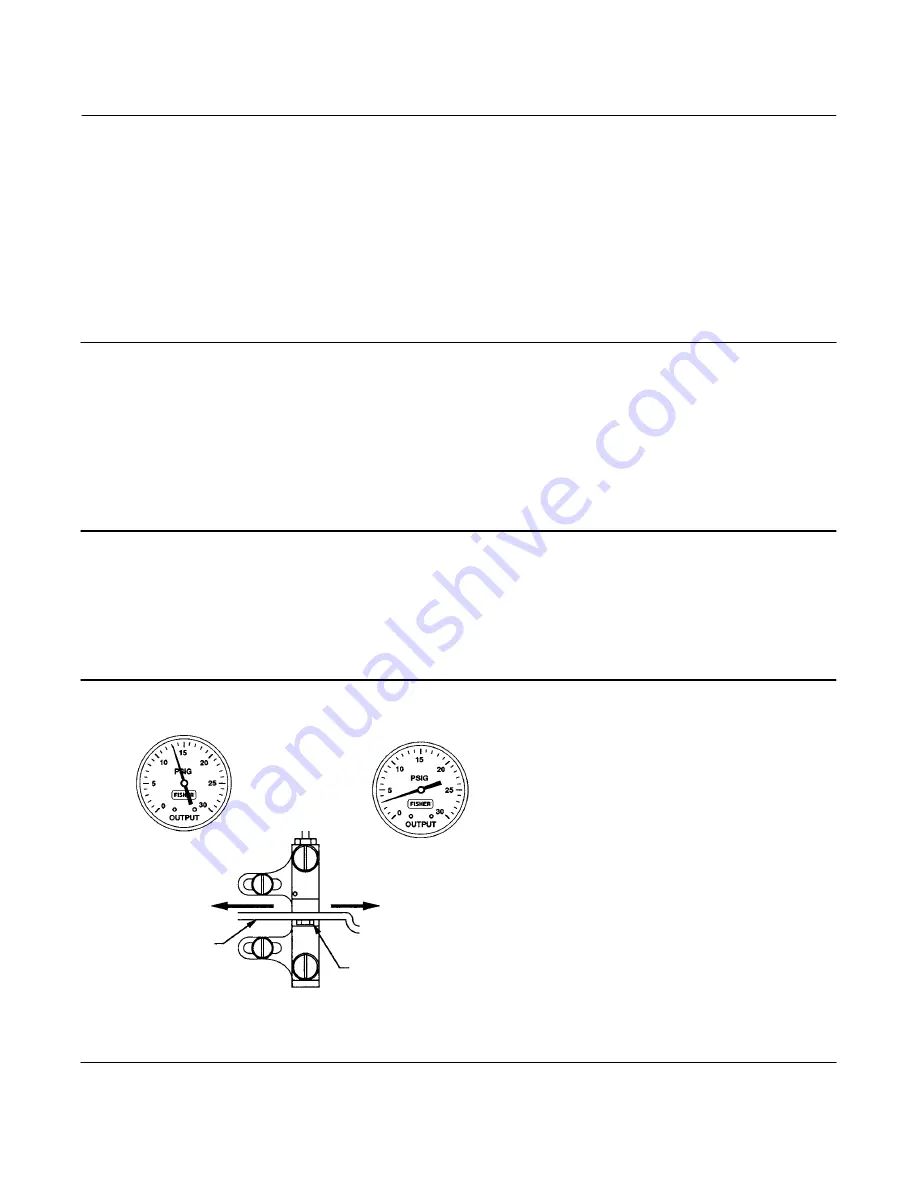
Instruction Manual
D103292X012
C1 Controllers and Transmitters
March 2017
13
For reverse-acting controllers:
4. Apply an input pressure equal to the sensing element upper range value.
5. Rotate the pressure setting knob to the maximum value.
6. Adjust the nozzle (key 54) until the controller output pressure is between 0.6 and 0.7 bar (8 and 10 psig).
7. Apply an input pressure equal to the sensing element lower range value.
8. Rotate the pressure setting knob to the minimum value.
Note
When performing the span adjustment in step 9, do not watch the output gauge while changing the calibration adjuster. The
change in output is not a good indication of the change in span. While moving the calibration adjuster, the output pressure may
change in the opposite direction than expected. For example, while moving the calibration adjuster to increase span, the output
pressure may decrease. This should be disregarded since even though the output pressure decreases, the span is increasing.
Proper controller response depends on nozzle-to-flapper alignment.
When performing span adjustments, carefully loosen both calibration adjuster screws while holding the calibration adjuster in
place. Then move the calibration adjuster slightly in the required direction by hand or using a screwdriver. Verify proper
nozzle-to-flapper alignment and hold the calibration adjuster in place while tightening both adjustment screws.
9. If the output is not between 0.6 and 0.7 bar (8 and 10 psig), adjust the controller span by loosening the two
10. Repeat steps 4 through 9 until no further adjustment is necessary.
11. Proceed to the startup procedure for proportional controllers.
Figure 5. Reverse-Acting Controller Span Adjustment — Proportional-Only Controllers
IF OUTPUT IS:
ABOVE
8 TO 10 PSIG
(0.6 TO 0.7 BAR)
BELOW
8 TO 10 PSIG
(0.6 TO 0.7 BAR)
MOVE ADJUSTER
LEFT
MOVE ADJUSTER
RIGHT
FLAPPER
NOZZLE
NOTE:
3 TO 15 PSIG (0.2 TO 1.0 BAR) OUTPUT SHOWN.
FOR 6 TO 30 PSIG (0.4 TO 2.0 BAR) OUTPUT, ADJUST
VALUES AS APPROPRIATE.
A6155-1