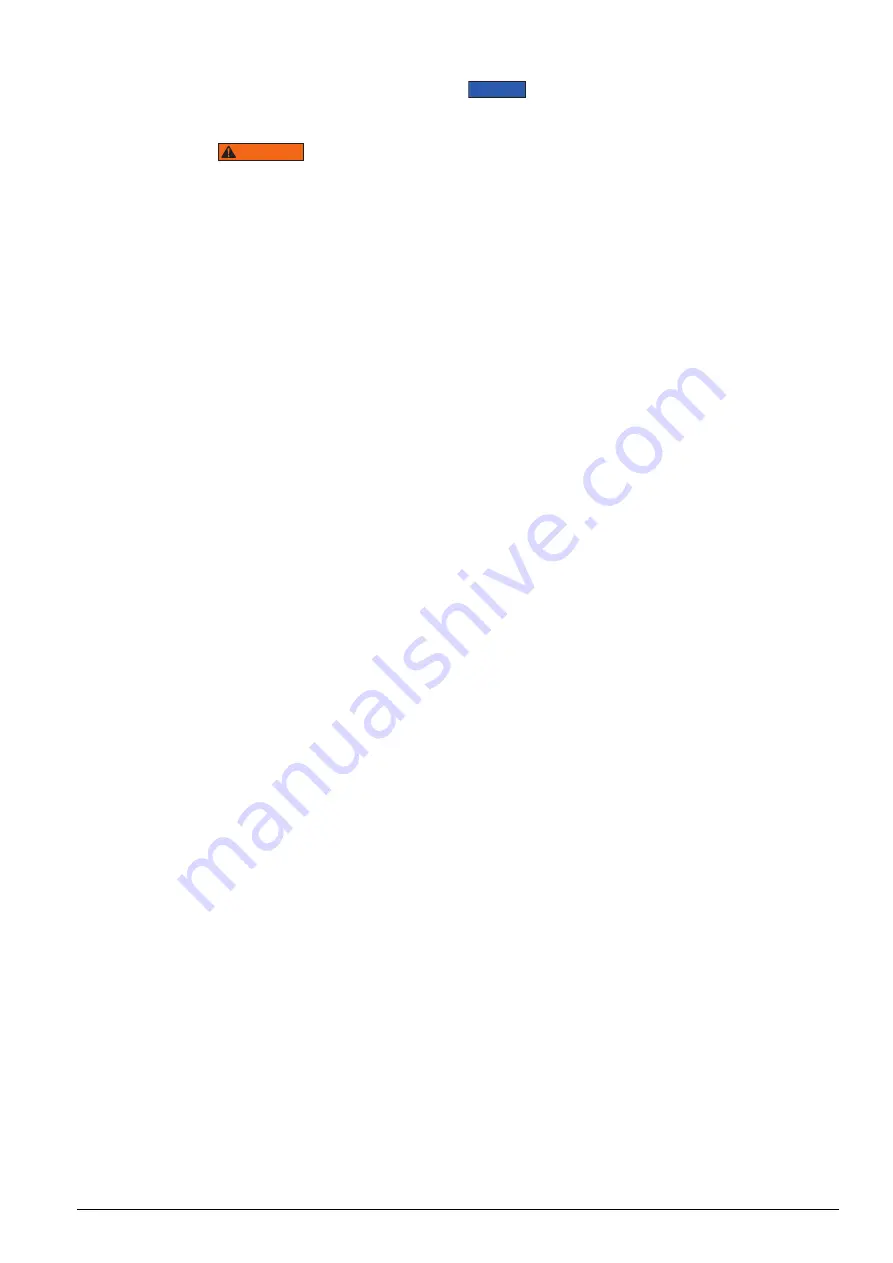
L4478_a
5
1.2 ATEX Safety Precautions
Reducing the Risk of Explosion
Failure to observe and comply with the following
precautions and instructions could result in
explosion and/or fire. Death and/or serious personal
injury could occur.
• To help reduce the risk of explosion, be certain
to use the HMT-Series torque wrench only in the
specific explosive atmospheres for which it has
been tested and certified. Refer to the beginning
of this section for ATEX classification information.
• The HMT-Series torque wrench is generally not
considered as a potential source of ignition.
However, proper operation and maintenance of
the tool is essential in order to help ensure that no
sparks are generated that could cause an ignition
of an explosive gas or dust mixture (which might be
present in the environment). Complete operation
and maintenance instructions must be provided to
all personnel in advance of operating or servicing
the wrench.
• Hot surfaces can be a major source of ignition.
To help prevent the possibility of ignition resulting
from excessive surface temperatures, do not use
the wrench in an environment with an ambient
temperature of above 104°F [40°C].
• Enerpac has designed and constructed the HMT-
Series torque wrench to minimize the possibility
of an incendiary spark that may be caused by the
impact of aluminium components with corroded
steel. However, to reduce the chance of an
incendiary spark, use of the wrench with corroded
steel structures or components should be avoided
whenever possible. Be especially careful to avoid
accidental impacts with the wrench and corroded
steel.
WARNING
To help prevent a mechanical spark hazard,
no components containing a magnesium content
greater than 7.5 percent have been used in the HMT-
Series torque wrench (in accordance with standard EN
13463-1).
• Take extreme care to prevent the HMT-Series
torque wrench from being dropped on the floor or
onto any other metallic surface that might cause
mechanical sparks at impact. Also, take every
precaution to prevent other tools (or other metallic
objects) from dropping onto the HMT-Series torque
wrench.
Electrostatic Discharge
• Electrostatic discharge is a potential source of
ignition and can result in electrostatic build-up
on isolated conductive parts. Isolated conductive
parts create capacitive poles which can become
charged. Electrostatic discharge risk is minimized
by the hydraulic hoses, which have multiple layers
of steel braiding, resulting in electrical continuity
between the torque wrench and the grounded
hydraulic pump.
• Non-conductive polyester labels could be a site
for electrostatic build-up. However, electrostatic
build-up is prevented by the close proximity of the
grounded torque wrench body.
NOTICE
Summary of Contents for HMT Series
Page 2: ......
Page 44: ...2020 Enerpac Tool Group All Rights Reserved www enerpac com...