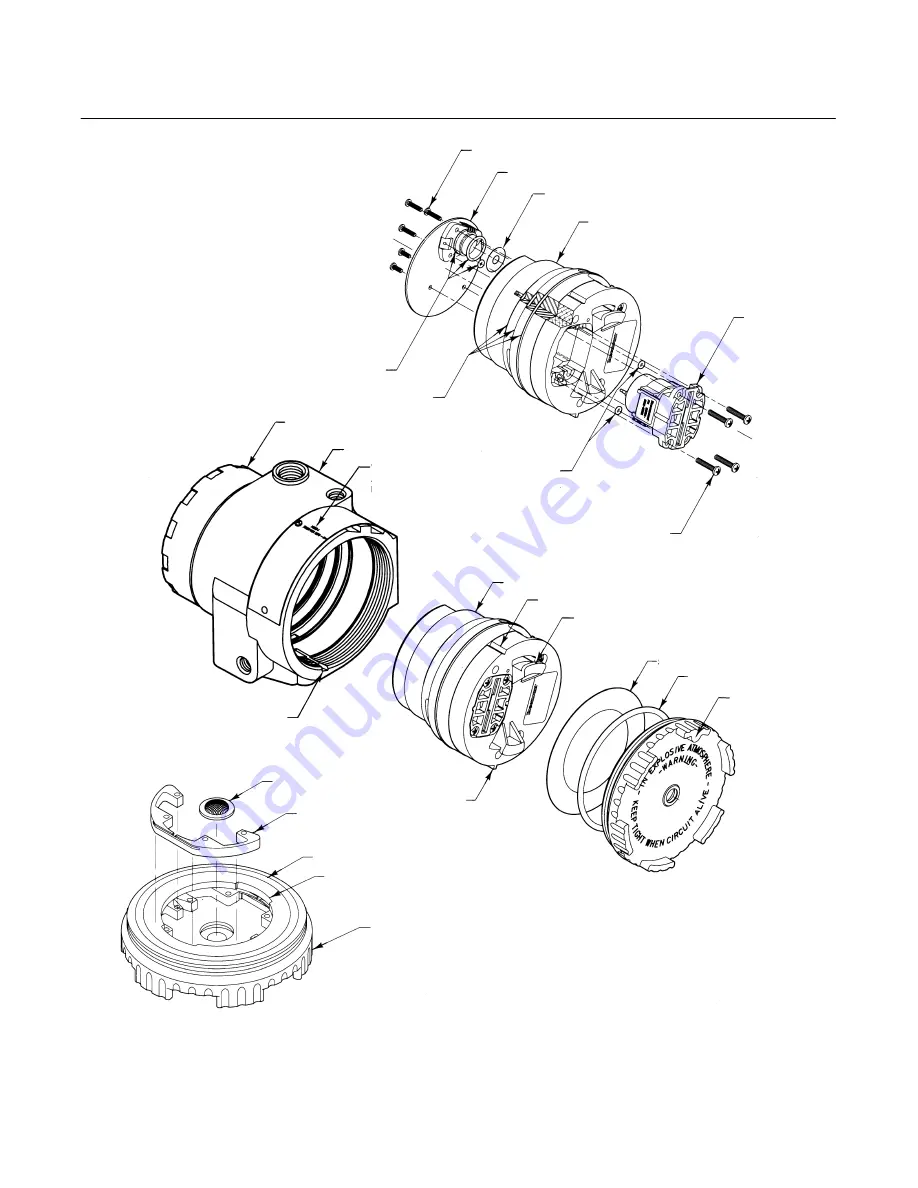
Type 846 and Model 3311
Instruction Manual
Form 5739
February 2002
6–2
Figure 6-1. Type 846 and Model 3311 Exploded View
ELECTRONIC CIRCUIT BOARD SCREWS
ELECTRONIC CIRUIT BOARD
SENSOR SEAL
MODULE SUBASSEMBLY
PILOT/ACTUATOR
ASSEMBLY
PILOT/ACTUATOR
ASSEMBLY SCREWS
PILOT/ACTUATOR
ASSEMBLY O-RINGS
MODULE
O-RINGS
ELECTRONIC
CIRCUIT BOARD O-RINGS
TERMINAL COVER
MODULE HOUSING
V-GROOVE
ALIGNMENT
MARK
MODULE FINAL ASSEMBLY
V-GROOVE
MODULE FEET
SLIP RING
O-RING
MODULE COVER
INDICATING BOSS
ALIGNMENT KEY
MODULE COVER
COVER SLOT (2)
O-RING CLIP
RETAINING CLIP (2)
STROKE PORT
SCREEN
KEY SLOT
C0790/IL