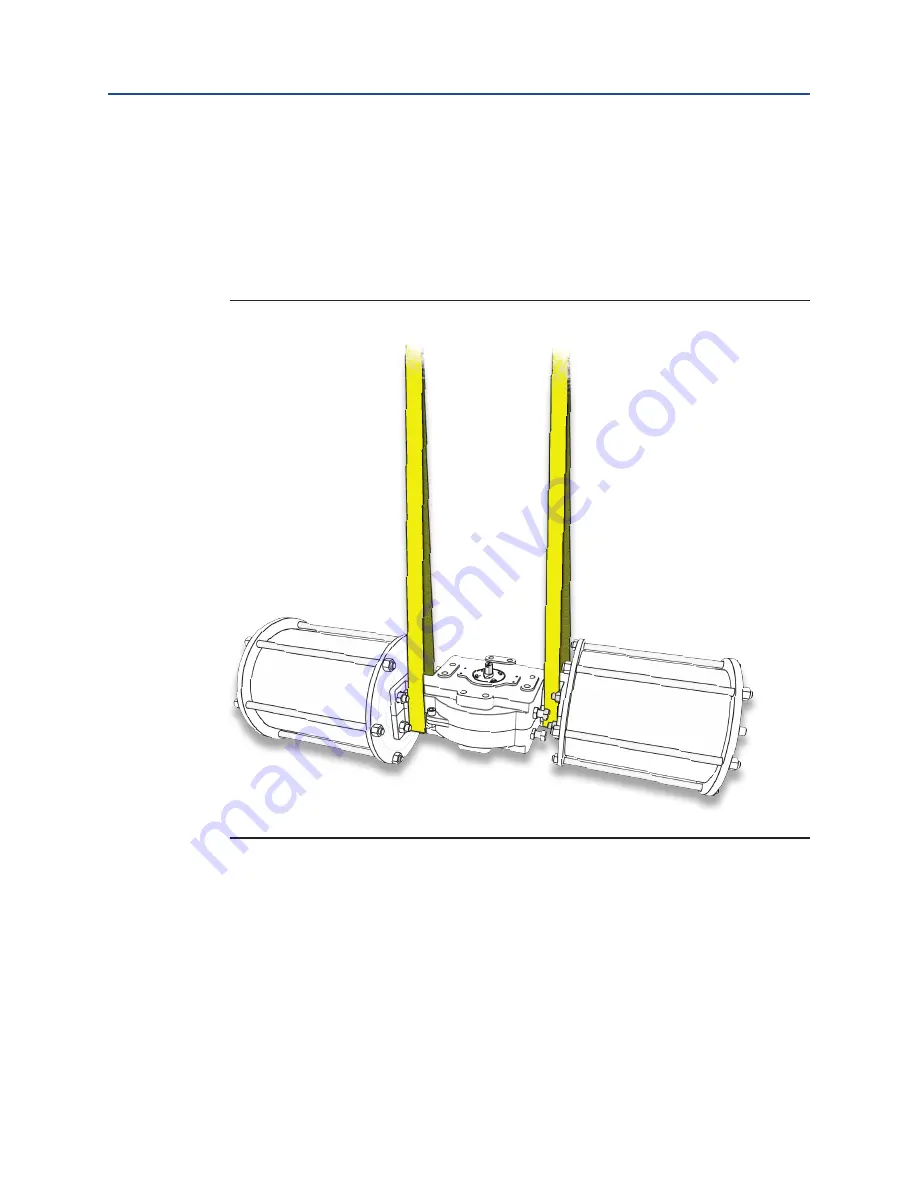
Installation, Operation and Maintenance Manual
RGS011110-3 Rev. 0
November 2015
2
Section 2: Installation
Installation
Section 2: Installation
Bettis actuators may be mounted in any position/orientation. If necessary, lift the actuator
with straps placed inside the framework of the body. Never lift the actuator by the cylinders,
tie rods, or travel stops. Lifting the actuator with the valve attached is not generally
recommended.
Figure 1