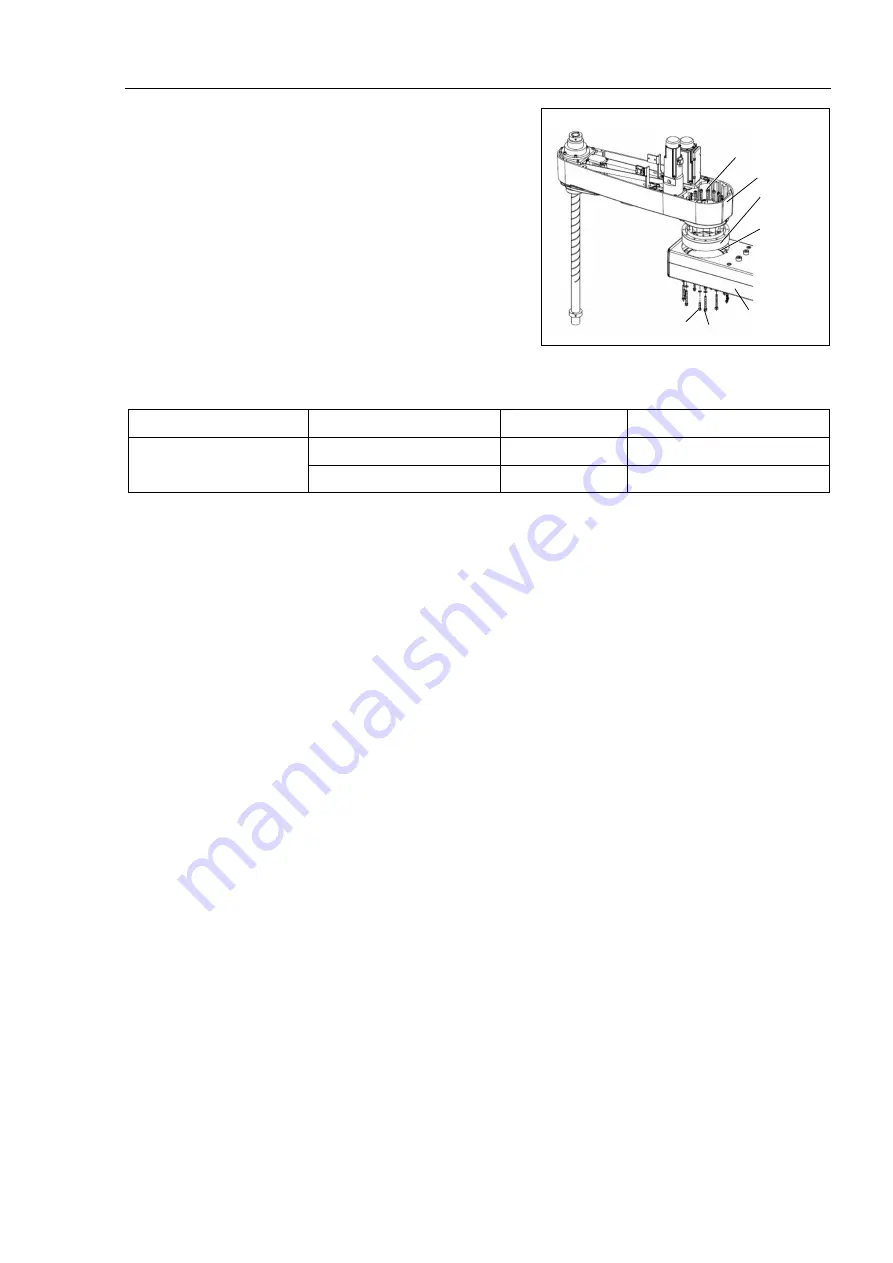
Maintenance 6. Arm #2
LS20 Rev.4
101
(5) Set the O-ring removed in the removal
step (6) into the O-ring groove of the
Arm #1 and install the flexspline on
the Arm #1.
A: 16-M5
×
30
B: 8-M5
×
45+8-M5 plain washer
C: 4-M4
×
20+4-M4 plain washer
Loosely secure all bolts in a crisscross
pattern so that the bolts will be
secured evenly. Then, using a torque
wrench, tighten each bolt securely in a
crisscross pattern at the torque
specified in the table below.
A
Arm #2
Reduction
Gear Unit
Arm #1
B
C
O-ring
Item
Bolt type
Qty.
Tightening torque
Joint #2
reduction gear unit
M4
4
5.5 N
⋅
m (56.1 kgf
⋅
cm)
M5
8
10.0 N
⋅
m (102 kgf
⋅
cm)
Be careful not to apply too much force since it may damage the parts
(6) Apply grease between the motor flange and waveform generator and next inside the
flexspline.
Between the motor flange and waveform generator
Grease volume: 38 g (SK-1A)
Inside the flexspline
Grease volume: 90 g (SK-1A)
(7) Set the attached O-ring into the O-ring groove of the circular spline.
Secure the Arm #2 on the circular spline.
Hexagon socket head cap bolts: 16-M5×30
Tightening torque
: 10.0 N
⋅
m (102 kgf
⋅
cm)
(8) Mount and Joint #2 motor.
Follow the installation steps in
Maintenance: 6.1 Replacing Joint #2 Motor
.
NOTE
Summary of Contents for LS20
Page 1: ...Rev 4 EM179R3533F SCARA ROBOT LS20 series MANIPULATOR MANUAL ...
Page 2: ...MANIPULATOR MANUAL LS20 series Rev 4 ...
Page 8: ...vi LS20 Rev 4 ...
Page 12: ...TABLE OF CONTENTS x LS20 Rev 4 ...
Page 14: ......
Page 29: ...Setup Operation 2 Specifications LS20 Rev 4 17 LS20 804S Standard Model ...
Page 31: ...Setup Operation 2 Specifications LS20 Rev 4 19 LS20 804C Cleanroom Model ...
Page 33: ...Setup Operation 2 Specifications LS20 Rev 4 21 LS20 A04S Standard Model ...
Page 35: ...Setup Operation 2 Specifications LS20 Rev 4 23 LS20 A04C Cleanroom Model ...
Page 72: ......
Page 92: ...Maintenance 4 Cable 80 LS20 Rev 4 4 2 Wiring Diagrams 4 2 1 Signal Cable ...
Page 176: ...Maintenance 14 Maintenance Parts List 164 LS20 Rev 4 ...