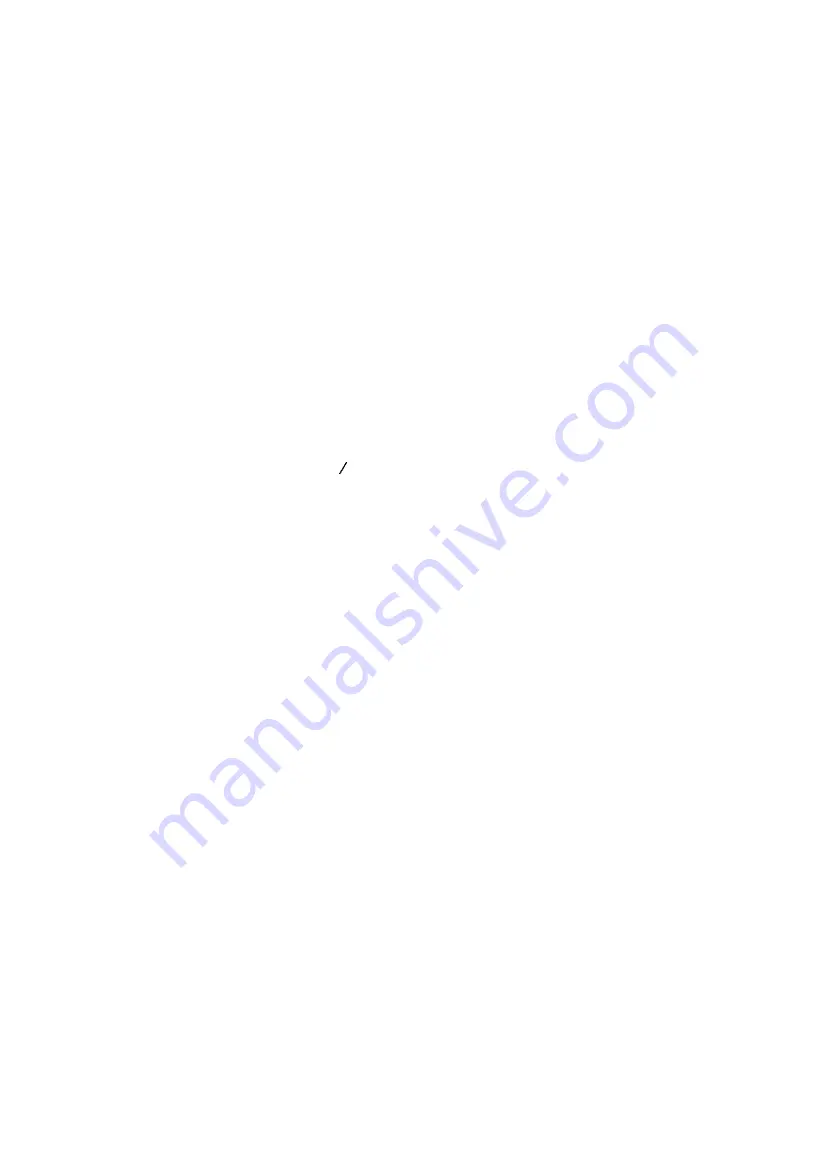
REV.-A
1.6.8 Paper Loading and Ejection
The release lever can disengage the pull tractor drive mechanism. This provides the printer with the
following paper handling features:
Automatic single-sheet loading without the cut-sheet feeder
Move the release lever to the friction feed position and place the sheet along the top or front paper
guide. A few seconds later, the printer automatically advances the sheet to the top-of-form position and
enters the RUNNING condition.
Automatic single-sheet loading and ejection with the cut-sheet feeder
Move the release lever to the friction feed position and load single-sheet paper into the hopper of the
cut-sheet feeder. Press the LOAD/EJECT button to load a sheet to the top-of-form position. If a paper
out is detected before printing starts, the printer automatically loads another sheet to the top-of-form
position.
Continuous paper loading and ejection (backout)
Move the release lever to the REAR PUSH FRONT PUSH position and load the paper onto the tractor
unit. Press the LOAD/EJECT button to load paper to the top-of-form position. If a paper out is detected
before printing starts, the printer automatically advances the paper to the top-of-form position.
If you press the LOAD/EJECT button after you load continuous paper, the printer moves the paper
backward to the push tractor. To back out several pages, press the LOAD/EJECT button several times.
Each time you press the LOAD/EJECT button, the printer reverse feeds one page.
When the paper is at the current setting for the top-of-form position, the top-of-form adjustment function
is valid for the setting a new top-of-form position. At this time, pressing the LOAD/EJECT button moves
the paper forward and pressing the LINE FEED/FORM FEED and ALT buttons at the same time moves
the paper backward. The adjusted top-of-form position for continuous paper is saved in EEPROM, but
the setting for single-sheet paper is not saved.
1.6.9 Tear-off Function
Auto tear off
You enable the auto tear-off function by setting a DIP switch. When this function is enabled and the
release lever is in the tractor position, the paper automatically advances to the tear-off position if the
input data buffer is empty and the printer is in the RUNNING condition. The TEAR OFF indicator light
comes on to indicate that you can use the LOAD/EJECT and LINE FEED/FORM FEED buttons with the
ALT button for backward and forward micro feed adjustment. Using micro feed, adjust the paper to
meet the tear-off edge. Once the tear-off position is set, this setting remains valid even after the printer
is turned off or initialized. If subsequent data is sent to the printer, the paper automatically returns to
the original position and printing starts. If you press the PAUSE button while the printer is advancing
the paper to the tear-off position, the paper returns to the original position and the printer enters the
PAUSE condition.
1-23
Summary of Contents for LQ-1170
Page 1: ...LQ 1170 24 PIN DOT MATRIX PRINTERS TM LQ8 1170 ...
Page 2: ...L Q 8 7 0 1 1 7 0 SERVICE MANUAL EPSON T Printed on recycled paper ...
Page 101: ...10 9 91 Yes NO Replace pluggable chips on main board 5 6 ...
Page 110: ...Table 5 4 Repair of the Power Supply Board Continued 5 15 ...
Page 118: ......
Page 121: ...REV A Figure 6 2 LQ 870 Lubrication Points 6 3 ...
Page 122: ...REV A Figure 6 3 LQ 1170 Lubrication Points 6 4 ...
Page 134: ...1 I II ...
Page 135: ...REV A Q m u D w IL 0 1 xl Figure A 3 CO60 DRV Board Circuit Diagram A 11 ...
Page 136: ...Figure A 4 CO60 PSB Board Circuit Diagram A 12 ...
Page 138: ...LO SLOE002 OWO9 1Nd 0 9 0 3 5 f l P I 11 I 01 I 6 I 8 1 L 9 I 9 I B I I2 I 2 I 1 ...
Page 142: ...REV A Fl 24ov T3 IsA I I II II AL I CU rl Figure A 10 C060 PSE Board Component Layout A 1 8 ...
Page 143: ...LMS d10 IP IMS dla ...
Page 144: ...REV A A 4 EXPLODED DIAGRAM Figure A l 2 1 Exploded Diagram for LQ 870 A 2 0 ...
Page 145: ......
Page 146: ...REV A Figure A 13 1 Exploded Diagram for Model 5DlO A 22 ...
Page 147: ... 5 2 5 610 c 3 5 9 0 El ...
Page 149: ...REV A A 5 CASE OUTLINE DRAWING Figure A l 4 1 Case Outline Drawing for LQ 870 A 25 ...
Page 151: ...lllllll IllI l l IIIIII II0 IIll III1 I I I C O 6 1 M A I N B o a r d A 3 7 ...
Page 152: ... U nRonenl2 i i C O 6 0 HAIN B t _1 m r OL J IIA IS I 19 CNI 36 I I8 I 23 IS ...
Page 153: ...a i iJ 0 E fig tfti I z ...