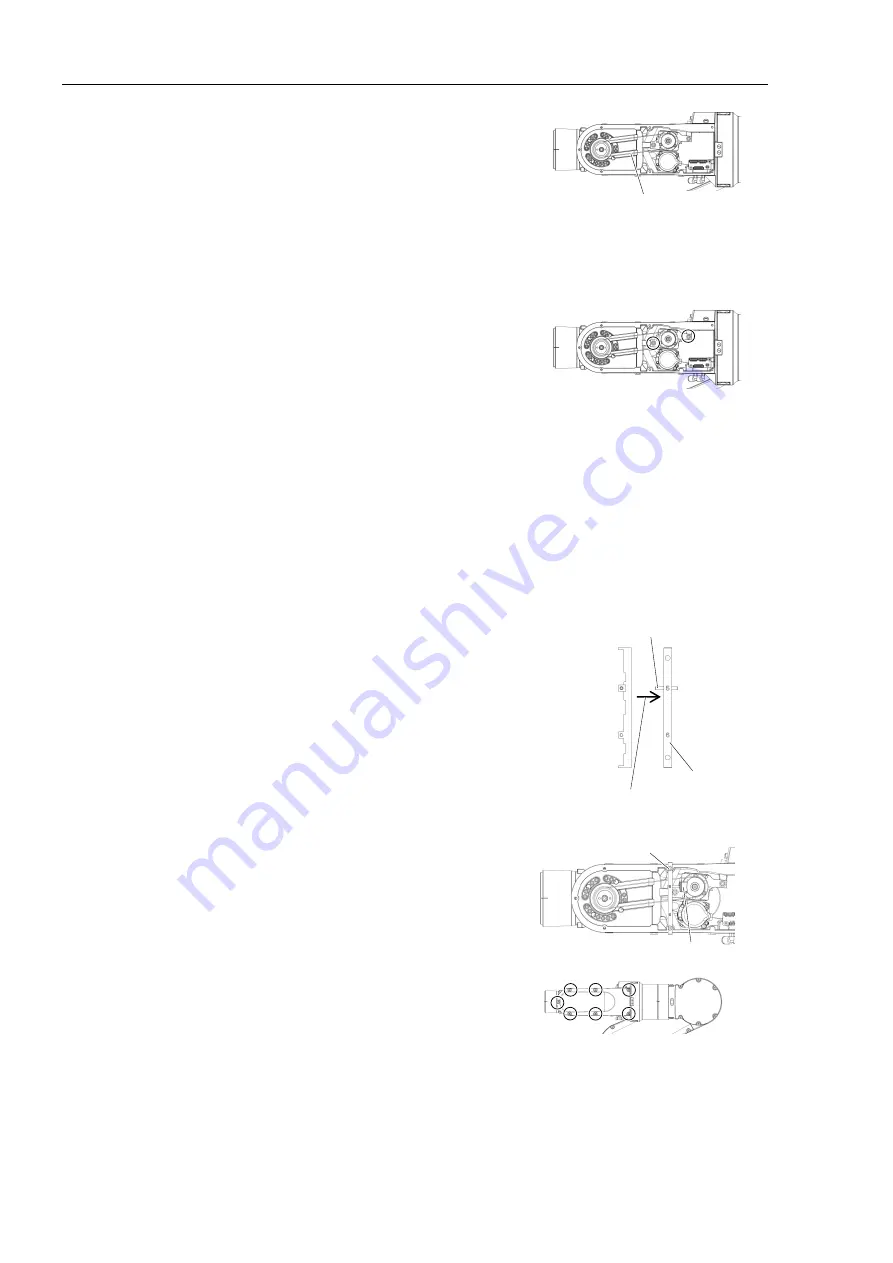
Maintenance 5. Actuator Units
306
N6 Rev.2
Installation
Joint #5
timing belt:
(1) Install the timing belt and temporarily fix the
Joint #5 motor unit.
Hexagon socket head cap bolts: 2-M4
×
15
(with plain washer for slotted hole thickness:
1.5mm)
Timing belt
When temporary fixing the Joint #5 motor unit, make sure that the motor unit can be
moved by hand and does not tilt when being pulled. If the unit is fixed too loose or
too tight, the belt will not have proper tension.
(2) Apply the proper tension to the Joint #5 timing
belt and fix the Joint #5 motor unit.
Tension of Joint #5 timing belt: 23
±
5 N
Belt tension meter setting value
Weight: 2.5g/mm Width×m Span, Width:6 mm, Span:142 mm
Hexagon socket head cap bolts:
2-M4
×
15 (with plain washer for slotted hole thickness: 1.5mm)
Tightening torque: 4.0
±
0.2 N·m
Regarding belt tension:
-
Jumping (position gap) may occur if the value is below the lower limit.
-
Vibration (abnormal noise) or reduction of life of the parts may occur if the
value exceeds the upper limit.
When using belt tensile jig (maintenance part):
1.
Install the hexagon socket set screws (M3×20) to
the holes on inscribed side of “5” on the belt
tensile jig.
2.
Fix the belt tensile jig on the Arm #4 with the
hexagon socket head cap bolts (2-M4×15).
3.
Push the rubber to the pulley. Push the rubber
with the hexagon socket set screws (M3×20) to
apply tension.
Be careful not to push the set screws forcibly.
Belt tensile jig
Hexagon socket set
screws: M3
×
20
Direction of set screws
2-M4
×
15
Rubber
(3) Install the Arm #4 side cover.
Cross recessed binding head machine screw:
7-M4×8
Tightening torque: 0.45
±
0.05 N·m
Be careful not to catch the cables. The cables will be disconnected.
(4) Perform calibration for the Joint #5.
For details, refer to
Maintenance 8. Calibration.
NOTE
NOTE
NOTE
NOTE
Summary of Contents for N6 Series
Page 1: ...Rev 2 EM187R3735F 6 Axis Robots N6 series MANIPULATOR MANUAL ...
Page 2: ...Manipulator manual N6 series Rev 2 ...
Page 8: ...vi N6 Rev 2 ...
Page 14: ......
Page 27: ...Setup Operation 1 Safety N6 Rev 2 15 N6 A850 R C A D F G F E H G F B G F G F F F N6 A850 BR F ...
Page 34: ...Setup Operation 2 Specifications 22 N6 Rev 2 N6 A850 BR Cable direction Upward ...
Page 52: ...Setup Operation 3 Environment and Installation 40 N6 Rev 2 N6 A850 R Maximum motion range 802 ...
Page 66: ...Setup Operation 4 End Effectors 54 N6 Rev 2 N6 A850 R Unit mm ...
Page 104: ......
Page 274: ...Maintenance 4 Cable 262 N6 Rev 2 4 7 1 Signal Power cable ...
Page 275: ...Maintenance 4 Cable N6 Rev 2 263 ...
Page 276: ...Maintenance 4 Cable 264 N6 Rev 2 4 7 2 User Cable ...