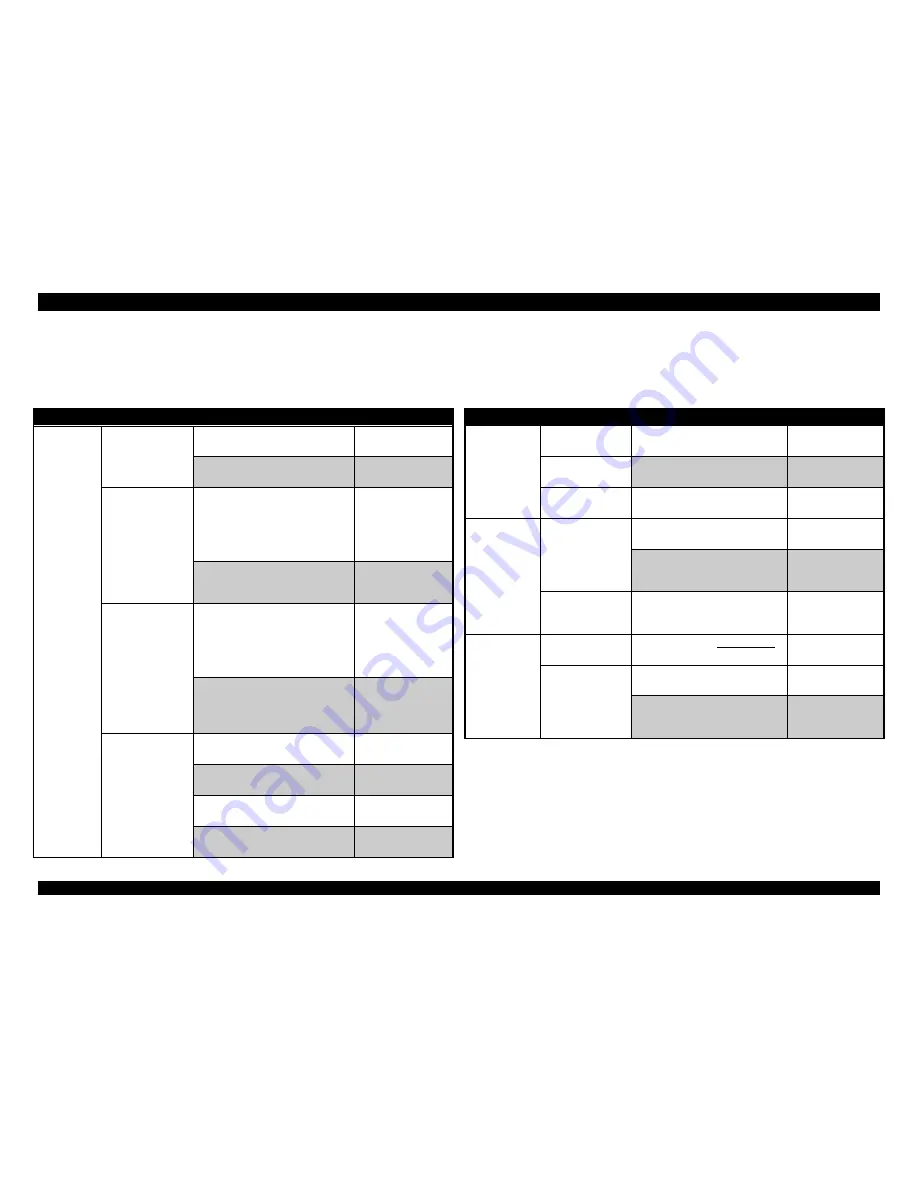
FX-2180 Service Manual
Disassembly and Assembly
Rev. A
4-2
4.1.3 Service Check After Repair
Before returning the printer after service, use the check list in the following
table, which provides a record to make servicing and shipping more efficient.
Table 4-3. Inspection Check List for the Repaired Printer (1)
Category
Components
Item
Check
Printer
unit
Printhead
Is any wire broken?
Checked
Not necessary
Is any wire worn out?
Checked
Not necessary
Carriage
mechanism
Dose the carriage move
smoothly?
Movement noisy
Mechanism dirty
Mechanism oily
Checked
Not necessary
Is the CR motor at the
correct temperature (not
overheating)?
Checked
Not necessary
Paper advance
mechanism
Is paper advancing
smoothly?
Movement noisy
Mechanism dirty
Mechanism oily
Checked
Not necessary
Is the paper feed motor
running at the correct
temperature (not
overheating)?
Checked
Not necessary
Paper Path
Is the type of paper in the
printer feeding smoothly?
Checked
Not necessary
Is the tractor feeding paper
correctly?
Checked
Not necessary
Is the paper path clear of
all obstructions?
Checked
Not necessary
Is the platen free of
damage?
Checked
Not necessary
Table 4-4. Inspection Check List for the Repaired Printer (2)
Category
Components
Item
Check
Printer unit
Ribbon mask
Is the ribbon mask free of
distortion?
Checked
Not necessary
Self-test
printing
Is the self-test printing
performed correctly?
Checked
Not necessary
On-line test
printing
Is the on-line printing
performed correctly?
Checked
Not necessary
Adjustment
Printhead
printing
Is the platen gap adjusted
correctly?
Checked
Not necessary
Is Bi-directional print
position adjusted
correctly?
Checked
Not necessary
Default
settings
Have user-changeable
settings been reset to the
default settings?
Checked
Not necessary
System
upgrade
ROM version
ROM version .
Checked
Not necessary
Shipment
Has the ribbon been
removed?
Checked
Not necessary
Have all relevant parts
been included in the
shipment?
Checked
Not necessary
Summary of Contents for FX-2180 - Impact Printer
Page 1: ...EPSON EPSON EPSON France S A SERVICE MANUAL FX 2180 PRODUIT ...
Page 2: ...6 59 0 18 3LQ PSDFW RW 3ULQWHU EPSON FX 2180 4009047 ...
Page 6: ...REVISION STATUS Rev Date Page s Contents A 1998 04 02 All First release ...
Page 11: ...PRODUCT DESCRIPTIONS 3 7 5 ...
Page 24: ...OPERATING PRINCIPLES 3 7 5 ...
Page 28: ...TROUBLESHOOTING 3 7 5 ...
Page 43: ...DISASSEMBLY AND ASSEMBLY 3 7 5 ...
Page 76: ...ADJUSTMENT 3 7 5 ...
Page 86: ...MAINTENANCE 3 7 5 ...
Page 89: ...APPENDIX 3 7 5 ...
Page 101: ......
Page 104: ......