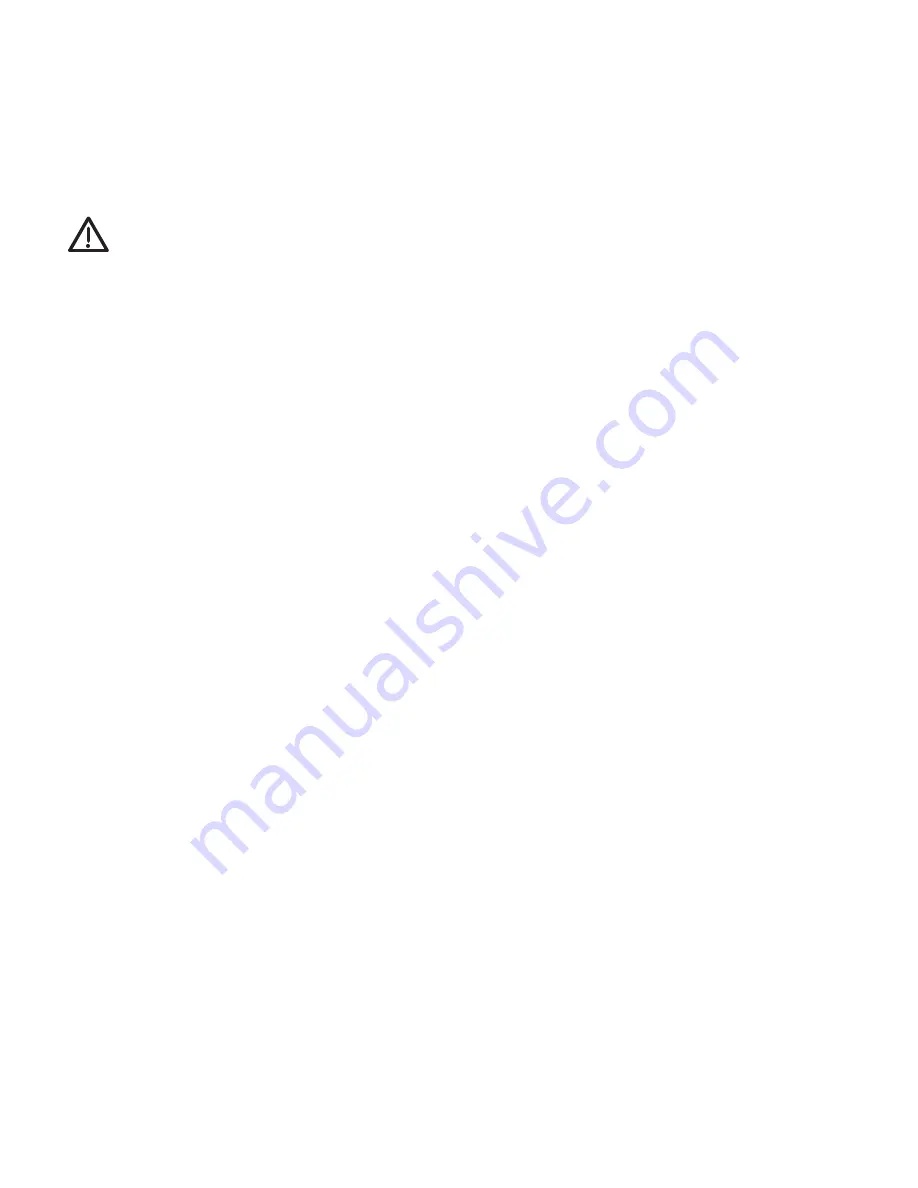
8
TROUBLESHOOTING AND REPAIR OF VM33, VM33M, VM33L, VM43, VM43M, VM43L MANUAL VALVE
In diagnosing malfunctioning valves, certain symptoms may be
common not only to valves, but often to hydraulic equipment in
general. Before repairing the valve, mount a different VM valve
onto the pump and verify that the problem is not with the pump.
TROUBLESHOOTING:
CAUTION:
Standard safety procedures are to be
followed during assembly to minimize any possibility
of injury.
1. Inability to obtain any pressure may be the result of
damaged connector seals on the pump, or failed relief valve
components (items 6, 7, fi gure 7) a damaged ball and seat
in the body (items 1, 2, fi gure 8), or damaged or worn shear
seals and disc (items 16, 18, 84, fi gure 1D). These problems
are usually a symptom of contaminated hydraulic oil. The
system should be drained and refi lled with fresh ENERPAC
hydraulic oil.
2.
Pressure leaks that are consistent and increase
proportionately with increasing pressure ranges are usually
the result of leaking gaskets or threaded surfaces such as
NTPF fi ttings or plugs.
3. Ball seat leakage is often erratic and intermittent and is
caused by contaminants trapped on the sealing edge. Over
time, as wear occurs, these seats will need to be replaced.
4. Leakage observed on the external surfaces around the shaft
(item 13, fi gure 1D) is an indication that the o-ring (item 15)
and backup ring (item 14) need to be replaced.
5. Leakage observed on the external surfaces around the relief
valve body (item 1, fi gure 7) is an indication that the o-ring
(item 8) needs to be replaced.
DISASSEMBLY:
1. Remove the 4 socket head cap screws (item 76, fi gure 1C)
and remove the valve from the pump.
2. Remove the return tube (item 75) and gasket (item 70).
3. Remove the screw (item 1, fi gure 1D) and washer (item 2)
from the shaft (item 13).
4. All models except VM33M & 43M: Remove the handle (item
3), disk (item 4) ball (item 5) and spring (item 6).
5. Models VM33M & VM43M only: Remove handle cap (item 66)
lever (item 67) and knob (item 68) as an assembly. Remove
ball (item 5) and spring (item 6).
6. Remove the 4 socket head cap screws (item 7) and remove
the upper valve assy. (item 44, fi gures 1A & 1B) from the
manifold (item 27) or locking valve block (item 45 or 46).
7. Remove the 2 socket head cap screws (item 24, fi gure 1D)
and separate the body (item 23) from the valve cap (item 9).
8. Remove the shaft assembly and inspect the o-ring (item 15)
and backup ring (item 14) for damage. Replace if needed.
9. Remove the o-ring (item 10) and inspect for damage such as
nicks or cuts. Replace if needed.
10. Remove the bearing (item 12) and bearing plate (item 11)
and inspect for damage. Replace if needed.
11. Remove the shear seal assemblies (items 18-20 or 84-86)
from the bores in the body.
12. Remove o-rings (item 20 or 86) and backup washers (item
19 or 85) and inspect for damage. Replace if needed.
13. Remove springs (item 22) and inspect for damage such as
breakage or permanent set. Replace if needed.
14. Disassembly of the manifold is as follows:
15. Loosen lock nut (item 9, fi gure 7) and unscrew the set screw.
(item 2).
16. Using a 7/8" socket, loosen and remove the relief valve
assembly (item 58, fi gures 4, 5, 6 & 6A) from the body.
17. Remove the seat (item 57) from the body.
18. Inspect the seat for damage such as nicks or dents on the
sharp edge of the internal diameter. Replace if necessary.
19. Inspect the o-ring (item 8, fi gure 7) for damage and replace if
necessary.
20. Inspect the ball (item 7) and guide (item 6). Replace if
necessary.
21. Remove the pipe plugs (item 53, 54, 55, fi gures 4, 5, 6 & 6A)
and clean the body. Inspect body for damages.
REASSEMBLY:
Procedure for Manifold Assembly
1. Apply Tefl on tape to threads. Install new pipe plug (item 53,
fi gures 4, 5, 6 & 6A) and torque to 10-12 ft-lbs [14-16 Nm].
Install pipe plug (item 54, 55) and torque to 32-39 ft-lbs [43-
52 Nm].
2. Install copper gasket (item 56) onto seat (item 57), with round
edges facing away from the seat.
3. Place seat onto the bottom counter bore in the valve body,
with the gasket side down. Note: make sure that the seat is
fi rmly seated and not crooked.
4. Grease o-ring on relief valve assembly and insert into cavity
in the valve body.
5. Torque relief valve assembly (Item 58) to 32-39 Ft-lbs [43-53
Nm].
Procedure for Upper Manual Valve Assembly
1. Position plate (item 11, fi gure 1D) and bearing (item 12) into
cap.
2. Place o-ring (item 10) into cap groove.
3. Place o-ring (item 15) and backup ring (item 14) onto shaft
(item 13). The o-ring is placed closest to the threaded end of
the shaft.
4. Place roll pin (item 17) into thru hole in disc (item 16). Insert
shaft (item 13) into disc from the solid side of the disc.
Align the thru hole in the shaft with the thru hole in the disc
and press or hammer roll pin until fl ush with disc outside
diameter.
5. Lubricate the o-ring and backup ring on the shaft with
grease. Insert the shaft and disc assembly into the valve cap
(item 9).
6. Place springs (item 22) in each of 3 holes except for hole on
tank side of the body (item 23).
7. All models except VM33M & VM43M: Assemble each shear
seal (item 18) with 2 backup washers (item 19) and 1 o-
ring (item 20). The o-ring is placed between the backup
washers.
8. Models VM33M & VM43M Only: Assemble each shear seal
(item 84) with 1 backup washer (item 85) and 1 o-ring (item
86). The o-ring is placed under the backup washer.
Summary of Contents for VM33
Page 55: ...55 ...