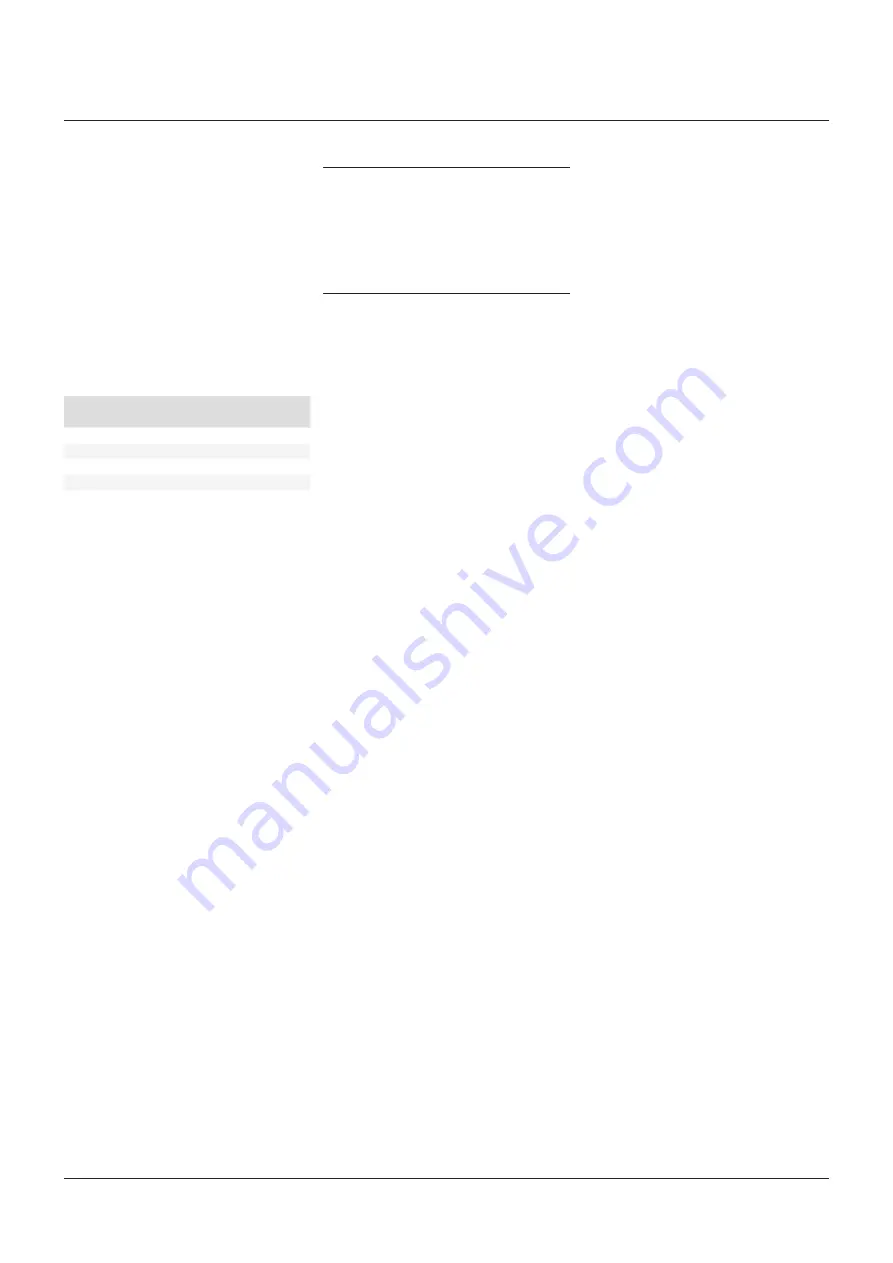
3
PENBERTHY
MULTIVIEW
TM
TOP MOUNT MAGNETIC GAGE
INSTALLATION, OPERATION AND MAINTENANCE INSTRUCTIONS
3.4 Indicator alignment
To change the direction the indicator is facing,
loosen the clamps holding the indicator to the
communicating chamber, rotate the indicator
to the position desired, and tighten the clamps.
This procedure should only be done when the
vessel is empty or the indicator is currently
registering a '0' level indication. To align the
indicator use the following procedure:
Follower style
1. Loosen the clamps holding the indicator
to the communicating chamber. Move the
indicator down as far as it will go.
2. Move the indicator so that the center line on
the magnetic follower is aligned with 'zero'
on the calibrated scale. If you do not have
a scale the bottom of the follower should
just touch the cushion in the bottom of the
hermetically-sealed tube.
3. Tighten the clamps.
Flag style
1. Loosen the clamps holding the indicator
to the communicating chamber. Move the
indicator down as far as it will go.
2. Move the indicator until the last visible gold
flag has rotated to black. This will be the
third flag from the bottom (two flags are
hidden behind the nameplate). Be careful
not to raise the indicator too far.
3. Tighten the clamps.
3.3 Installation
1. A minimum distance of 8" should be
maintained from the centerline of the
standpipe to the nearest source of
ferromagnetic material.
2. Support the float and float tube. Damage to
either of these components will adversely
affect the performance of your TMMG.
3. Carefully insert the float, float tube and float
guide system (if present) through the vessel
connection flange.
4. Align the bolt pattern in the TMMG flange
with the vessel flange.
5. Connect the two flanges together using
standard piping procedures.
Minimum vessel opening requirements
Float diameter (mm)
Min. flange connection
3.5" (89)
4"
4.5" (114)
6"
6" (152)
6"
8" (203)
8"
10" (254)
10"
Minimum connection sizes assume the use of a
Schedule 10 stilling well equal to the flange size. If a
higher schedule or the Penberthy guide system is
used, the minimum connection must be increased
by one pipe size.
4 START-UP
1. Check the connections between the
communicating chamber and the vessel to
insure proper mating.
2. Check for any leaks at the connections. If
none are observed, the unit is ready for use.
5 PERIODIC MAINTENANCE
Your Penberthy top mount magnetic gage
(TMMG) is designed to give you years of reliable
service. However, equipment failure can occur.
Sound maintenance practices require periodic
inspection of the gage to ensure it is in good
working order.
The end user must determine the appropriate
maintenance schedule based upon his or
her experience for the specific application.
Realistic maintenance schedules can only be
determined with full knowledge of the services
and applications involved.
WARNING
Do not proceed with any maintenance if the
magnetic gage is still at operating pressure or
temperature. Relieve the unit of pressure or
vacuum, allow it to reach ambient temperature,
and purge or drain it of all fluids. Failure to do
so could result in personal injury or property
damage.