.3 "Refrigerant Changeover from R404A/R507 to
HFC R407A, R407F, R448A, R449A".
6.2 Replacing a compressor
CAUTION
Inadequate lubrication! Bearing destruction!
Exchange the accumulator
after replacing a compressor with a burned out motor. The accumulator oil
return orifice or screen may be plugged with debris or may become plugged.
This will result in starvation of oil to the new compressor and a second
failure.
In the case of a motor burnout, the majority of contaminated oil will be removed with the
compressor. The rest of the oil is cleaned through the use of suction and liquid line filter driers. A
100% activated alumina suction line filter drier is recommended but must be removed after
72 hours.
It is highly recommended that the suction accumulator be replaced if the system
contains one.
This is because the accumulator oil-return orifice or screen may be plugged with
debris or may become plugged shortly after a compressor failure. This will result in starvation of
oil to the replacement compressor and a second failure. When a single compressor or tandem is
exchanged in the field, it is possible that a major portion of the oil may still be in the system.
While this may not affect the reliability of the replacement compressor, the extra oil will add to
rotor drag and increase power usage.
6.3 Lubrication and oil removal
CAUTION
Chemical reaction! Compressor destruction!
Do not mix up ester oils with
mineral oil and/or alkyl benzene when used with chlorine-free (HFC)
refrigerants.
The compressor is supplied with an initial oil charge. The standard oil charge for use with
refrigerants R404A, R407A, R407C, R407F, R448A, R449A, R450A, R507, R513A and R134a is
a polyolester (POE) lubricant Emkarate RL 32 3MAF. In the field the oil level could be topped up
with Mobil EAL Arctic 22 CC if 3MAF is not available. The standard mineral oil for R22 is Suniso
3GS.
One disadvantage of POE is that it is far more hygroscopic than mineral oil (see
Figure 19
).
Only brief exposure to ambient air is needed for POE to absorb sufficient moisture to make it
unacceptable for use in a refrigeration system. Since POE holds moisture more readily than
mineral oil it is more difficult to remove it through the use of vacuum. Compressors supplied by
Emerson Climate Technologies contain oil with low moisture content, and it may rise during the
system assembling process. Therefore it is recommended that a properly sized filter-drier is
installed in all POE systems. This will maintain the moisture level in the oil to less than 50 ppm. If
oil is charged into a system, it is recommended to use POE with moisture content no higher than
50 ppm.
S
afet
y
in
struct
ion
s
P
ro
d
u
ct
d
es
cr
ipt
ion
Inst
all
atio
n
E
lec
tr
ica
l
c
o
n
n
ec
tion
S
tar
ting
up
&
o
p
er
atio
n
Ma
int
enan
c
e &
repai
r
Dismant
ling
&
d
ispo
sa
l