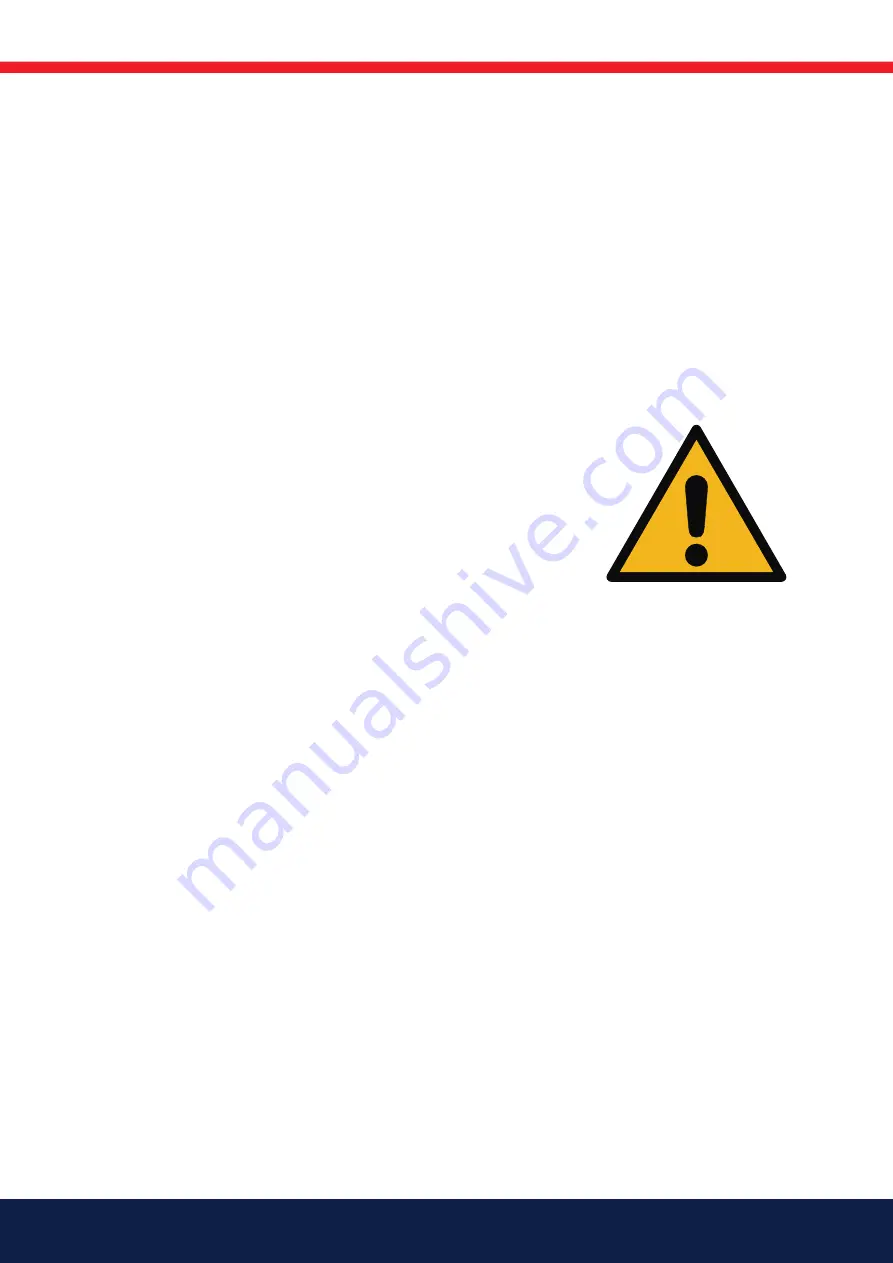
4
Bentone
1. General Information
This Installation and Maintenance manual:
• is to be regarded as part of the burner and must always be kept near
the installation site
• is intended for use by authorised personnel
• must be read prior to installation
• must be observed by all who work with the burner and associated
system components
• work with the burner may only be carried out by certified installers/
personnel
• Enertech AB is not liable for any typographical errors and reserves the
right to make design changes without prior notice.
• The burner may only be used for its intended purpose in accordance
with the product’s technical data.
• The burner may only be installed and operated by authorised
personnel.
• The product is packaged to prevent damage from occurring during
handling. Handle the product with care. Lifting equipment must be
used to lift larger packages.
• The products must be transported/stored on a level surface in a dry
environment, max. 80% relative humidity, no condensation.
Temperature -20 to +60 °C.
• Check that the burner is compatible with the boiler’s output range.
• The label information on the rating plate refers to the burner’s minimum
and maximum power.
• The power data on the type sign refers to the burner’s min. and max.
power.
• All components must be installed without being bent, twisted or
subjected to mechanical or thermal forces which can affect the
components.
• The burner must be installed so that it complies with local regulations
for fire safety, electrical safety, and fuel distribution.
• Make sure when installing the equipment that there is enough space to
service the burner.
• Permitted ambient temperature during operation -0 to +60 °C. Max
80% relative humidity, no condensation.
• The installer must ensure that the room has adequate air supply.
• The room must comply with local regulations pertaining to its intended
use.
• The installation site must be free of chemicals.
• Burner pipes, fan wheels and air dampers may contain sharp edges.
• The surface temperature of the burner’s components can exceed 60
°C.
• Caution: The burner has moving parts, and there is risk of crushing
injuries.
165 105 01
Summary of Contents for Bentone ST50 ST 120 KA
Page 2: ...2 Bentone...
Page 16: ...16 Bentone...
Page 32: ...171 905 28...
Page 35: ......
Page 36: ...Enertech AB P O Box 309 SE 341 26 Ljungby www bentone se www bentone com...