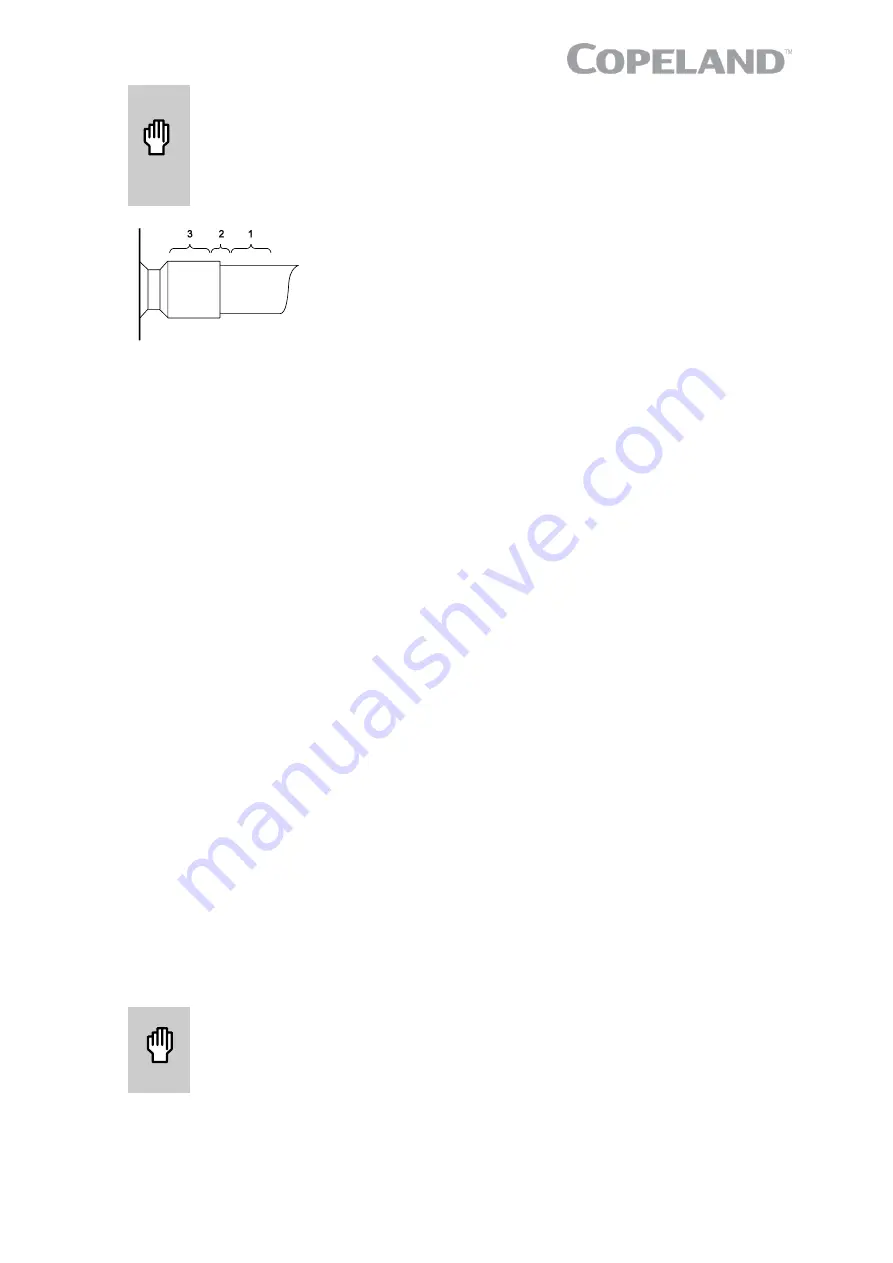
AGL_AC_ST_YRH_EN_Rev01
9
CAUTION
Blockage! Compressor breakdown!
Maintain a flow of oxygen-free nitrogen
through the system at very low-pressure during brazing. Nitrogen displaces
the air and prevents the formation of copper oxides in the system. If allowed
to form, the copper oxide material can later be swept through the system and
block screens such as those protecting capillary tubes, thermal expansion
valves, and accumulator oil return orifices.
Copeland scroll compressors have copper-plated steel
suction and discharge stub tubes. These stub tubes are far
more robust and less prone to leaks than copper tubes.
Brazing must be carried out in an appropriate manner, taking
into account the different thermal properties of steel and
copper.
Refer to
Figure 9
and procedure below for the brazing of the
stub tube connections of a scroll compressor.
▪
Flushing oxygen-free nitrogen through the piping during the brazing process is mandatory for
applications with flammable A2L and A3 refrigerants.
▪
The copper-coated steel tubes on scroll compressors can be brazed in approximately the same
manner as any copper tube.
▪
Recommended brazing materials: any Silfos material is recommended, preferably with a
minimum of 5 % silver. However, 0 % silver is acceptable.
▪
Be sure tube fitting inner diameter and tube outer diameter are clean prior to assembly.
▪
Using a double-tipped torch, apply heat in area 1.
▪
As the tube approaches brazing temperature, move the torch flame to area 2.
▪
Heat area 2 until braze temperature is attained, moving the torch up and down and rotating around
the tube as necessary to heat the tube evenly. Add braze material to the joint while moving the
torch around the joint to flow braze material around the circumference.
▪
After the braze material flows around the joint, move the torch to heat area 3. This will draw the
braze material down into the joint. The time spent heating area 3 should be minimal.
▪
As with any brazed joint, overheating may be detrimental to the final result.
NOTE: Since the discharge stub contains a check valve, care must be taken not to overheat
it to prevent brazing material from flowing into it.
3.4 Pressure safety controls
Emerson requires the installation of low- and high-pressure controls, preferably direct acting, for all
transport systems.
3.4.1 High-pressure protection
Applicable regulations and standards, for example EN 378-2, shall be followed to apply appropriate
control and ensure that the pressure never exceeds the maximum limit.
High-pressure protection is required to stop the compressor operating outside the allowable pressure
limits. The high-pressure control must be installed correctly, which means that no service valve is
allowed between the compressor and the pressure protection.
The high-pressure cut-out setting shall be determined according to the applicable standard, the type
of system, the refrigerant and the maximum allowable pressure PS.
3.4.2 Low-pressure protection
CAUTION
Operation outside the application envelope! Compressor breakdown!
A
low-pressure protection shall be fitted in the suction line to stop the
compressor when it operates outside the envelope limits. Do not bridge or by-
pass the low-pressure limiter.
Applicable regulations and standards shall be followed to apply appropriate control and ensure that
the pressure is always above the required minimum limit.
Figure 9: Brazing areas