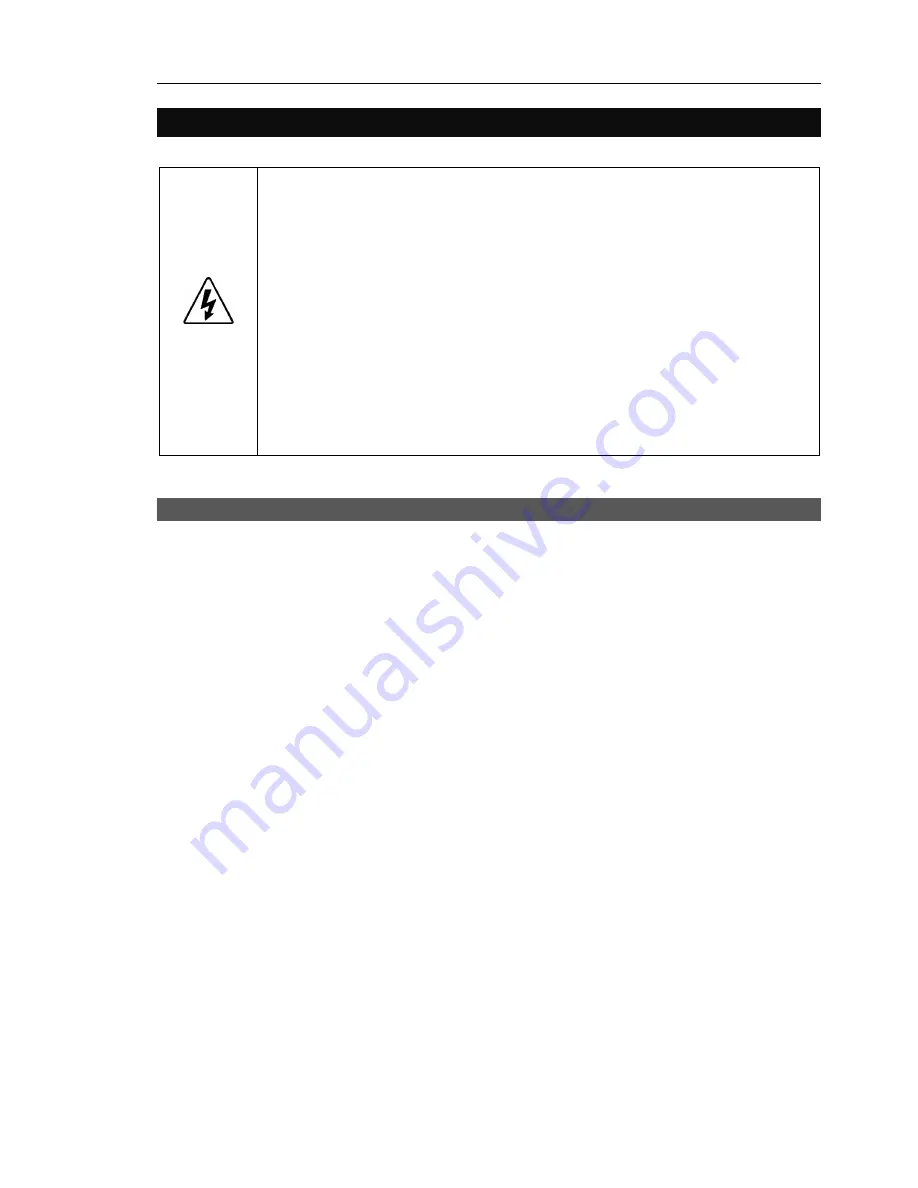
Maintenance 11. Replacing the Signal Relay Board
E2C Rev.6
177
11. Replacing the Signal Relay Board
■
Do not insert or pull out the motor connectors while the power to the robot system
is turned ON. Inserting or pulling out the motor connectors with the power ON is
extremely hazardous and may result in serious bodily injury as the Manipulator
may move abnormally, and also may result in electric shock and/or malfunction of
the robot system.
■
To shut off power to the robot system, pull out the power plug from the power
source. Be sure to connect the AC power cable to a power receptacle. DO
NOT connect it directly to a factory power source.
WARNING
■
Before performing any replacement procedure, turn OFF the controller and
related equipment, and then pull out the power plug from the power source.
Performing any replacement procedure with the power ON is extremely
hazardous and may result in electric shock and/or malfunction of the robot
system.
11.1 Before Replacing the Signal Relay Board
Before replacing the signal relay board, turn ON the Controller and keep it ON for 30 or
more minutes. Then, Turn OFF the Controller.
This preparation is necessary to charge the super-capacitor that keeps the position data.
The super-capacitor is mounted on each motor. The charged motors can keep the
position data for about 2 hours after the motors are disconnected from the lithium battery
on the signal relay board.
Since the power is supplied to each motor from the lithium battery on the signal relay
board via signal connector, the position data will exist even when the Controller is turned
OFF. When the signal connectors are disconnected, only the super-capacitors in the
motors will keep the position data.
When the data storage time of the super-capacitor is exceeded, the position data will be
lost, and the error* will occur when the Controller is turned ON.
* : In the case of SPEL CT, the “Error F-5016” occurs. In case of EPSON RC+, the error
message that Encoder alarm has occurred is displayed.
If the error occurs, perform the calibration of all joints and axes. For details on the
calibration method, refer to
Maintenance: 14. Calibration
.
Summary of Contents for E2C Series
Page 1: ...SCARA ROBOT E2C series MANIPULATOR MANUAL Rev 6 EM069R1409F ...
Page 2: ...MANIPULATOR MANUAL E2C series Rev 6 ...
Page 8: ...vi E2C Rev 6 ...
Page 14: ......
Page 82: ......
Page 92: ...Maintenance 2 General Maintenance 80 E2C Rev 6 ...
Page 118: ...Maintenance 4 Replacing the Cable Unit 106 E2C Rev 6 ...
Page 194: ...Maintenance 11 Replacing the Signal Relay Board 182 E2C Rev 6 ...