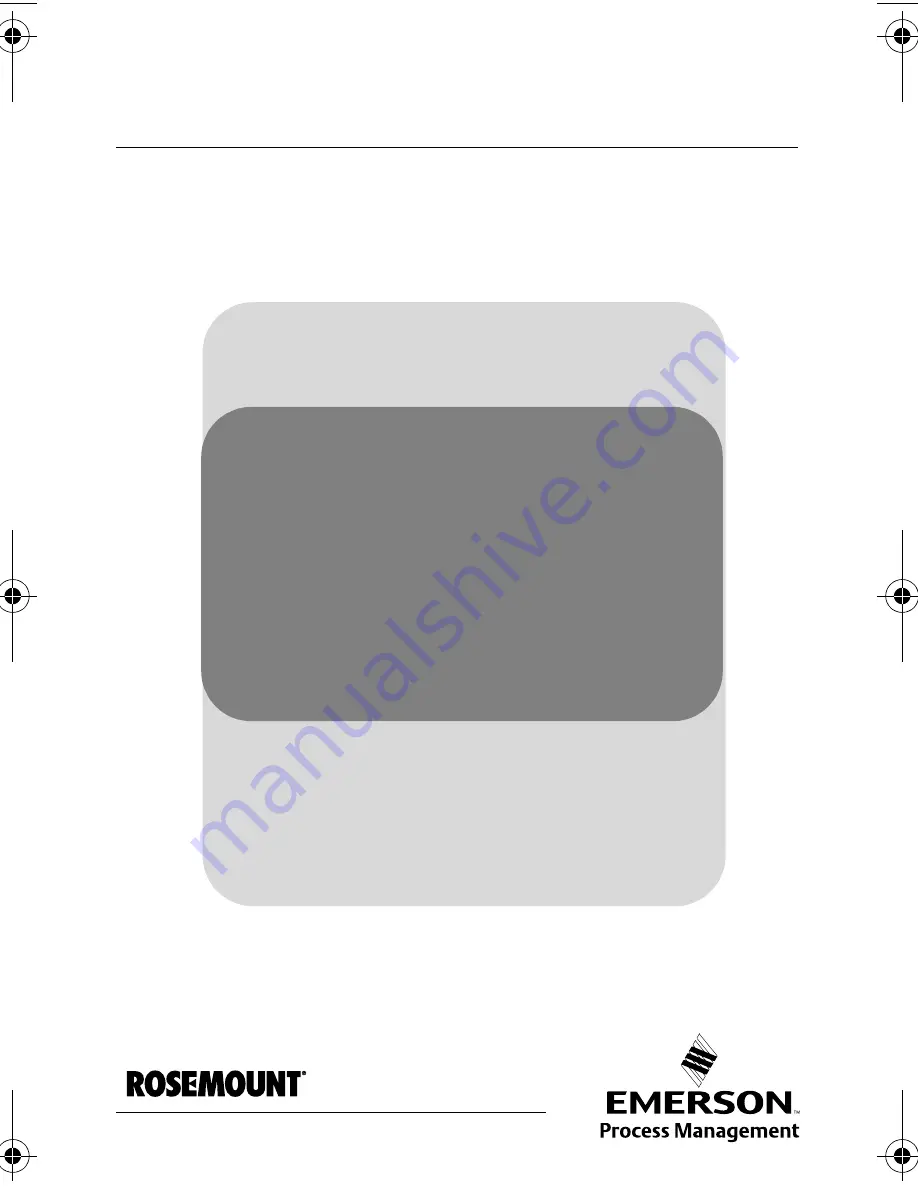
Quick Installation Guide
00825-0500-4809, Rev CA
September 2003
Threaded Flo-Tap 485 Annubar
www.rosemount.com
¢00825-0500-4809{¤
HART
®
Rosemount 485 Annubar
®
Threaded
Flo-Tap Assembly
Step 1: Location and Orientation
Step 2: Weld Mounting Hardware
Step 3: Install Isolation Valve
Step 4: Mount Drilling Machine and Drill Hole
Step 5: Remove Drilling Machine
Step 6: Mount the Annubar
Step 7: Insert the Annubar
Step 8: Mount the Transmitter
Step 9: Retracting the Annubar
4809-0500 Rev CA.fm Page 1 Monday, September 22, 2003 11:14 AM