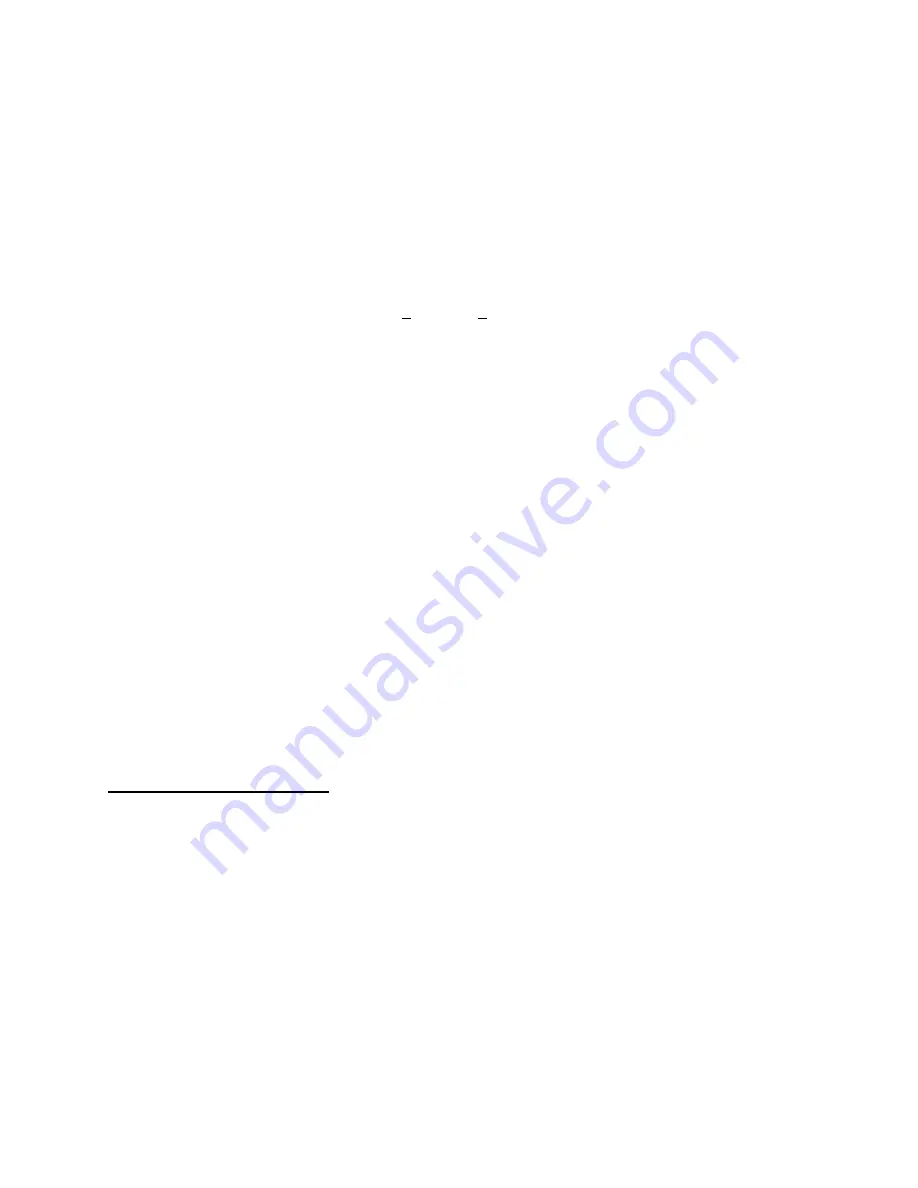
April 23, 1999
Page 13
(2) Remove pressure tap plug in valve or pressure tap plug in manifold and install pressure
tap fitting.
(3) Connect pressure gauge to pressure tap fitting. Preferred gauge is a U tube manometer.
(4) Turn valve to "on" and let burners come to full fire (approximately 15 seconds from initial
opening of valve).
(5) Remove regulator cover screw and adjust manifold pressure by turning adjusting screw
clockwise to increase pressure or counterclockwise to decrease pressure. (CAUTION:
Adjustment is sensitive. Turn screw very slowly.)
(6) Set manifold pressure to the rating plate value.
i.e.
4.0"WG(1kPa) for 0 - 2000 ft. (610m) rating
3.5"WG(0.89kPa) for 0 - 4500 ft. (1372m) rating
Allowable tol .05"WG(+ 12.5 Pa)
(7) Check the gas input to the unit with the gas meter.
(8) When the pressure and input are set, turn knob on gas valve to "pilot" or "off". Remove
pressure tap fittings, install pressure tap plugs and install regulator cover screw.
(9) Turn knob on control valve back to on position.
3. AIR SHUTTER ADJUSTMENT: - See instruction label in burner compartment.
4. TEMPERATURE RISE: Adjust the fan pulley to get the specified temperature rise through
the unit (70
o
F[21
E
C] to 100
o
F[38
E
C] allowable). Thermometers may be used at the return
and supply air outlets to determine temperature rise. Avoid having thermometers pick up
radiant heat and giving false readings.
5. THERMOSTAT: Complete thermostat instructions are provided in the thermostat box.
These should be adhered to, with the following exception: Thermostat heat anticipator
should be set slightly higher (+0.16) than the control circuit current draw. Set heat anticipator
to 1.0 on units with X-TRAC or Maxitrol controls.
6. VENT SAFETY SWITCH: This unit is equipped with a vent safety limit switch. The sensing
element of this switch is located in the relief opening of the draft hood. The switch opens to
shut down the main burners in the event of a blockage in the venting system. If a shut down
occurs, refer to the information sticker adjacent to the switch.
OPERATING INSTRUCTIONS
1. Lighting, shut off and shut down instructions are provided on the rating plate located in the
burner compartment.