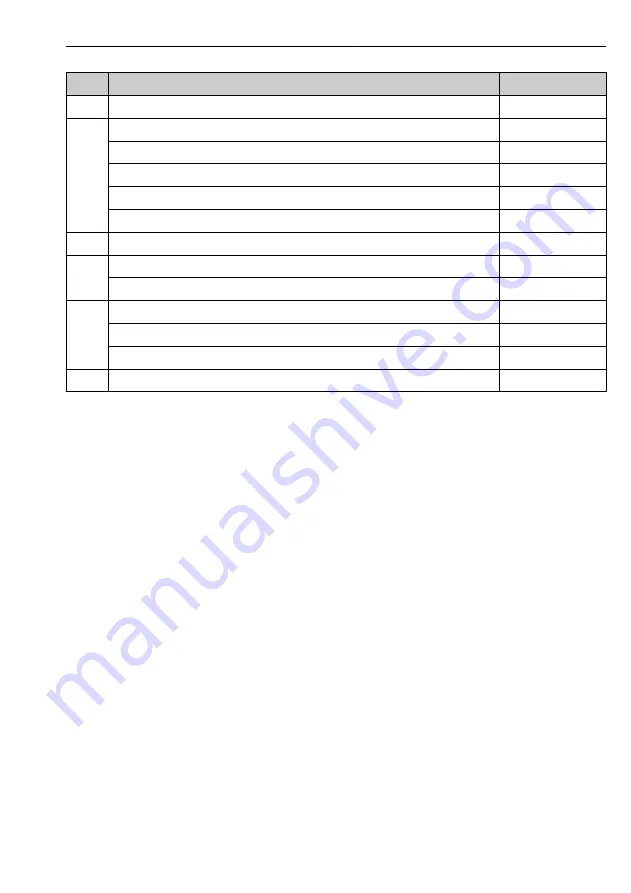
ASP Station 2000 RPS20B
Repair
Hauser
51
Item
Designation
Order number
31
Kit RPS20B: Temp. sensor wet compartment
71257697
None
Kit RPS20B: Flange dosing unit cond. cpl.
71257691
Kit RPS20B: Retrofit kit, heating bottom
71257673
Kit RPS20B: 3 contact cable
71257689
Kit RPS20B: Locking handle dosing system
71257690
Kit RPS20B: Locking handle bolt cpl.
71257693
32
Kit RPS20B: Rotary tap drive cpl
71257699
33
Kit RPS20B: Rotary tap cpl. + adapter
71257700
Kit RPS20B: Adapter rotary tap
71257698
None
Kit RPS20B: Cable set rotary tap
71257701
Kit RPS20B: Terminal board
71257702
Kit RPS20B: Air filter for membrane pump
71257688
Kit RPS20B: Dosing hose 15x2
71259919
12.2 Return
The sampler is repaired on site.
Contact your Hauser Service.
12.3 Disposal
The device contains electronic components. The product must be disposed of as electronic
waste.
‣
Observe the local regulations.