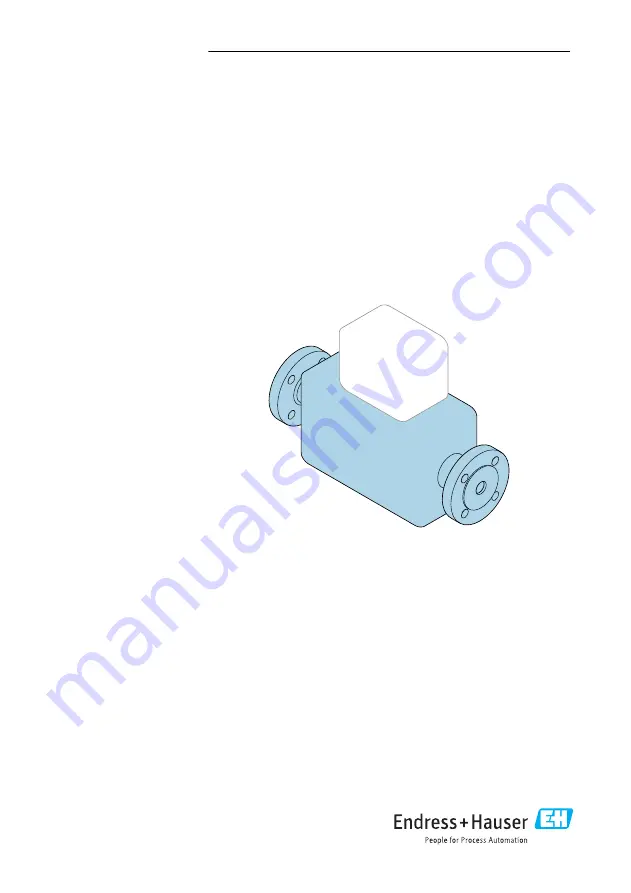
Products
Solutions
Services
Brief Operating Instructions
Proline Prosonic Flow P
Ultrasonic time-of-flight sensor
These instructions are Brief Operating Instructions; they are
not
a substitute for the Operating Instructions pertaining to
the device.
Brief Operating Instructions part 1 of 2: Sensor
Contain information about the sensor.
Brief Operating Instructions part 2 of 2: Transmitter
KA01474D/06/EN/01.21
71508892
2021-05-10
Summary of Contents for Proline Prosonic Flow P
Page 39: ......