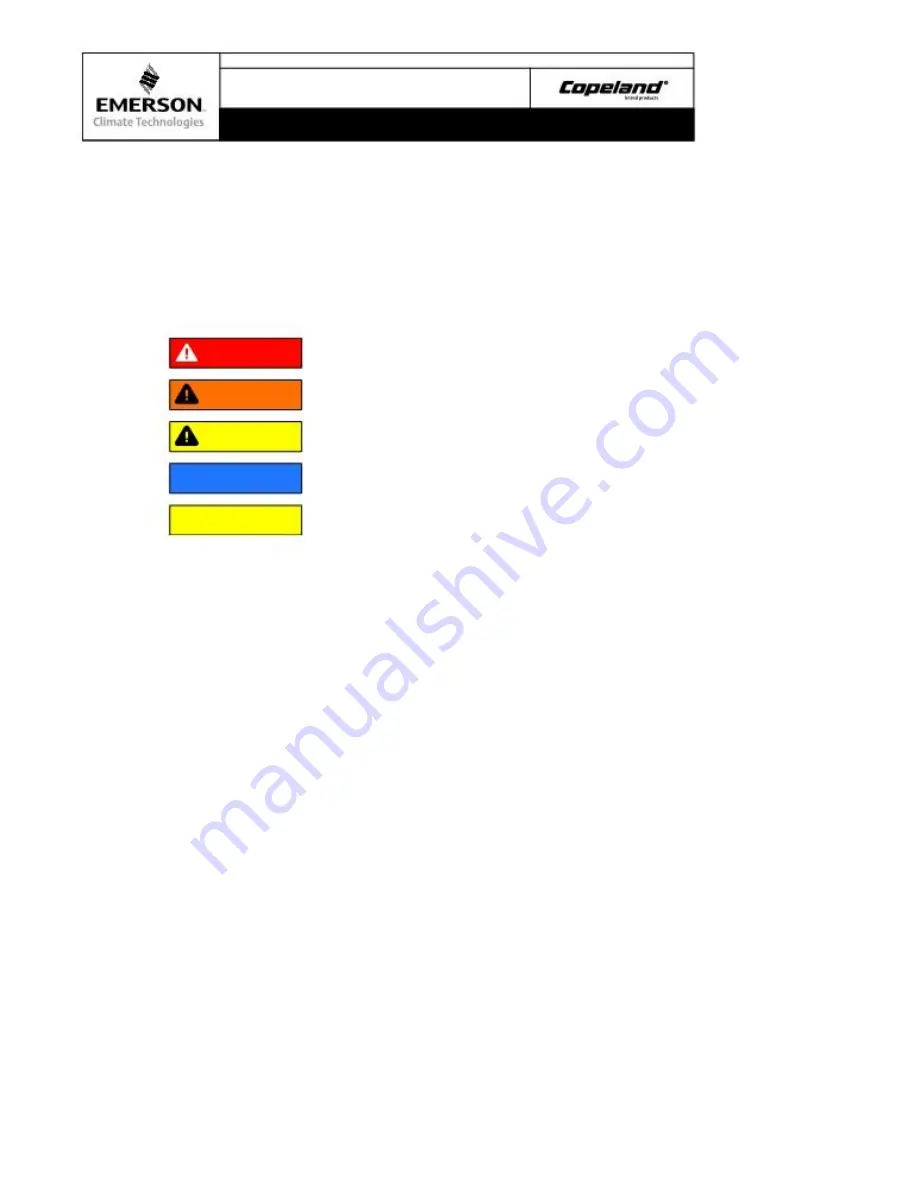
Application Engineering
B U L L E T I N
AE4-1374 R1
Safety Instructions
Copeland Scroll
™
compressors are manufactured according to the latest U.S. and European Safety
Standards. Particular emphasis has been placed on the user's safety. Safey icons are explained below and
safety instructions applicable to the products in this bulletin are grouped on Page 3. These
instructions should be retained throughout the lifetime of the compessor. You are strongly advised to follow
these safety instructions.
Safety Icon Explanation
DANGER
WARNING
CAUTION
NOTICE
CAUTION
© 2013 Emerson Climate Technologies, Inc.
Printed in the U.S.A.
DANGER indicates a hazardous situation which, if not avoided, will result in
death or serious injury.
WARNING indicates a hazardous situation which, if not avoided, could
result in death or serious injury.
CAUTION, used with the safety alert symbol, indicates a hazardous
situation which, if not avoided, could result in minor or moderate injury.
NOTICE is used to address practices not related to personal injury.
CAUTION, without the safety alert symbol, is used to address practices not
related to personal injury.
2