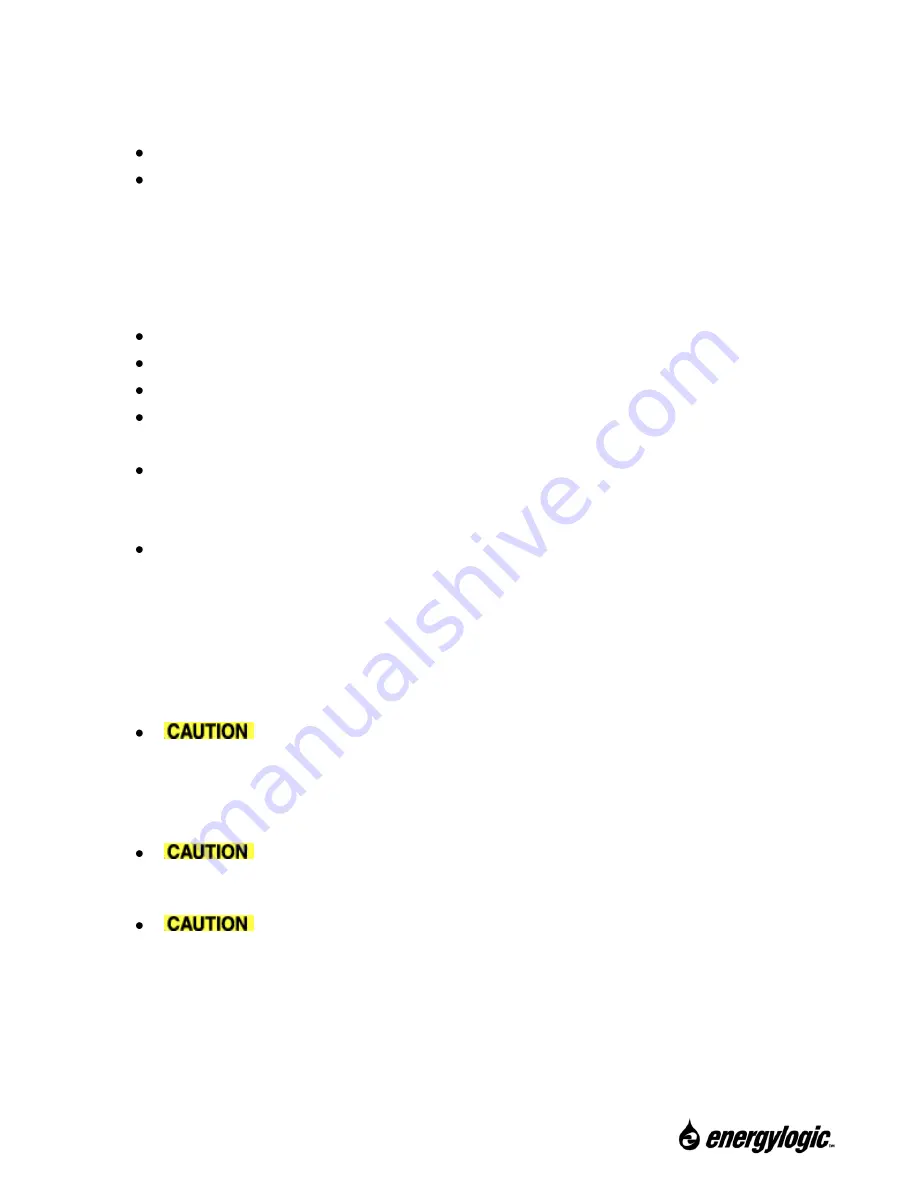
28
Call 1-
800-347-9575
for Technical Support
4.7.2 Pump Discharge (Outlet) Tubing Installation
– Guidelines
The following guidelines are provided:
Pump Discharge Tubing Considerations:
Use
3/8” O.D. copper tubing, with 1/32” wall thickness.
Run tubing with an upward slope towards the preheater, with no loops or high points to
trap air. Realizing that the preheater is low to the ground on most boiler installations and
that the line will likely need to drop down at one point, install a high-point-bleed kit
(accessory available from EnergyLogic) wherever the discharge line routing steps down
to provide a means to bleed trapped air in the line during priming. Run tubing as straight
as possible.
Use 45° flare connections for copper tube. Never use compression fittings.
Maximum vertical rise of discharge piping is 30 feet.
Maximum total length of discharge piping is 150 feet.
Discharge line from the metering pump must be run indoors, with a minimum ambient
temperature of 50°F (10°C).
Installation of a shut-off valve after the fuel pump will make routine maintenance easier.
It will prevent loss of oil in the discharge line if the pump discharge connection is to be
loosened for priming or other maintenance.
If the tank is not visible from the burner, the use of a remote system gauge kit
(accessory available from EnergyLogic) is recommended in order to have convenient
pressure readings available at the burner.
4.8 Hydronics Connection and Boiler Mixing Valve Installation
4.8.1 Hydronics Installation
– Key Points
The EL Boiler is a low pressure (30 psi), hot water boiler. When an EL boiler
is incorporated into an existing hydronics system with other types of boilers, it is
important to know what the system pressure will be. Injection pumps and pressure
reducing valves can allow incorporation of a low pressure boiler into a higher loop
pressure application.
The return water temperature to the boiler must be above 140°F. If water
temperatures at the return are consistently lower than 140°F, the boiler will sweat on the
fire-side of the tube causing coking, and corrosion; thus voiding the warranty.
Boiler water must be oxygen-free (use an air/water separator and oxygen
barrier piping) if the water is through the main vessel (closed-loop system). For
applications where water is being pulled directly from main water supplies, open tanks,
or pools, the water should be routed through the domestic coil. An oxygen-rich water
supply through the carbon steel portion of the boiler heat exchanger will result in
corrosion and accelerated vessel degradation, voiding the warranty.