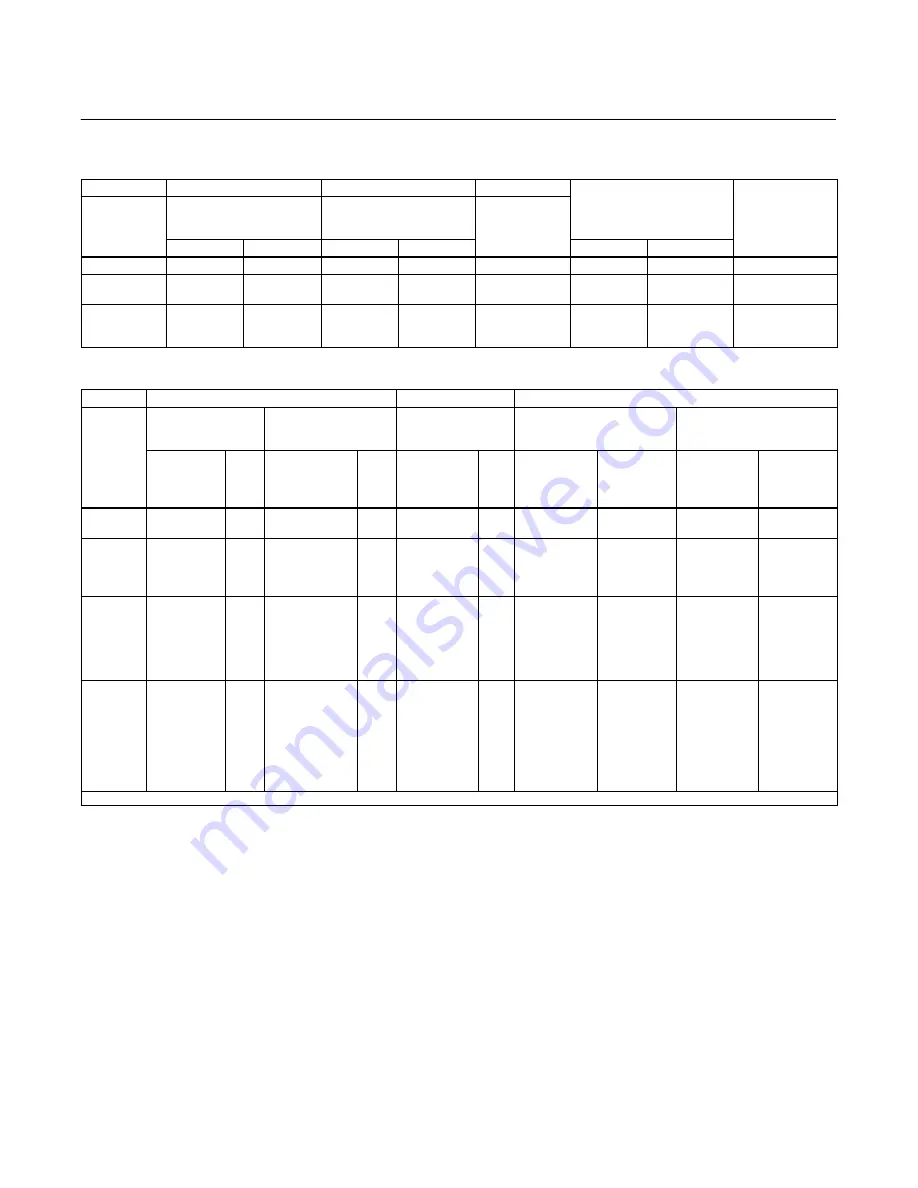
3660 and 3661 Positioners
Instruction Manual
Form 5265
March 2006
22
Table 6. Range Spring Selection for Fisher
R
Actuators
TYPE
3660
3660
3661
VALVE STEM TRAVEL
WHEN USING
TYPES 3660 AND 3661
RANGE SPRING
PART NUMBER
(KEY 30)
Split
0.2 to 1.0 bar
(3 to 15 psig)
Input Signal
0.4 to 2.0 bar
(6 to 30 psig)
Input Signal
4 to 30 mAdc
Input Signal
Bar
Psig
Bar
Psig
mm
Inches
One Way 1:1
0.2 to 1.0
3 to 15
0.4 to 2.0
6 to 30
4 to 20
20 to 50
0.787 to 1.969
11B3880X012
Two Way 2:1
0.2 to 0.6
0.6 to 1.0
3 t0 9
9 to 15
0.4 to 1.2
1.2 to 2.0
6 to 18
18 to 30
4 to 12
12 to 20
20 to 50
0.787 to 1.969
11B3881X012
Three Way
3:1
0.2 to 0.5
0.5 to 0.8
0.8 to 1.0
3 to 7
7 to 11
11 to 15
0.4 to 1.0
1.0 to 1.5
1.5 to 2.0
6 to 14
14 to 22
22 to 30
4 to 9.33
9.33 to 14.66
14.66 to 20
15 to 33.3
0.591 to 1.311
11B3881X012
Table 7. Range Spring Selection for Baumann
t
Actuators
TYPE
3660
3661
VALVE STEM TRAVEL
Split
0.2 to 1.0 bar
(3 to 15 Psig)
Input Signal
0.4 to 2.0 bar
(6 to 30 Psig)
Input Signal
4 to 20 mA dc
Input Signal
12.7 to 19.1 mm
(1/2 to 3/4 inch)
19.1 to 50 mm
(3/4 to 2 inch)
Range
Bar
(Psig)
Span
Bar
(Psi)
Range
Bar
(Psig)
Span
Bar
(Psi)
Range
mA
Span
mA
Range Spring
Part Number
(key 30)
Approximate
Pilot Shaft
Setting
mm (Inch)
Range Spring
Part Number
(key 30)
Approximate
Pilot Shaft
Setting
mm (Inch)
One Way
1:1
0.2 to 1.0
(3 to 15)
0.8
(12)
0.4 to 2.0
(6 to 30)
1.6
(24)
4 to 20
16
17B0662X012
89 (3.50)
17B0662X012
129 (5.09)
Two Way
2:1
0.2 to 0.6
(3 to 9)
0.6 to 1.0
(9 to 15)
0.4
(6)
0.5 to 1.2
(6 to 18)
1.2 to 2.0
(18 to 30)
0.8
(12)
4 to 12
12 to 20
8
11B3880X012
92 (3.63)
11B3881X012
92 (3.63)
Three Way
3:1
0.2 to 0.5
(3 to 7)
0.5 to 0.8
(7 to 11)
0.8 to 1.0
(11 to 15)
0.3
(4)
0.5 to 1.0
(6 to 14)
1.0 to 1.5
(14 to 22)
1.5 to 2.0
(22 to 30)
0.6
(8)
4 to 9.33
9.33 to 14.66
14.66 to 20
5.33 11B3881X012
70 (2.75)
11B3881X012
137 (5.38)
Four Way
4:1
0.2 to 0.4
(3 to 6)
0.4 to 0.5
(6 to 9)
0.5 to 0.8
(9 to 12)
0.8 to 1.0
(12 to 15)
0.2
(3)
0.5 to 0.8
(6 to 12)
0.8 to 1.2
(12 to 18)
1.2 to 1.6
(18 to 24)
1.6 to 2.0
(24 to 30)
0.4
(6)
4 to 8
8 to 12
12 to 16
16 to 20
4
11B3881X012
95 (3.75)
−
−
−
−
−
−
1. Pilot shaft setting is the A dimension in figure 20.
8. Release all pressure from the positioner. Remove
the plug or the gauge that was installed in step 4,
and reconnect the output tubing to the actuator.
9. Turn on supply pressure. Set the input signal to
the minimum value.
10. Remove the cover (key 19T) from the feedback
lever assembly (key 19).
11. Set the travel (span) adjustment to the desired
actuator travel by loosening the hex nut (key 19D)
and sliding the pilot shaft (key 19A) to the desired
setting on the feedback lever assembly (key 19).
The travel settings are marked in millimeters on the
feedback lever assembly.
12. Set the gain (PB) adjustment and/or the output
volume damping adjustment to a setting that
provides the best actuator/positioner response.
Observe the gain dependency on the air supply
pressure as shown in the graph of figure 19. The
gain adjustment restrictor for air delivery should be
fully open for large size actuators and adjusted to a
mid-value for smaller size actuators with 225 cm
2
(35 square inches) or less diaphragm area. Start by
setting the gain adjustment at approximately one
turn open, and, if the output volume damping
adjustment is used, turn it clockwise to decrease the
air delivery.
13. Adjust the valve stem position by rotating the
zero adjustment screw (key 19S).