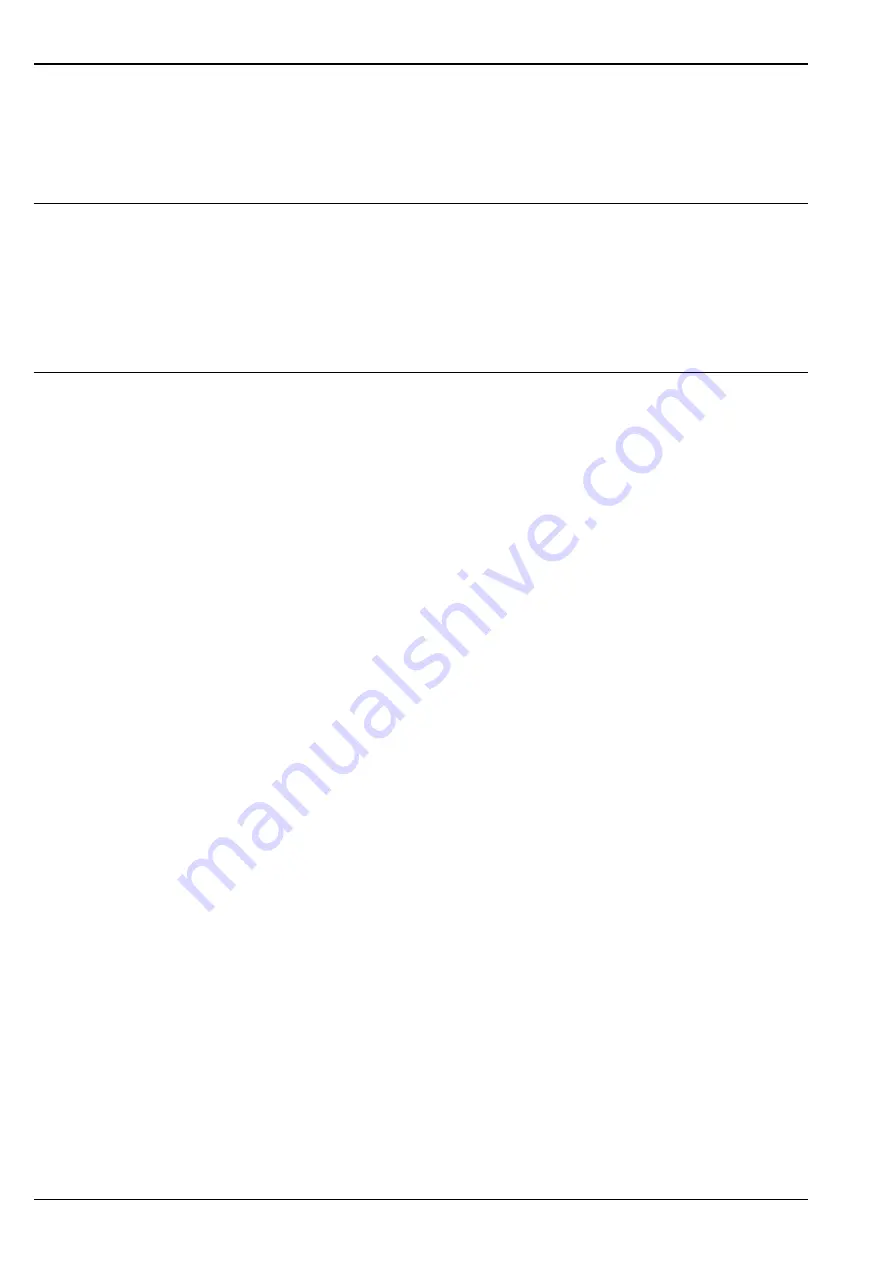
Deltabar S
58
Hauser
Planning instructions, diaphragm seal systems
With the Endress Hauser selection tool "Applicator" you will find the optimum diaphragm seal for your
application. Online on "www.endress.com/applicator" or offline (on CD)
For further information please contact your local Hauser Sales Center.
Applications
Diaphragm seal systems should be used if the process media and the device should be separated. Diaphragm
seal systems offer clear advantages in the following instances:
• In the case of high process temperatures (
28, section "Process temperature limits".)
• In the case of process media that crystallise
• In the case of corrosive or highly various process media or process media with solids content
• In the case of heterogeneous and fibrous process media
• If good and rapid measuring point cleaning is necessary
• If the measuring point is exposed to vibrations
• For mounting locations that are difficult to access
Design and operation mode
Diaphragm seals are separating equipment between the measuring system and the process medium.
A diaphragm seal system consists of:
• A diaphragm seal in a one-sided system, e.g. FMD77 or two diaphragm seals, in a two-sided system, e.g.
FMD78
• One capillary tube or two capillary tubes
• Fill fluid and
• A differential pressure transmitter.
The process pressure acts via the process isolating diaphragm of the diaphragm seal on the liquid-filled system,
which transfers the process pressure via the capillary tube onto the sensor of the differential pressure
transmitter.
Hauser delivers all diaphragm seal systems as welded versions. The system is hermetically sealed,
which ensures the highest reliability.
Note!
The correlations between the individual diaphragm seal components are presented in the following section.
For further information and comprehensive diaphragm seal system designs, please contact your local
Hauser Sales Center.
Diaphragm seal
The diaphragm seal determines the application range of the system by
• the process isolating diaphragm diameter
• the process isolating diaphragm stiffness and material
• the design (oil volume).
Diaphragm diameter
The larger the diaphragm diameter (less stiffness), the smaller the temperature effect on the measurement
result.
Note: To keep the temperature effect in practice-oriented limits, you should select diaphragm seals with a
nominal diameter of
DN 80, in as far as the process connection allows for it.
Diaphragm stiffness
The stiffness is dependent on the process isolating diaphragm diameter, the material, any available coating and
on the diaphragm thickness and shape. The diaphragm thickness and the shape are defined constructively. The
stiffness of a process isolating diaphragm of the diaphragm seal influences the temperature operating range and
the measuring error caused by temperature effects.
Capillary
Diaphragm seals are used with the following capillary internal diameters as standard:
•
DN 50: 1 mm
• > DN 50: 2 mm
The capillary tube influences the T
K
zero point, the ambient temperature operating range and the response time
of a diaphragm seal system as a result of its length and internal diameter.
60 ff, sections "Influence of the temperature on the zero point", "Ambient temperature range" and