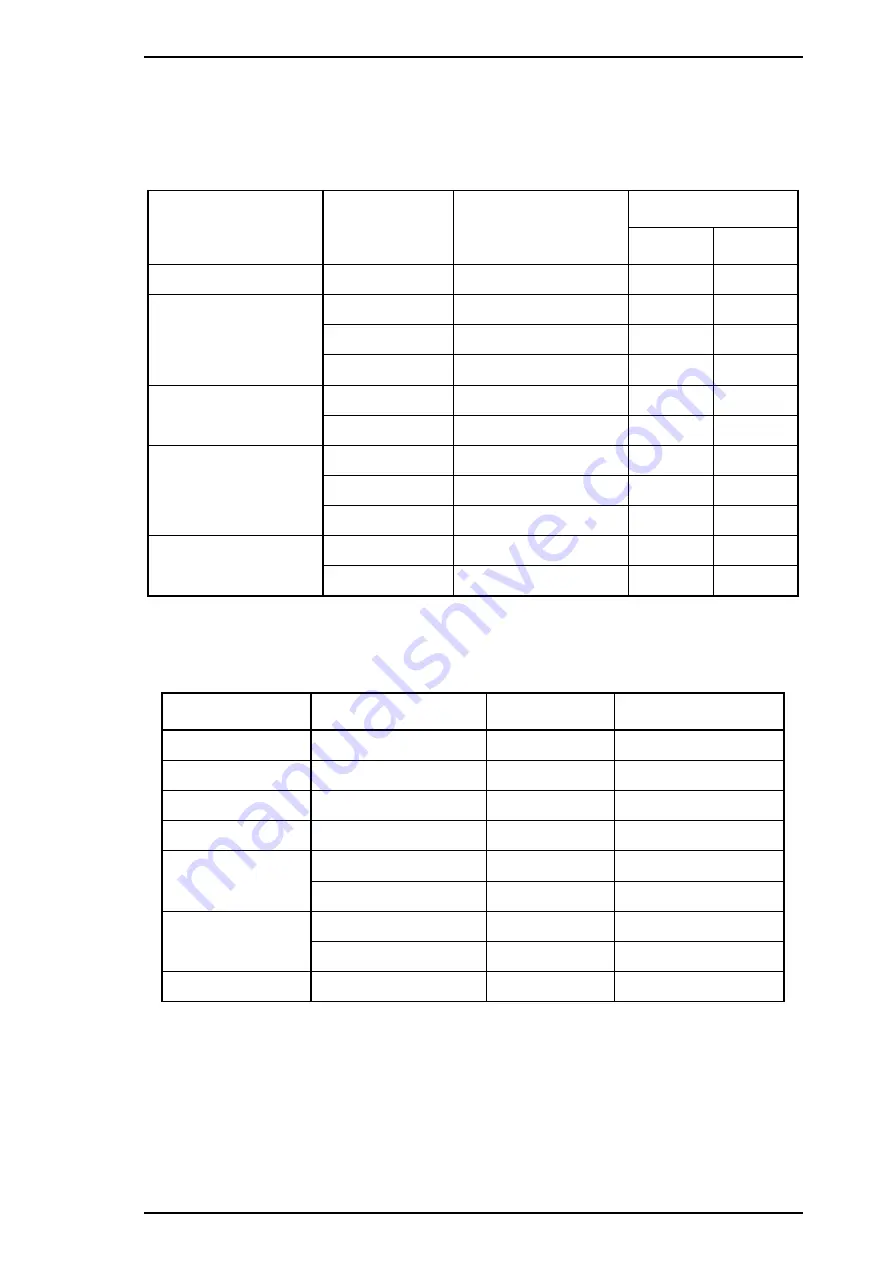
1.2.2 Printing Specifications
Copy capability
1 or 4 copies
Print speed and printable columns
Table 1-4 Print Speed and Printable Columns
Print Mode
Character Pitch
Printable Columns
Print Speed (cps)
Normal
Multipart
High-speed draft
10 cpi
136
440
293
Draft
10 cpi
136
330
220
12 cpi
163
396
264
15 cpi
204
495
330
Draft condensed
17 cpi
233
283
189
20 cpi
272
330
220
NLQ
10 cpi
136
110
73
12 cpi
163
132
88
15 cpi
204
165
110
LQ Condensed
17 cpi
233
189
126
20 cpi
272
220
147
Resolution
Table 1-5 Print Resolution
Print Mode
Horizontal Density
Vertical Density
Adjacent Dot Printed?
High-speed draft
90 dpi
180 dpi
No
Draft
120 dpi
180 dpi
No
Draft condensed
240 dpi
180 dpi
No
NLQ
360 dpi
180 dpi
No
8 pin bit image
60, 80, 90, or 120 dpi
60 dpi
Yes
120 or 240 dpi
60 dpi
No
24 pin bit image
60, 90, 120, or 180 dpi
180 dpi
Yes
360 dpi
180 dpi
No
Raster graphics
180 or 360 dpi
180 or 360 dpi
Yes
Acoustic noise
53 dB (A), ISO 7779 pattern
LQ-2170 Service Manual
Product Description
Rev.A
1-5
Summary of Contents for LQ-2170
Page 1: ...EPSON TERMINAL PRINTER LQ 2170 SERVICE MANUAL EPSON 4005735 ...
Page 5: ...REVISION SHEET Revision Issued Date Revision Page Rev A December 5 1995 1st issued ...
Page 11: ...Figure 1 1 Exterior View of the LQ 2170 Product Description LQ 2170 Service Manual 1 2 Rev A ...
Page 80: ......
Page 127: ...1 Abnormal CR Operation LQ 2170 Service Manual Troubleshooting Rev A 5 5 ...
Page 141: ...LQ 2170 Service Manual Troubleshooting Rev A 5 19 ...
Page 156: ...Appendix LQ 2170 Service Manual A 10 Rev A ...
Page 158: ...Appendix LQ 2170 Service Manual A 12 Rev A ...
Page 159: ...Figure A 3 C165 PSB Board Assembly Circuit Diagram LQ 2170 Service Manual Appendix Rev A A 13 ...
Page 160: ...Appendix LQ 2170 Service Manual A 14 Rev A ...
Page 161: ...Figure A 4 C165 PSE Board Assembly Circuit Diagram LQ 2170 Service Manual Appendix Rev A A 15 ...
Page 162: ...Appendix LQ 2170 Service Manual A 16 Rev A ...
Page 167: ...Figure A 9 LQ 2170 Exploded Diagrams 2 LQ 2170 Service Manual Appendix Rev A A 21 ...
Page 168: ...Figure A 10 LQ 2170 Exploded Diagrams 3 Appendix LQ 2170 Service Manual A 22 Rev A ...
Page 169: ...Figure A 11 C S F Bin1 Exploded Diagrams 1 LQ 2170 Service Manual Appendix Rev A A 23 ...
Page 170: ...Figure A 12 C S F Bin1 Exploded Diagrams 2 Appendix LQ 2170 Service Manual A 24 Rev A ...
Page 171: ...Figure A 13 C S F Bin2 Exploded Diagrams LQ 2170 Service Manual Appendix Rev A A 25 ...
Page 172: ...Table A 15 Part No Reference Table Appendix LQ 2170 Service Manual A 26 Rev A ...
Page 173: ...Table A 15 Part No Reerence Table Continue LQ 2170 Service Manual Appendix Rev A A 27 ...
Page 174: ...Appendix LQ 2170 Service Manual A 28 Rev A ...
Page 175: ...EPSON Printed in Japan 95 12 05 S ...