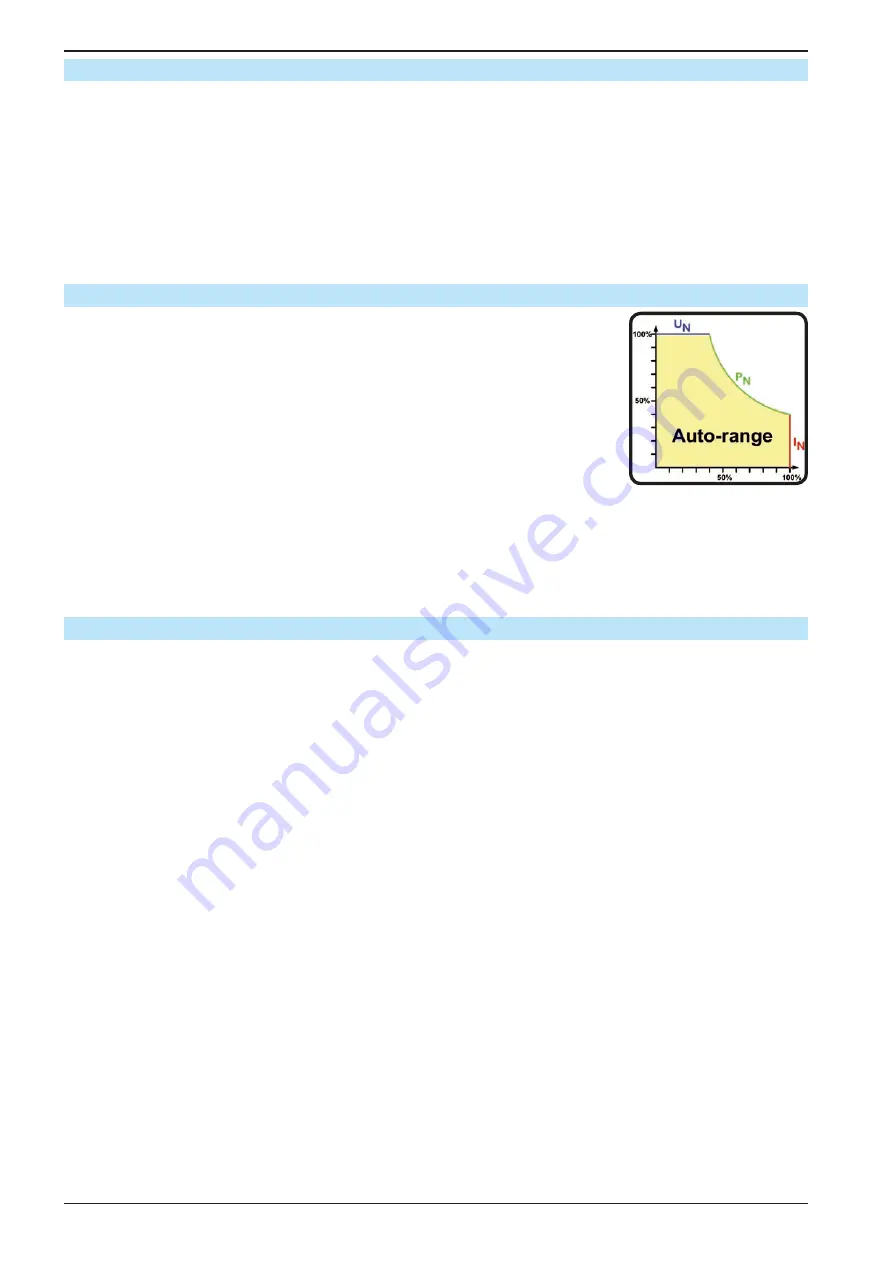
Page 36
EPS Stromversorgung GmbH
Alter Postweg 101 • 86159 Augsburg
Germany
ELR 9000 Series
Fon: +49 821 / 570451-0
Fax: +49 821 / 570451-25
3.2.3 Resistance regulation / constant resistance
Inside electronic loads, whose operating principle is based on a variable internal resistance, constant resistance
mode (CR) is almost a natural characteristic. The load attempts to set the internal resistance to the user defined
value by determining the input current depending on the input voltage according to Ohm’s law I
IN
= U
IN
/ R
SET
.
The internal resistance is naturally limited between almost zero and maximum (resolution of current regulation
too inaccurate). As the internal resistance cannot have a value of zero, the lower limit is defined to an achievable
minimum. This ensures that the electronic load, at very low input voltages, can consume a high input current from
the source, up to the maximum.
While the DC input is switched on and constant resistance mode is active, the condition “CR mode active” will
be shown on the graphics display by the abbreviation CR, as well it will be stored as internal status which can be
read via digital interface.
3.2.4 Power regulation / constant power / power limitation
Power regulation, also known as power limitation or constant power (CP), keeps
the DC input power of the device at the adjusted value, so that the current flowing
from the source, together with the input voltage, achieves the desired value. Power
limitation then limits the input current according to I
IN
= P
SET
/ U
IN
as long as the
power source is able to provide this power.
Power limitation operates according to the auto-range principle such that at lower
input voltages higher current can flow and vice versa, in order to maintain constant
power within the range P
N
(see diagram to the right).
While the DC input is switched on and constant power operation is active, the con-
dition “CP mode active” will be shown on the graphic display by the abbreviation
CP, as well it will be stored as internal status which can be read via digital interface.
Constant power operation impacts the internal set current value. This means that the maximum set current may
not be reachable if the set power value according to I = P / U sets a lower current. The user defined and displayed
set current value is always the upper limit only.
3.2.5 Dynamic characteristics and stability criteria
The electronic load is characterised by short rise and fall times of the current, which are achieved by a high band-
width of the internal regulation circuit.
In case of testing sources with own regulation circuits at the load, like for example power supplies, a regulation
instability may occur. This instability is caused if the complete system (feeding source and electronic load) has too
little phase and gain margin at certain frequencies. 180 ° phase shift at > 0dB amplification fulfils the condition for
an oscillation and results in instability. The same can occur when using sources without own regulation circuit (eg.
batteries), if the connection cables are highly inductive or inductive-capacitive.
The instability is not caused by a malfunction of the load, but by the behaviour of the complete system. An improve-
ment of the phase and gain margin can solve this. In practice, a capacity is directly connected to the DC input of
the load. The value to achieve the expected result is not defined and has to be found out. We recommend:
80 V models: 1000uF....4700uF
250 V models: 100uF...470uF
500 V models: 47uF...150uF
750 V models: 22uF...100uF
1500 V models: 4.7uF...22uF