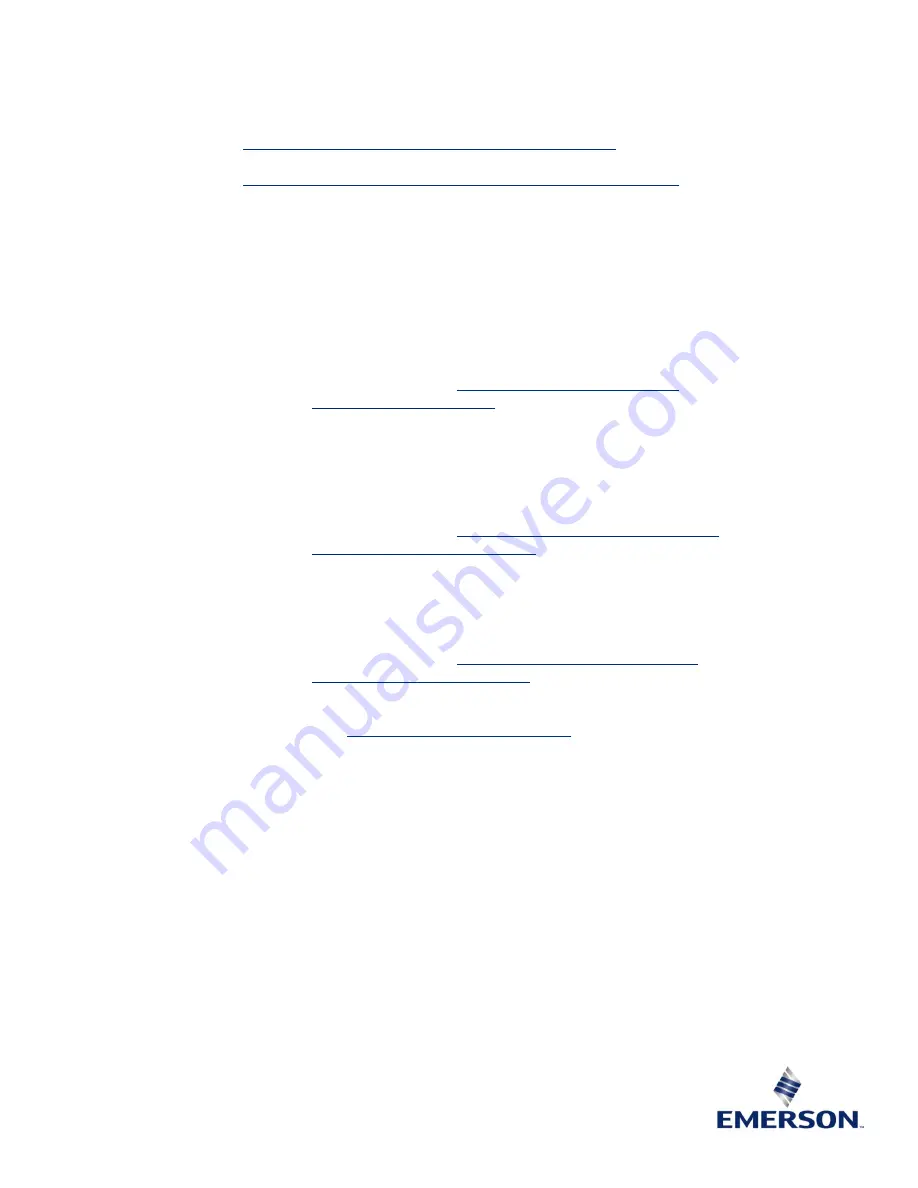
General Contact Information
Home link:
http://www.emerson.com/industrial-automation-controls
Knowledge Base:
https://www.emerson.com/industrial-automation-controls/support
Technical Support
Americas
Phone:
1-888-565-4155
1-434-214-8532 (If toll-free option is unavailable)
Customer Care (Quotes/Orders/Returns):
Europe
Phone:
+800-4444-8001
+420-225-379-328 (If toll-free option is unavailable)
+39-0362-228-5555 (from Italy - if toll-free 800 option is unavailable or dialing from a mobile telephone)
Customer Care (Quotes/Orders/Returns):
customercare.emea.mas@emerson.com
Asia
Phone:
+86-400-842-8599
+65-6955-9413 (All other Countries)
Customer Care (Quotes/Orders/Returns):
customercare.cn.mas@emerson.com
Any escalation request should be sent to:
mas.sfdcescalation@emerson.com
Note: If the product is purchased through an Authorized Channel Partner, please contact the seller directly for any
support.
Emerson reserves the right to modify or improve the designs or specifications of the products mentioned in this manual at
any time without notice. Emerson does not assume responsibility for the selection, use, or maintenance of any product.
Responsibility for proper selection, use, and maintenance of any Emerson product remains solely with the purchaser.
© 2022 Emerson. All rights reserved.
Emerson Terms and Conditions of Sale are available upon request. The Emerson logo is a trademark and service mark of
Emerson Electric Co. All other marks are the property of their respective owners.