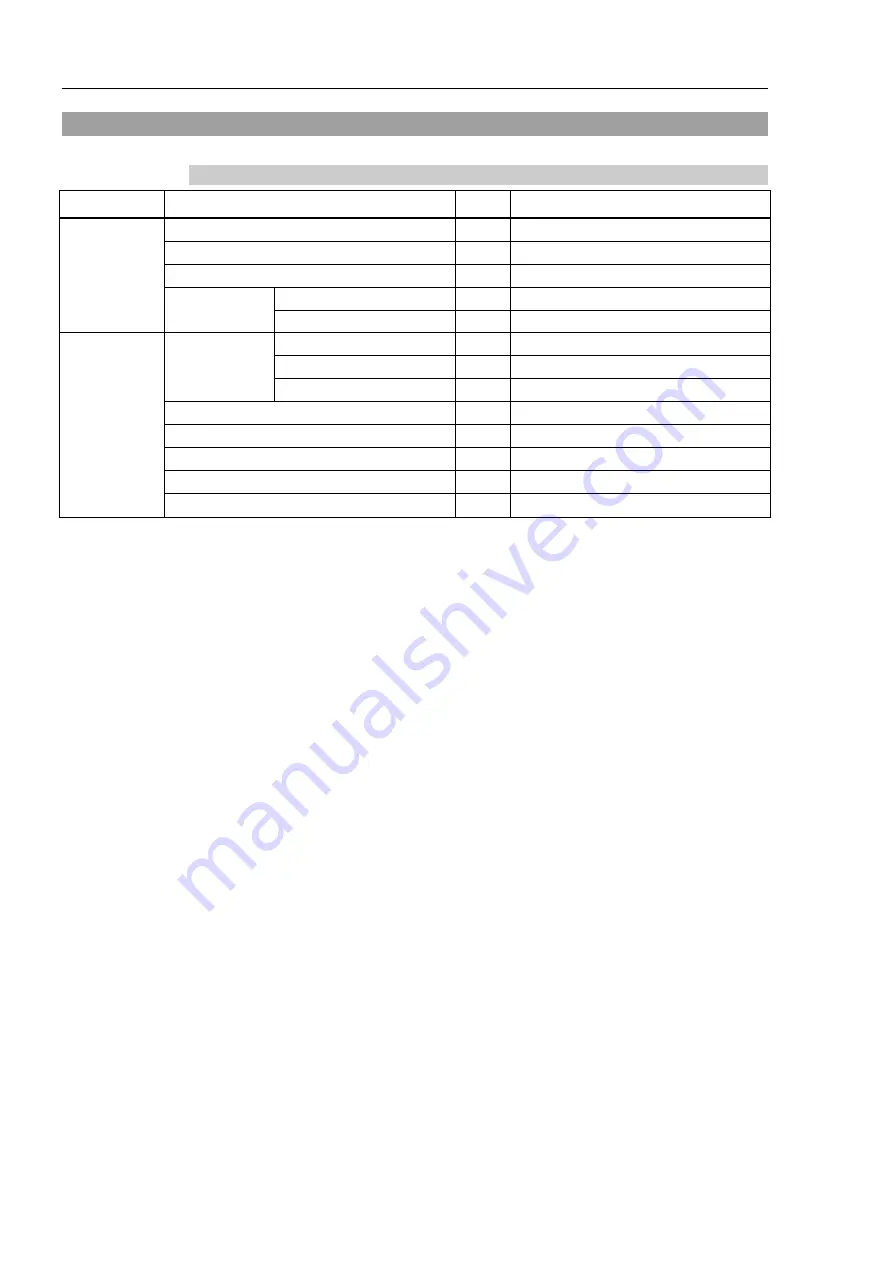
Maintenance 5. Joint #1
148
C12 Rev.3
5.1 M/C Cable Backward (Joint #1)
5.1.1 Joint #1 - Replacing the Motor (M/C Cable Backward)
Name
Qty.
Note
Maintenance
Parts
Motor unit (Joint #1)
1
2172922
Belt tensile jig*
1
1674582
J1 brake positioning jig*
1
1675081
Wire tie
AB100
-
1675753
AB350
-
1697428
Tools
Hexagonal
wrench
width across flats: 3 mm
1
For M4 hexagon socket head cap bolts
width across flats: 4 mm
1
For M5 hexagon socket head cap bolts
width across flats: 5 mm
1
For M6 hexagon socket head cap bolts
Cross-point screwdriver (#2)
1
For cross recessed head screws
Torque wrench
1
For tightening torque control
Nippers
1
For cutting the wire tie
Pliers
1
For tightening the wire tie
Belt tension meter
1
Refer: Unitta U-505
* The belt tensile jig and J1 brake positioning jig are assembly jigs. Use these jigs in relevant maintenance
steps.
The brake is mounted on each joint to prevent the arm from lowering due to its own weight while the Controller
power is OFF or the motor is OFF status. The brake does not work during replacement.
Be careful when performing maintenance work.
Summary of Contents for C12 Series
Page 1: ...Rev 3 EM204R4255F 6 Axis Robots C12 series MANIPULATOR MANUAL ...
Page 2: ...Manipulator manual C12 series Rev 3 ...
Page 8: ...vi C12 Rev 3 ...
Page 14: ...Table of Contents xii C12 Rev 3 ...
Page 16: ......
Page 30: ...Setup Operation 2 Specifications 16 C12 Rev 3 2 4 Outer Dimensions Unit mm ...
Page 84: ......
Page 155: ...Maintenance 4 Cable Unit C12 Rev 3 141 4 2 Connector Pin Assignment 4 2 1 Signal Cable ...
Page 156: ...Maintenance 4 Cable Unit 142 C12 Rev 3 ...
Page 157: ...Maintenance 4 Cable Unit C12 Rev 3 143 ...
Page 158: ...Maintenance 4 Cable Unit 144 C12 Rev 3 4 2 2 Power Cable ...