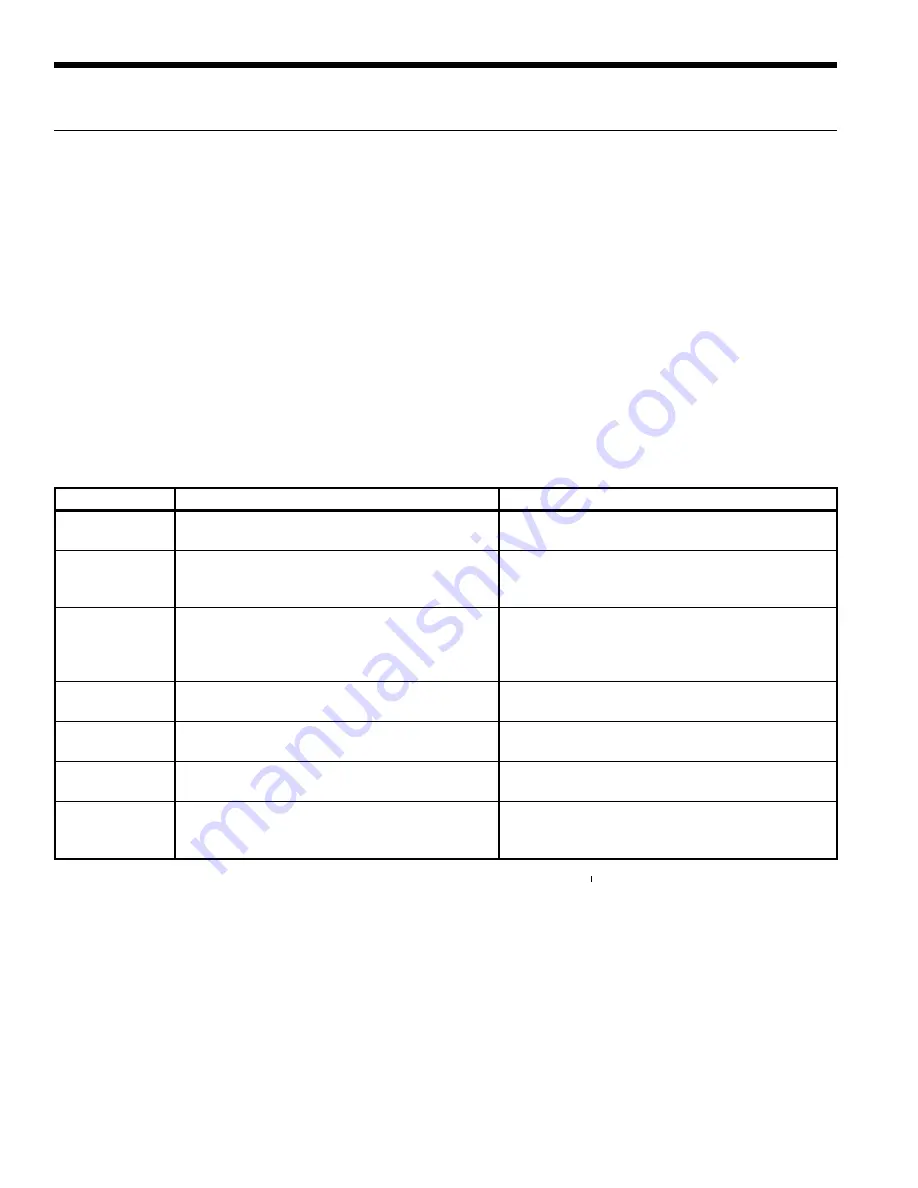
44
NSKW INSTALLATION MANUAL
Troubleshooting cont.
DISPLAY
FAILURE
DIAGNOSTIC
DC
Freeze detection thermistor is closed (shorted)
Replace the freeze detection thermistor (clip-on
thermistor)
DO
Freeze detection thermistor is open
Verify that the freeze detection thermistor is
secured properly in the board connector. If the
connection is secure, replace the thermistor.
FP
Freeze detection
The water going through the unit has reached the
freeze point setting (P=5, CL=15, OL=30). Verify
that the freeze detection setting is correct for the
application.
HC
Water set point thermistor is closed (shorted)
Replace the water set point thermistor (threaded
thermistor).
HP
High Pressure
The unit has cut out on high pressure. Discharge
pressure is >4.1 kPa.
LP
Low Pressure
The unit has cut out on low pressure. Suction
pressure is <275 Pa.
PO
Water set point thermistor is open
Verify that the water set point thermistor is
properly secured in the board connector. If the
connection is secure, replace the thermistor.
Troubleshooting Controls
Check the unit. If a lockout mode is displayed, refer to the
table below to determine the meaning of the failure. Follow
the procedure listed to correct the problem.
Check the mode:
1. If the unit is running on the internal aquastat, verify the
unit is in “Primary” mode. The SL should be set to 0 in
the setup menu.
2. If the unit is running on an external aquastat, the SL
should be set to 1.
Check the jumpers on the control board:
1. Refer to the Control Board with Jumper illustration in
the Converting to a Dedicated Cooling Unit section to
see the location of the jumper on the board. If the unit is
a heating only unit, the jumper should be across 1 and 2.
2. If the unit is a cooling only unit, the jumper should be
across 2 and 3.
3. If the unit is a reversible unit, the jumper should be
across 3 and 4.
Check the thermistor calibration:
1. Using a thermometer in the P/T port, check the
incoming water temperature.
2. Verify that the measured temperature is within 3
degrees of the temperature displayed on the unit.
3. If it is not, adjust the calibration in the setup menu.
Standard Control Diagnostic Table