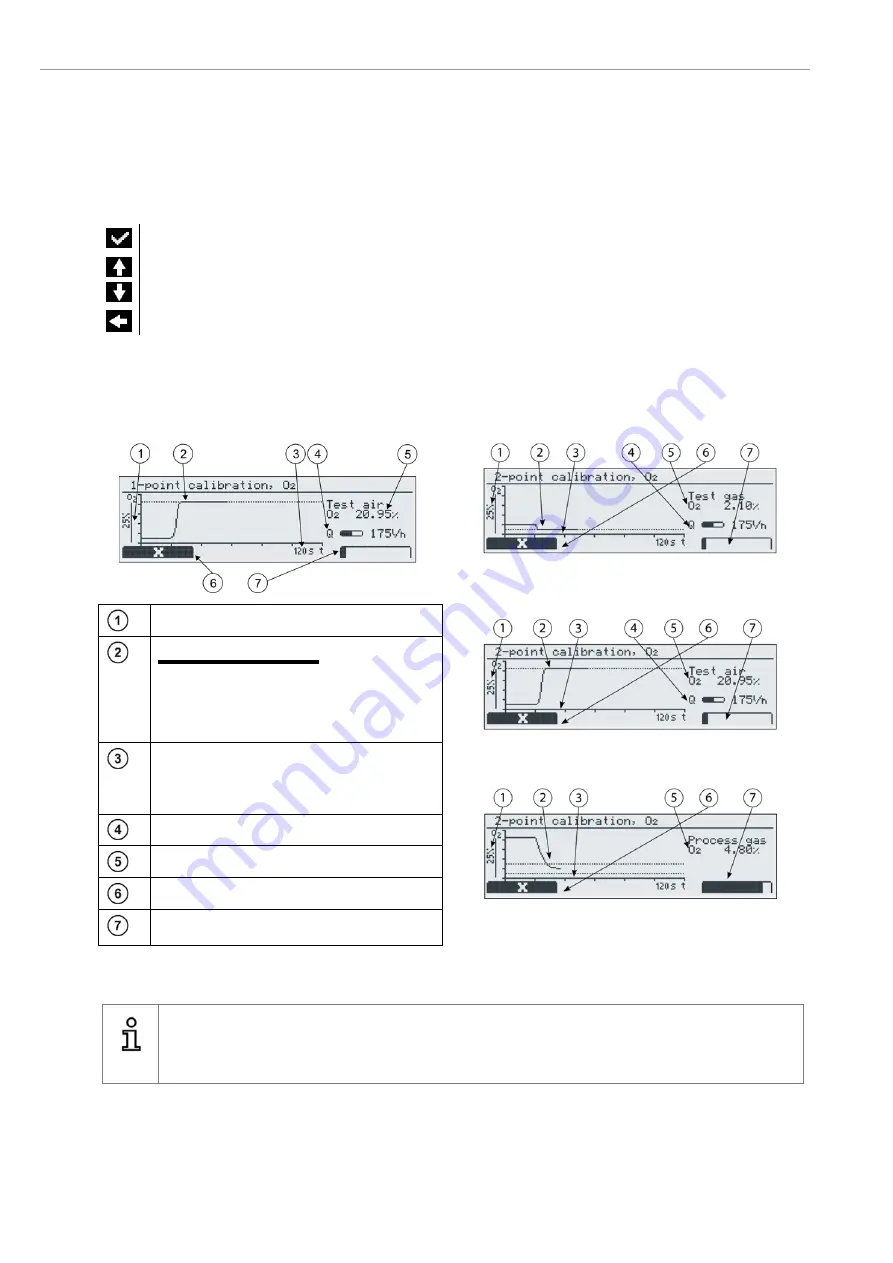
Software Overview and Explanations
Installation and Operation Manual OXITEC
®
5000
26
Doc.-ID: OXI-11022020-EN
4.2.15
Service (factory service settings)
The service functions are password protected and are only accessible by trained service personnel. These functions
are protected with a code, different to the system code.
4.3
Calibration menu
CAL MENU
1 point calibration, O
2
2 point calibration, O
2
4.3.1
Calibration menu - display overview
1-point calibration display:
2-point calibration displays:
Test Gas apply
The max. adjustable measuring range
Trend representation of measured O
2
value
and O
2
target value
………………
The target value is determined by the O
2
concentration in the test gas / test air
Time scale showing the elapsed time of the
current calibration process. The
amount in seconds (here 120 s) refers to the
end of the time scale
Test Air apply
The flow rate currently measured
Current measured value of O
2
Abort the calibration
Progress bar
Process gas apply
Figure 26 –
Different calibration displays.
Info
The oxygen concentration in test air needs not be entered as it is known (20,95 % O
2
).
During calibration, entry of the test gas concentration value takes place after test gas has been applied.