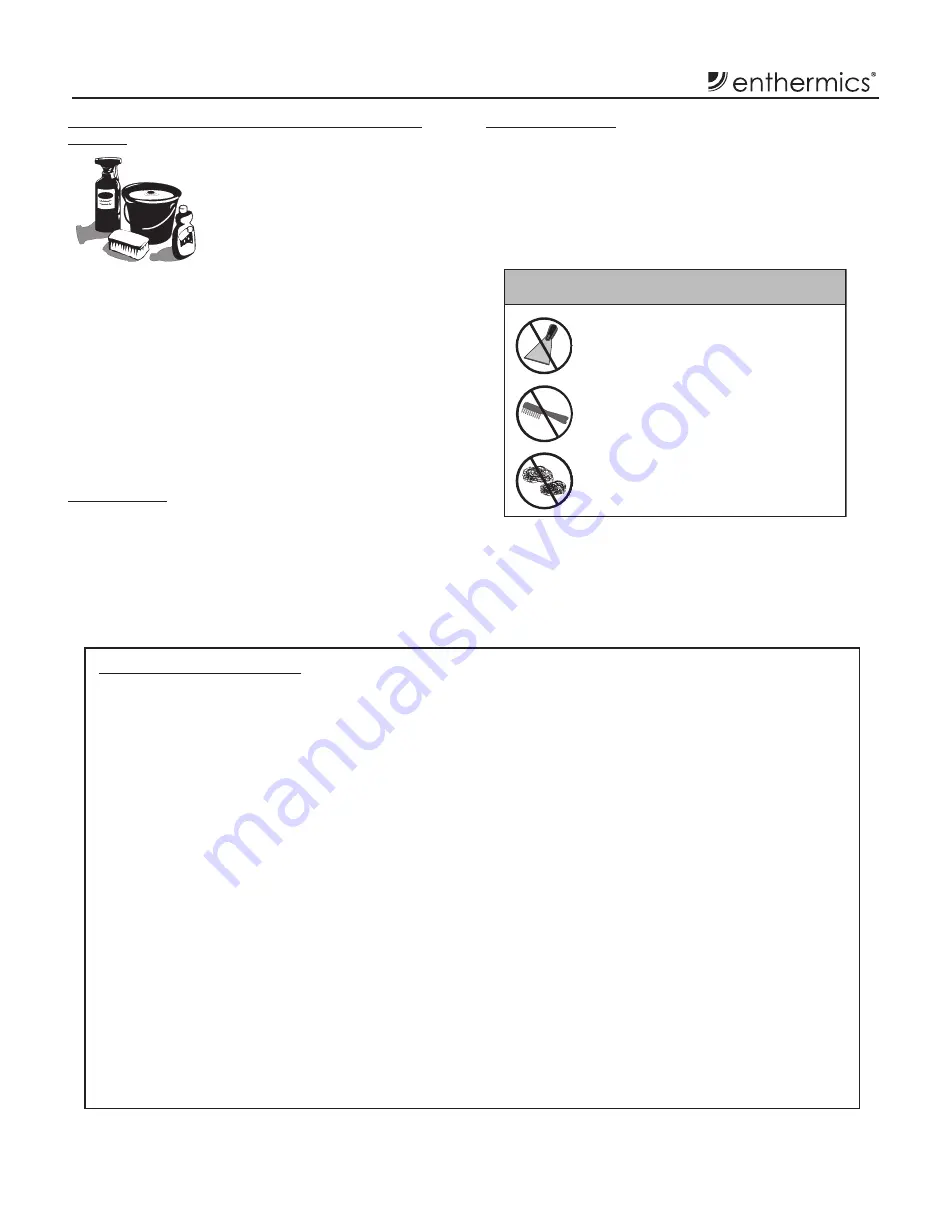
MN-28646 • Rev 4 • 03/18 • EC Series Fluid Combination Blanket/Fluid Warmer
14
Cleaning and Prevetative Maintenance
Cleaning and Preventive Maintenance
Protecting stainless steel, epoxy coated and plastic
surfaces
It is important to guard against corrosion
in the care of stainless steel surfaces.
Harsh, corrosive, or inappropriate
chemicals can completely destroy the
protective surface layer of stainless
steel, epoxy or plastic. Abrasive pads,
steel wool, or metal implements will
abrade surfaces causing damage to
this protective coating and will eventually result in areas of
corrosion. Even water, particularly hard water that contains
high to moderate concentrations of chloride, will cause
oxidation and pitting that result in rust and corrosion. In
addition, many acidic spills left to remain on metal surfaces are
contributing factors that will corrode surfaces.
Proper cleaning agents, materials, and methods are vital to
maintaining the appearance and life of this appliance. Spilled
items should be removed and the area wiped as soon as possible
but at the very least, a minimum of once per day. Always
thoroughly rinse surfaces aft er using a cleaning agent and wipe
standing water as quickly as possible aft er rinsing.
Cleaning agents
Use non-abrasive cleaning products designed for use on
stainless steel surfaces. Cleaning agents must be chloride-free
compounds and must not contain quaternary salts. Never use
hydrochloric acid (muriatic acid) on stainless steel surfaces.
Failure to observe this will void the warranty. Always use the
proper cleaning agent at the manufacturer’s recommended
strength. Contact your local cleaning supplier for product
recommendations.
Cleaning Materials
Cleaning can usually be accomplished with the proper cleaning
agent and a soft , clean cloth. When more aggressive methods are
needed, use a non-abrasive scouring pad on diffi cult areas and
make certain to scrub with the visible grain of surface metal to
avoid surface scratches. Never use wire brushes, metal scouring
pads, or scrapers to remove residue. Failure to observe this will
void the warranty.
CAUTION
To protect surfaces, completely
avoid the use of abrasive cleaning
compounds, chloride based cleaners,
or cleaners containing quaternary
salts. NEVER use hydrochloric acid
(muriatic acid) on stainless steel.
NEVER use wire brushes, metal
scouring pads or scrapers.
NO
W
IRE BRUSH
ES
NO
STE
EL PAD
S
NO
SCRAPERS
PREVENTATIVE MAINTENANCE
Daily Checklist:
❏
Ensure that the correct operation and care manual is
available to all users.
❏
Ensure that all people using this appliance have
been properly trained in the operation and safety
instructions.
❏
DO NOT overload cabinet.
• Blanket Warmer: 1" (25mm) from top interior of
unit and/or shelf
• Fluid Warmer: See electrical/capacity page
Weekly Checklist:
❏
Inspect condition of plug and cord. Replace if
damaged.
❏
Clean dust from under inserts, outer vents surrounding
the unit and around top of bonnet (if applicable).
❏
Check insert assembly (depends on unit):
• Blanket Warmer: Check the blanket support
assembly and shelf. Is the assembly in place?
Are any pieces missing?
• Fluid Warmer: Check basket and side rail condition.
Do baskets move smoothly and freely?
❏
Check that all control and interior LEDs light up.
Monthly Checklist:
❏
Check door gasket integrity. Are there any tears? Is the
gasket worn or loose? Ensure seal is tight to unit body.
Replace gasket if integrity is compromised.
❏
Check air temperature sensor mount on the interior of
chamber. Is the guard in place and is it fully secured to
the unit?
❏
Check condition of casters or feet. Ensure components
are secure and tightly threaded.
❏
Check control panel overlay condition. Are there
any tears or excessive wear on the graphic? Does the
control work properly when buttons are pushed?
❏
Is the set temperature comparable to the actual
temperature displayed? Check cavity air temperature
with a quality thermocouple placed 1" (25mm) from
the cavity sensor not allowing it to touch any surface.
Monitor for approximately one hour in an empty
cavity.
Contact service for immediate repair
if any of the above problems exist.