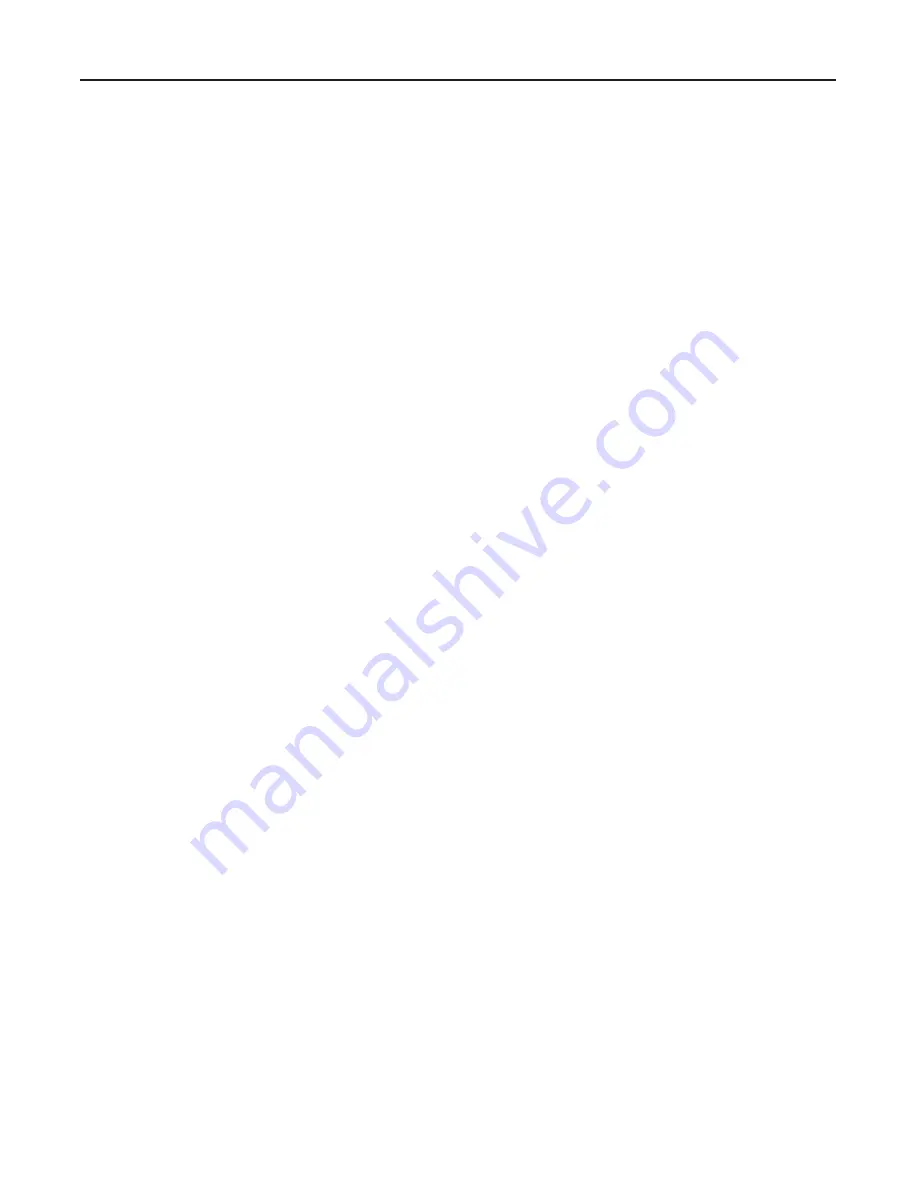
Y690VB Series
2
Diaphragm and Spring Case Area
This procedure is for gaining access to the control
spring, diaphragm, and lever assembly stem. All
pressure must be released from the diaphragm case
assembly before performing the following steps. Key
numbers are referenced in figures 3 and 4.
To Change the Control Spring:
1. Remove the closing cap (key 22), and turn the
adjusting nut (key 20) counterclockwise to remove all
compression from the control spring (key 6).
2. Change the control spring to match the desired
spring range.
3. Install the upper spring seat (key 19) and the
adjusting nut (key 20), turning clockwise until there is
enough control spring (key 6) force to provide proper
slack to the diaphragm (key 10). Using a crisscross
pattern, finish tightening the cap screws (key 24) and
hex nuts (key 23,
not shown)
to 160 to 190 inch-
pounds (22 to 26 N•m) of torque. When finished, turn
the adjusting nut (key 20) to the desired outlet
pressure setting.
4. Install a replacement closing cap gasket (key 25), if
necessary, and reinstall the closing cap (key 22).
5. If the spring range was changed, be sure to
change the stamped spring range on the spring case
nameplate.
To Disassemble and Reassemble
Diaphragm Parts:
Use this procedure to gain access to the control spring,
diaphragm assembly, valve stem, and stem O-ring. All
pressure must be released from the diaphragm case
assembly before performing these steps. Key numbers
are referenced in figures 3 and 4.
1. Remove the closing cap (key 22) and the adjusting
nut (key 20).
2. Remove the hex nuts (key 23, not shown) and cap
screws (key 24), lift off the spring case assembly
(key 3) and remove the control spring (key 6).
3. Remove the diaphragm (key 10) plus attached
parts by tilting them so that the pusher post (key 8)
• Replace the Diaphragm and Spring Case Area Maintenance section beginning on page 4 with the
following:
slips off the lever assembly (key 16). To separate the
diaphragm assembly (key 10) from the attached parts,
unscrew the diaphragm hex nut (key 21) from the
pusher post (key 8). If the only further maintenance is
to replace the diaphragm parts, skip to step 7.
4. To replace the lever assembly (key 16), remove
the machine screws (key 17). To replace the stem
(key 14) on Types Y690VB and Y690VBM or stem seal
(key 30, figure 4) on Type Y690VBM, perform Body
Area Maintenance procedure steps 1 and 4, and pull
the stem (key 14) out of the guide insert (key 18).
5. Install the stem (key 14) into the guide insert
(key 18) and perform Body Area Maintenance
procedure steps 5 through 7 as necessary.
6. Install the lever assembly (key 16) into the stem
(key 14) and secure the lever assembly with the
machine screws (key 17).
7. Reassemble the diaphragm parts as follows:
• Pusher post (key 8)
• Diaphragm head gasket (key 45)
• Diaphragm head (key 7)
• Diaphragm (key 10)
• Diaphragm head (key 7)
• Washer (key 36)
• Diaphragm nut (key 21)
Secure using 5 to 6 foot-pounds (7 to 8 N•m) of torque.
8. Install the pusher post (key 8) plus attached
diaphragm parts onto the lever assembly (key 16).
9. Install the spring case (key 3) on the diaphragm
casing (key 4) so that the vent assembly (key 26) is
correctly oriented, and secure with the cap screws
(key 24) and hex nuts (key 23, not shown) fingertight.
10. Install upper spring seat (key 19), the control
spring (key 6), and the adjusting nut (key 20), turning
clockwise until there is enough control spring (key 6)
force to provide proper slack to the diaphragm (key
10). Using a crisscross pattern, finish tightening the
cap screws (key 24) and hex nuts (key 23,
not shown)
to 160 to 190 inch-pounds (22 to 26 N•m) of torque.
When finished, turn the adjusting nut to the desired
outlet pressure setting.
11. Install a replacement closing cap gasket (key 25)
if necessary, and then install the closing cap (key 22).