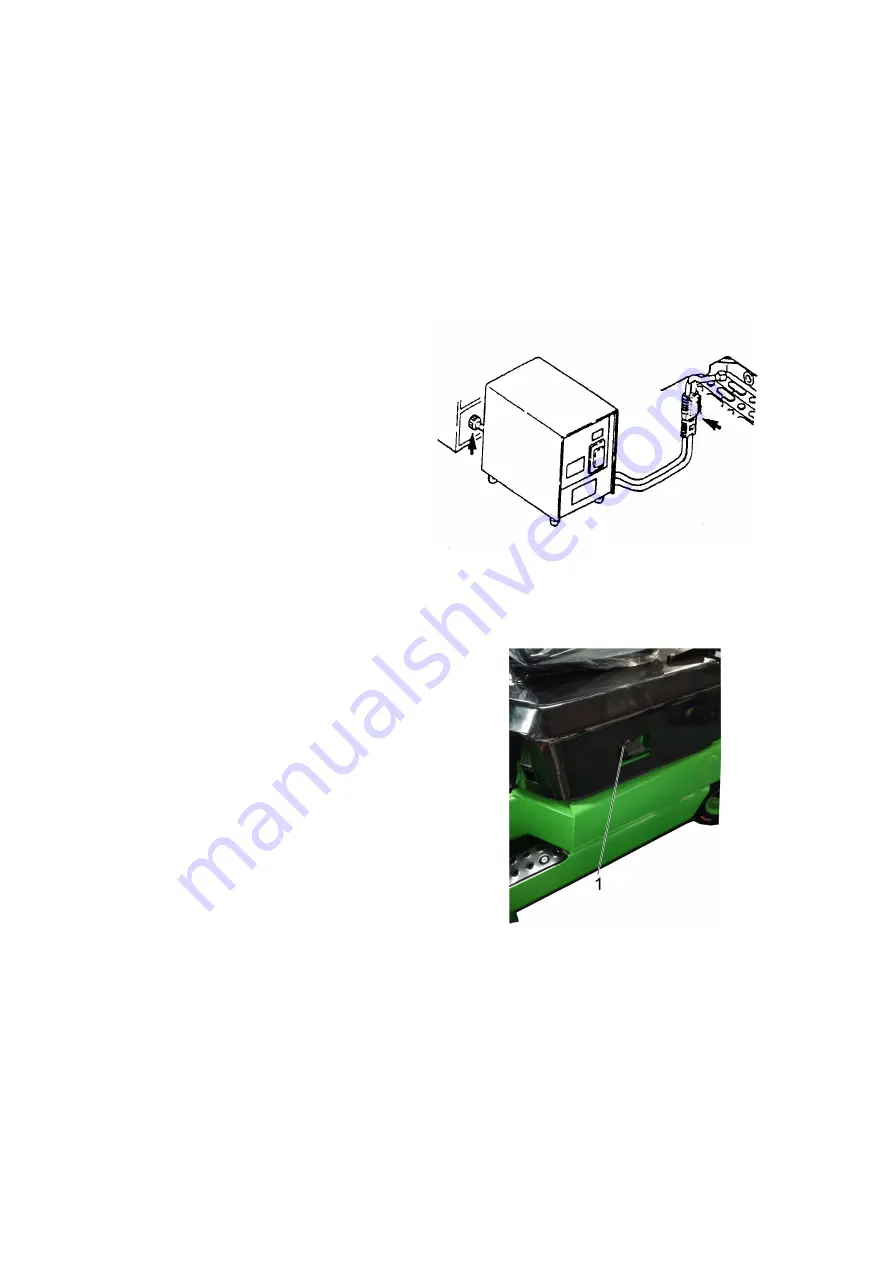
36
4.3Charging the battery
4.3.1Charging the battery
Attentions for charging
1. Please charge in the well-ventilated and appointed site.
2. Mark ‘no smoking’ on charging.
3. Inspect wire and pin.
·ahead of charging
,
please examine
wire and connector whether good
condition.
·When wire and connector are
damaged
,
please do not charge.
4. In charging
,
electrical source
switch or battery connector are not
close
,
or
,
which destroys connector
and electrical units as a rule.
4.3.1 Charging Procedure
Insert the electric switch key and turn clockwise;
Tilt the lift mast forwards slightly. The truck must
be stationary on the ground;
Pull the hand brake;
Press the emergency stop switch;
Connect charger connector to the battery
connector
(
1
)
;
Switch on the charger and charge the battery in
accordance with the battery and charging station
manufacturers’ instructions;
5. After the battery is fully charged. first close the
charger
,
then remove the connector.
Summary of Contents for IMOW ICE251
Page 1: ......
Page 25: ...18...
Page 50: ...43 5 4 Lubrication Schedule...
Page 51: ...44...
Page 84: ...77 APPENDIX...