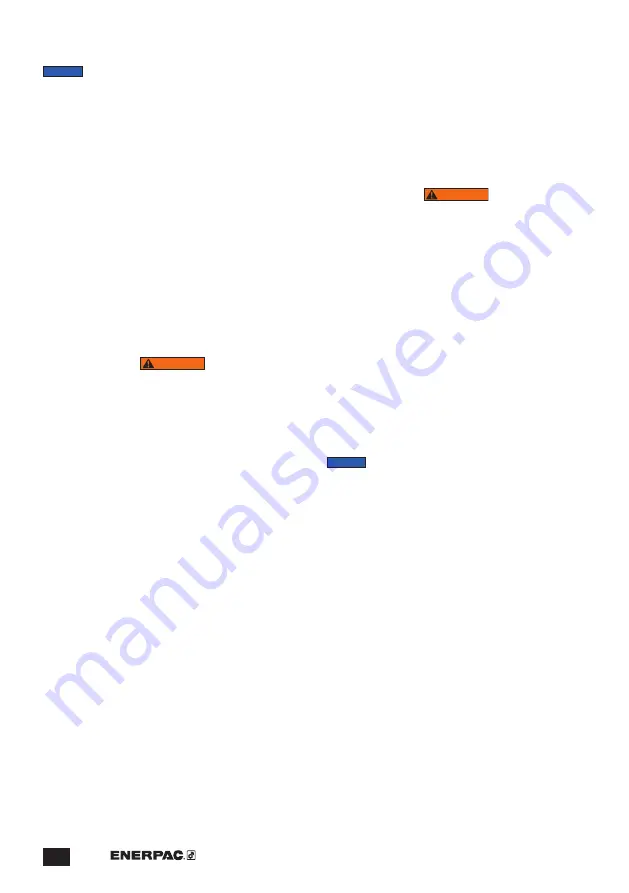
18
NOTICE
During priming, the oil may become entrained
with air and may develop a foamy appearance. This is
normal.
19. Continue pressing and releasing the trigger in
short bursts as the piston retracts all the way back.
During this process, continue adding oil to keep the
reservoir full.
20. Move the directional control valve lever to the
position 1 (advance).
21. Press and release the trigger in short bursts as
the piston extends all the way forward. During this
process, continue adding oil to keep the reservoir
full.
22. Loosen the vent screw.
23. Slowly install the diaphragm in the diaphragm
opening. This should result in some oil leakage
from the vent screw, as well as from around the
diaphragm.
24. Tighten the vent screw.
25. Install and securely tighten the diaphragm cover.
NOTICE:
WARNING
To avoid serious personal injury, stay clear of cutting
head and blades during the following procedures.
26. Start the cutter and cycle the piston through several
advance and return strokes. Ensure that the piston
is fully advanced when done.
27. Disconnect the cutter from the AC power supply.
28. Be sure cutter is positioned so that the oil reservoir
cap is facing upwards. Do not operate cutter for
several hours (preferably overnight) to allow any
remaining air to separate from the oil.
29. Loosen and remove the oil reservoir cap. Recheck
the oil level in the oil drain/fill hole. If oil level has
dropped, loosen vent screw and add additional
Enerpac HF oil until the oil level is up to the top of
the hole.
30. Install and securely tighten the oil reservoir cap.
31. Tighten the vent screw (if loosened).
32. Using a clean rag, wipe the cutter housing, grip and
motor so that surfaces are free of oil residue.
33. Connect the cutter to the AC power supply. Cycle
the piston several times to test for proper operation
before placing the cutter back into service.
10.6 Cutter Blade Replacement
NOTICE:
WARNING
• Always disconnect cutter from AC power supply
before beginning blade replacement procedures.
Failure to observe this precaution could result in
accidental start-up during blade replacement.
Serious personal injury could result.
• Use extreme caution when removing and installing
blades. Blades may be sharp even when worn. To
avoid hand injury, wear appropriate personal
protective equipment (PPE) and avoid contact with
blade cutting edges.
10.6.1 Blade Wear
The use of worn blades decreases the effectiveness of
the cutter and can also side load the cylinder, resulting
in possible damage to the tool. Motor overheating can
also occur.
Replace blades immediately if they are worn and/or
damaged or if there has been a noticeable decrease in
cutting performance.
NOTICE
Blades are not sharpenable and must be
replaced when worn. To help ensure optimum cutting
performance, replace both the fixed blade and the
moving blade at the same time.