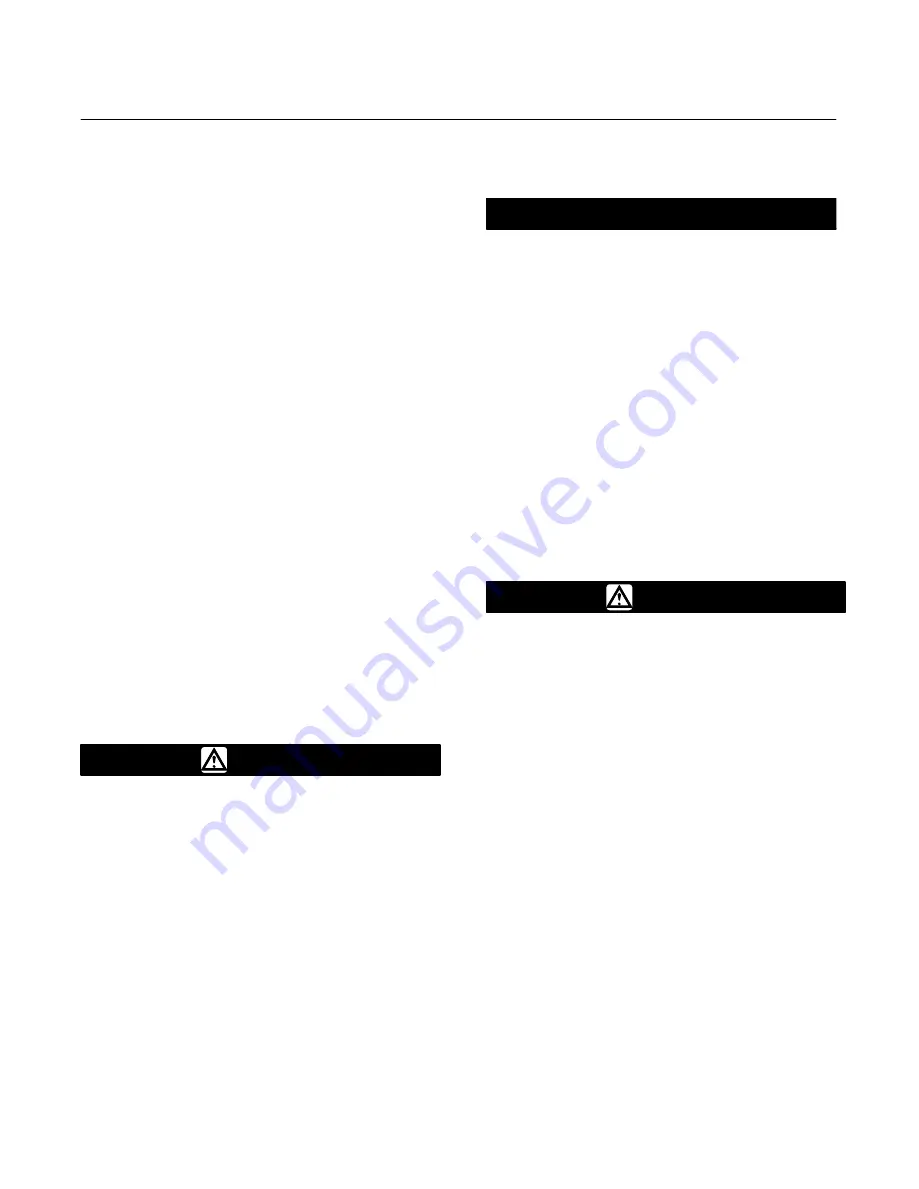
CV500 Valve
Instruction Manual
Form 5302
July 2006
14
shown in figures 11 and 12, making certain the
necessary clearance exists. Compare the measured
gap to the clearance in table 4; proceed as follows:
D
If the measured clearance is within table
values, proceed to the next step.
D
If the measured gap is larger than the
maximum, tighten the retainer--apply more torque
than that listed in figure 7, if necessary, until the
clearance is within maximum and minimum values.
D
If the measured clearance is smaller than the
minimum, remove the retainer, seat ring, and face
seals, clean the parts, and reassemble so as to
obtain the necessary minimum clearance.
10. Perform the Adjusting Actuator Travel procedure
in this manual and then install the control valve in
the pipeline.
Replacing Ball, Shaft, and Bearings
Perform this procedure to replace the ball (key 2),
expansion pin (key 9), taper pin (key 10), drive shaft
(key 3), follower shaft (key 38), groove pins (key 39),
or bearings (keys 6 and 42). These parts are
independently replaceable; for example, installing a
new ball does not require replacing a reusable valve
shaft or expansion pin assembly. For key numbers
refer to figure 11 for 3- through 8-inch sizes and to
figure 12 for 10- and 12-inch sizes unless otherwise
indicated.
Disassembly
WARNING
To avoid personal injury resulting from
contact with edges of the V-notch ball
(key 2) and seat ring (key 4) during ball
rotation, stay clear of its edges when
rotating the ball. To avoid damage to
tools, valve parts, or other items
resulting from V-notch ball rotation,
keep tools and other property away
from the edges of the ball.
The ball closes with a shearing,
cutting motion, which could result in
personal injury. When the actuator is
removed from the valve, the ball/shaft
assembly may suddenly rotate,
resulting in personal injury or property
damage. To avoid injury or damage,
carefully rotate the ball/shaft assembly
to a stable position in the valve body
after the actuator is disconnected.
CAUTION
To avoid increased leakage, increased
valve component wear or possible
damage to the valve body (key 1), ball
(key 2), drive shaft (key 3), follower
shaft (key 38), and bearings (keys 6
and 42) resulting from a sharp blow to
the actuator or valve parts, use a
wheel puller to separate the actuator
parts from the valve drive shaft.
Do not drive the actuator parts off the
valve drive shaft since this could move
the valve bearings, shafts, and ball
away from proper alignment, causing
improper seating of the ball. Such
misalignment may result in damage to
valve components if the valve is
returned to service without
disassembly and inspection of the ball
alignment.
WARNING
Refer to the WARNING at the
beginning of the Maintenance section
in this instruction manual.
1. Isolate the control valve from the line pressure,
release pressure from both sides of the valve body,
and drain the process media from both sides of the
valve. If using a power actuator, also shut-off all
pressure lines to the power actuator, release all
pressure from the actuator. Use lock-out procedures
to be sure that the above measures stay in effect
while you work on the equipment.
2. Remove the actuator cover. Note the actuator
orientation with respect to the valve body and the
lever orientation with respect to the valve drive shaft
(see figure 3). Remove the lever but do not loosen
the actuator turnbuckle adjustment. Remove the
actuator mounting screws and nuts, and remove the
actuator. If necessary, refer to the actuator
instruction manual for assistance.
3. With the valve body (key 1) out of the pipeline,
loosen the packing nuts (key 16). If the packing is to
be reused, do not remove it. However, Emerson
Process Management recommends that the packing
be replaced whenever the drive shaft is removed.
4. Rotate the V-notch ball (key 2) to the fully open
position.