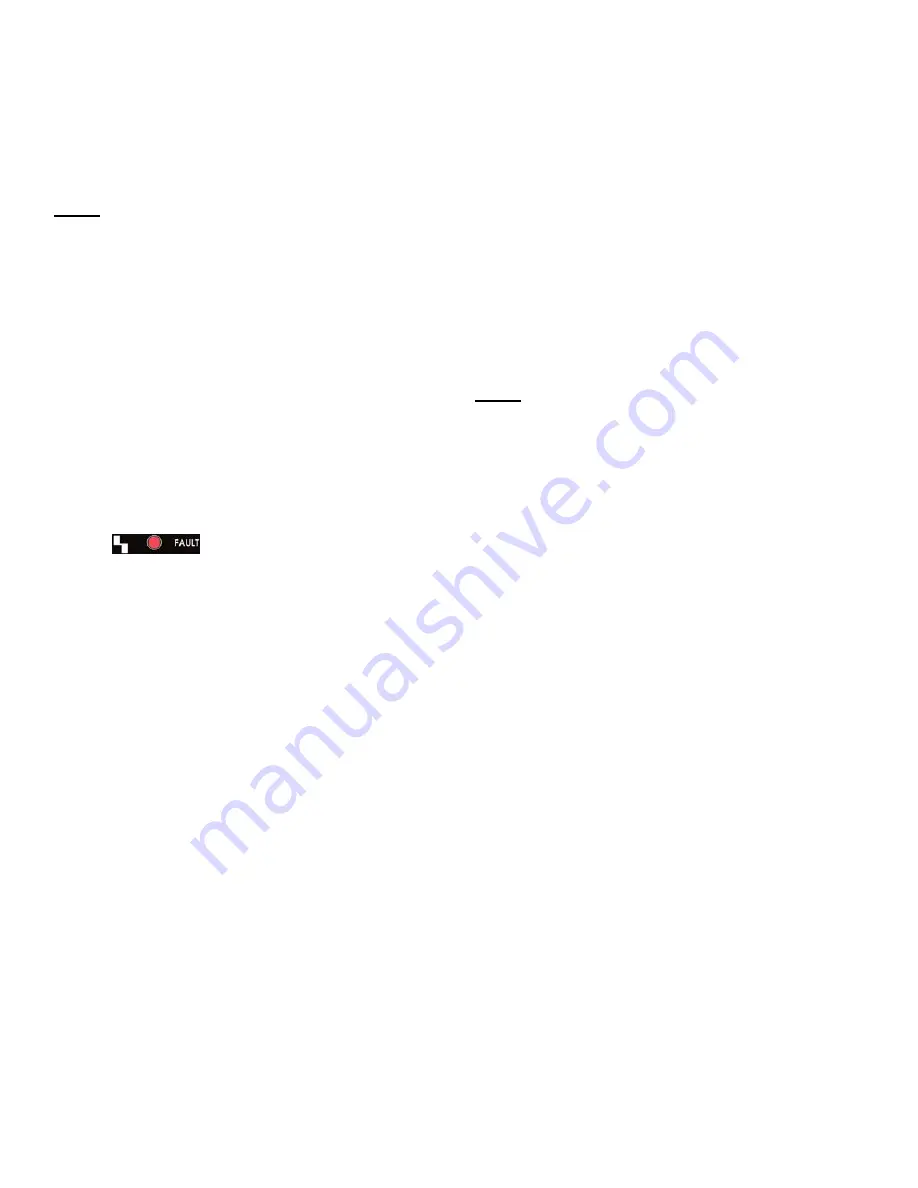
ML0071-601-06 Super Seal™ Operations Manual Rev. A
ENERCON INDUSTRIES
35
a. Remove the power supply cover, following the
Removal
portion of the
REMOVE / INSTALL
THE POWER SUPPLY COVER
procedure.
b. Replace the boards one at a time and perform
Step 3c after replacing each board. Refer to
your system drawings to ensure the boards are
reconnected correctly.
NOTE:
When replacing the Control/Display board, take care
to ensure the pushbuttons align correctly with the
front cover cutouts.
c. Reinstall the power supply cover, following the
Reinstallation
portion of the
REMOVE /
INSTALL THE POWER SUPPLY COVER
procedure. Do not reinstall the cover screws
until you have tested the system.
d. If the issue is resolved, complete the power
supply cover reinstallation. If the issue is not
resolved, replace the remaining board and
continue troubleshooting.
If none of these steps resulted in a resolution of your
problem, contact Enercon Customer Service for
information on Repair or Service.
FAULT
Symptoms:
The
FAULT
LED is lit when the START pushbutton
is pressed, and the power supply will not start.
Possible Causes:
1. Failed Inverter
2. Failed Control / Display board, or a failed Power /
Connector board.
Solutions:
1. Failed Inverter
a. Remove the power supply cover, following the
Removal
portion of the
REMOVE / INSTALL
THE POWER SUPPLY COVER
procedure.
b. Inspect the condition of the wires around the
Inverter device. Refer to your system drawings
to confirm and correct any wiring issues.
c. Perform the Inverter Ohm check procedure on
Page 38
.
If the
inverter passes
the ohm check,
proceed to Step 2.
If the
inverter fails
the ohm check, refer to
your system drawings and replace the
inverter and continue with Step d.
d. Reinstall the power supply cover, following the
Reinstallation
portion of the
REMOVE /
INSTALL THE POWER SUPPLY COVER
procedure, but do not reinstall the hardware at
this time.
e.
Test the system to ensure the issue is
resolved.
f. If the issue is resolved, complete the power
supply cover reinstallation. If the issue is not
resolved, continue troubleshooting.
2.
Failed Control / Display Board, or a Failed
Power / Connector Board
The following can only be performed if you have
spare boards on hand.
a. Remove the power supply cover, following the
Removal
portion of the
REMOVE / INSTALL
THE POWER SUPPLY COVER
procedure.
b. Replace the boards one at a time and perform
Step 3c after replacing each board. Refer to
your system drawings to ensure the boards are
reconnected correctly.
NOTE:
When replacing the Control/Display board, take care
to ensure the pushbuttons align correctly with the
front cover cutouts.
c. Reinstall the power supply cover, following the
Reinstallation
portion of the
REMOVE /
INSTALL THE POWER SUPPLY COVER
procedure. Do not reinstall the cover screws
until you have tested the system.
d. If the issue is resolved, complete the power
supply cover reinstallation. If the issue is not
resolved, replace the remaining board and
continue troubleshooting.
If none of these steps resulted in a resolution of your
problem, contact Enercon Customer Service for
information on Repair or Service.
PUSHBUTTONS DO NOT FUNCTION
Symptoms:
The symptoms you see will vary depending upon the
cause of this issue.
Improperly installed, or loose, Control/Display
Board:
What you see depends upon which button is
in contact with the cover.
The output meter may not flash upon power up of the
power supply.
The output level may also run up to 100%, or down
to the power supply’s minimum output level.
If you press the pushbutton(s) that is in contact with
the cover it, will typically not depress or spring back.
Failed Control/Display Board:
In this case the
symptoms will be dictated by what has failed on the
board.
If a pushbutton has failed or broken, the symptoms
may only affect that pushbuttons function.