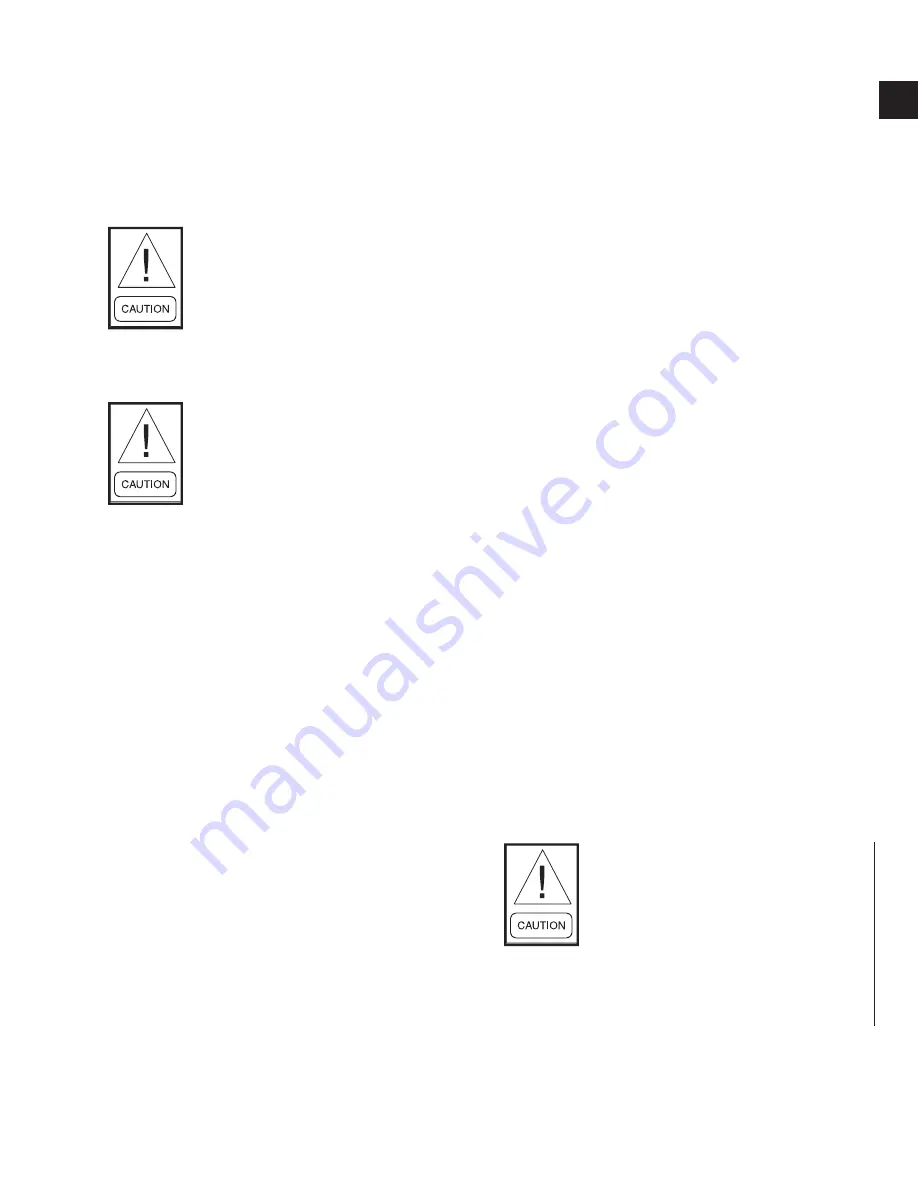
ENVIRO-TEC
17
SECTION 1 - RECEIPT & INSTALLATION
FORM ET115.24-NOM4 (819)
1
After all connections are completed, and prior to insu-
lating and furring-in of any riser or piping connections,
the system should be tested for leaks. Since some com-
ponents are not designed to hold pressure with a gas,
hydronic systems should be tested with clear water.
Care should be taken to completely drain the system,
or otherwise protect it from freezing in cold weather.
Standard unit operating pressure is 300
psig maximum. Field test pressure must
not exceed 400 psig maximum. Some op-
tional or special unit piping components
may have lower pressure ratings than the
standard unit. All valve and piping com-
ponent pressure ratings must be verified
before applying test pressure to the unit.
All water coils and unit piping must be
protected from freezing after initial filling
with water. Unit coils and piping may still
hold enough water to cause damage when
exposed to freezing temperatures, even
after the system is drained.
In the event that leaking or defective components are
discovered, the Sales Representative must be notified
BEFORE any repairs are attempted. All leaks should
be repaired before proceeding with installation.
After all risers and piping are installed and pressure
tested, all riser joints must have the insulation joint
sealed and all other piping must be insulated in compli-
ance with the project specifications. All chilled water
risers, piping, and valves must be insulated or located
over a drain pan, to prevent damage from condensa-
tion. This includes factory and field piping inside the
unit cabinet.
The drain should always be connected and piped to an
acceptable disposal point. For proper moisture carry-
off, the drain piping should be sloped away from the
unit at least 1/8” per foot. A drain trap is integral to the
unit and is necessary for odor containment. The drain
riser and piping must be installed to avoid pinching or
kinking the unit drain tube.
Any required piping or riser penetration fire blocking
is the responsibility of the installer. All penetrations for
piping and risers should be sealed with materials and
techniques suitable for all governing codes and ordi-
nances.
DUCTWORK CONNECTIONS
All ductwork and/or supply and return grills should
be installed in accordance with the project plans and
specifications. If not included on the unit or furnished
from the factory, supply and return grilles should be
provided as recommend in the product catalog.
All units must be installed in non-hazardous areas.
Zero clearance to combustible materials is allowed.
Units provided with outside air for ventilation should
have some form of low temperature protection to pre-
vent coil freeze-up. This protection may be any of sev-
eral methods such as a low temperature thermostat to
close the outside air damper or a preheat coil to temper
the outside air before it reaches the unit. It is recom-
mended that outside air is pretreated to regulate its
temperature and humidity ratio
It should be noted that none of these methods would
adequately protect a coil in the event of power failure.
The safest method of freeze protection is to use glycol
in the proper percent solution for the coldest expected
air temperature.
Flexible duct connections should be used on all air han-
dling equipment. All ductwork and insulation should
be installed to allow proper access to all components
for service and repair such as filters motor/blower as-
semblies, etc.
Dual Air Discharge Units
All dual discharge units are provided with a sight and
sound baffle in the discharge plenum area (except top
discharge units). It is recommended that a discharge
grille with a damper be provided in one of the dis-
charge locations to aid in air balancing. Dual discharge
units with top discharge must be provided with a field
supplied damper in the top discharge duct.
Do not inhibit inlet or outlet connections.
Quickly turning off the inlet or rapid
reduction in ductwork can cause system
effects that impact airflow. Reductions
in airflow can cause electric heaters to
overheat, condensation to form, or other
unintended consequences, which can re-
sult in injury, property damage, equipment
damage, as well as void factory warranty.
Summary of Contents for VHA
Page 10: ...ENVIRO TEC 10 FORM ET115 24 NOM4 819 THIS PAGE INTENTIONALLY LEFT BLANK ...
Page 41: ...ENVIRO TEC 41 SECTION 2 START UP FORM ET115 24 NOM4 819 THIS PAGE INTENTIONALLY LEFT BLANK ...
Page 54: ...ENVIRO TEC 54 FORM ET115 24 NOM4 819 SECTION 6 Dimensional Data 74 80083 ...
Page 78: ...ENVIRO TEC 78 FORM ET115 24 NOM4 819 SECTION 6 Dimensional Data NOTES ...