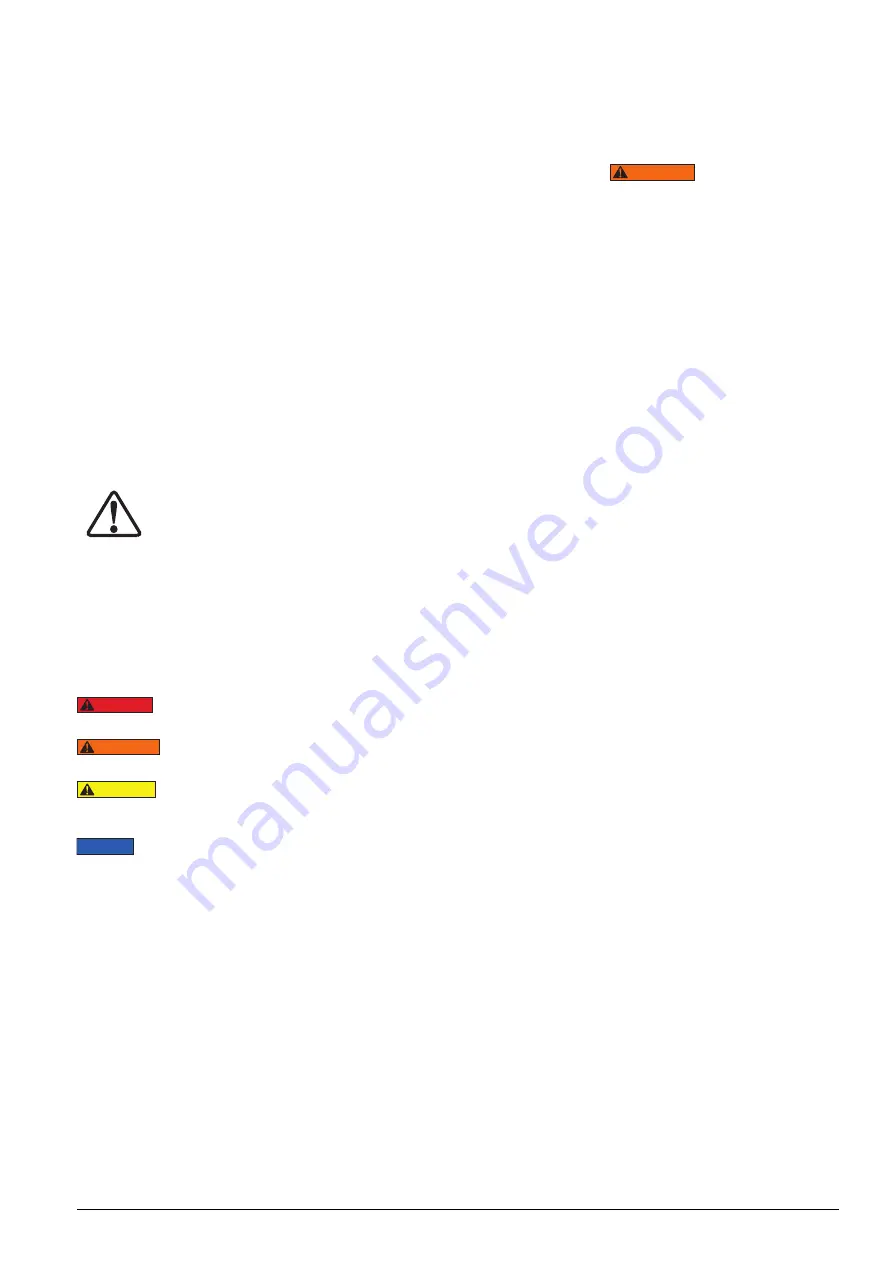
L4627_b
3
1. Safety
1.1 Safety Precautions
Failure to observe and comply with the following
precautions could result in death or serious personal
injury. Property damage could also occur.
• Read and completely understand the safety
precautions and instructions in this manual before
operating the SHS or preparing it for use. Always
follow all safety precautions and instructions,
including those that are contained within the
procedures of this manual.
• Always wear protective head-wear, ear protectors,
footwear and gloves (at a minimum rigger type
gloves) suitable for safe operation of the tool.
The protective clothing must not interfere with
safe operation of the tool or restrict the ability to
communicate with co-workers.
• Be sure your workplace is safe. Follow the
instructions in your workplace’s standard
operating procedures and be sure to observe all
communicated safety precautions.
• Ensure all hydraulic components are rated to a safe
working pressure of 700 bar (10150 psi).
• Do not remove or disable the pump relief valve.
• The system operating pressure must not exceed
the pressure rating of the lowest rated component
in the system.
• Never set a relief valve to a higher pressure than
the maximum rated pressure of the SHS. If ratings
are different, relief valve setting should not exceed
the setting of the lowest rated component (pump
or cylinder).
• Do not overload equipment. Never attempt to move
a load with higher weight than the maximum load
value of the SHS. Overloading causes equipment
failure and possible personal injury.
• Always perform a visual inspection of the SHS
before placing it into operation. If any problems are
found, do not use the cylinder. Have the cylinder
repaired and tested before it is returned to service.
• Never use a cylinder that is leaking oil. Do not use
the SHS if is damaged, altered or in need of repair.
• Always lift the cylinder using a crane or other
suitable lifting device of sufficient rated capacity.
Use only the 4 hoisting eyes on the SHS frame to
attach the cylinder to the lifting device.
• Allow only trained and experienced personnel
to supervise and perform lifting and lowering
procedures.
• Be sure the operator has completed safety induction
training, specific to the work surroundings. The
operator should be thoroughly familiar with the
controls and the proper use of the tool.
• Be certain that no persons are working on or near
the SHS before moving of the load begins. Alert all
personnel in advance that the procedure is about
to occur.
WARNING
Read all instructions carefully. Follow all recommended
safety precautions to avoid personal injury as well
as damage to the product and / or damage to other
property. Enerpac cannot be responsible for any
damage or injury from unsafe use, lack of maintenance,
or incorrect operation. Do not remove warning labels,
tags, or decals. In the event that any questions or
concerns arise, contact Enerpac or a local Enerpac
distributor for clarification.
Save these instructions for future use.
If you have never been trained on high-pressure
hydraulic safety, consult your distributor or service
center for information about Enerpac Hydraulic Safety
Courses.
This manual follows a system of safety alert symbols,
signals, words, and safety messages to warn the user of
specific hazards. Failure to comply with these warnings
could result in death or serious personal injury, as well
as damage to the equipment or other property.
The Safety Alert Symbol appears throughout
this manual. It is used to alert you to potential
physical injury hazards. Pay close attention
to Safety Alert Symbols and obey all safety
messages
that follow this symbol to avoid the possibility
of death or serious injury.
Safety Alert Symbols are used in conjunction with certain
Signal Words that call attention to safety messages or
property damage messages and designate a degree or
level of hazard seriousness. The Signal Words used in
this manual are DANGER, WARNING, CAUTION, and
NOTICE.
Indicates a hazardous situation that, if not
avoided, will result in death or serious personal injury.
Indicates a hazardous situation that, if not
avoided, could result in death or serious personal injury.
Indicates a hazardous situation that, if not
avoided, could result in minor or moderate personal
injury.
Indicates information considered
important, but not hazard related (e.g. messages related
to property damage). Please note that the Safety Alert
Symbol will not be used with the signal word.
DANGER
WARNING
CAUTION
NOTICE