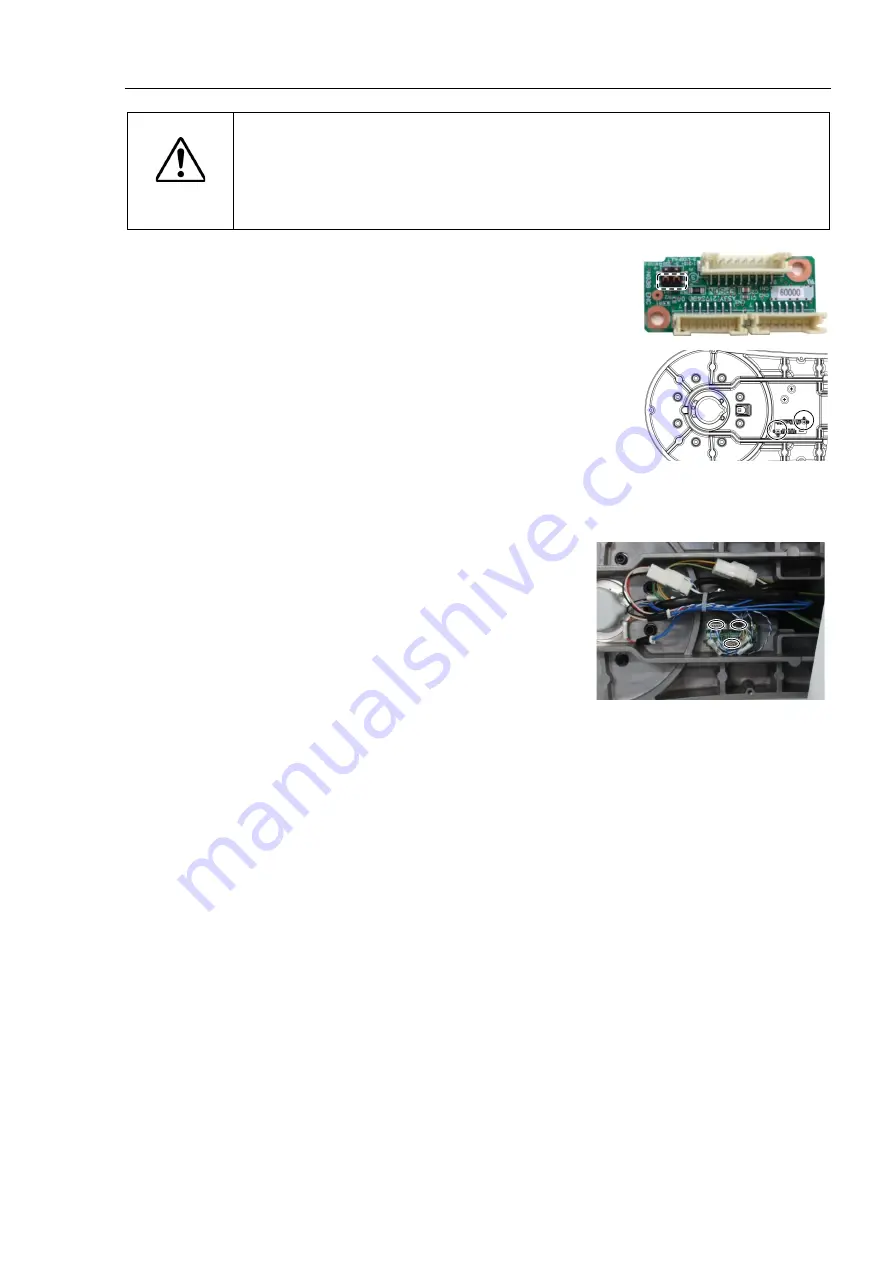
Maintenance 7. Boards
N6 Rev.2
341
CAUTION
■
Improper jumper pin settings may result in occurrence of the errors such as below.
Example:
5042: Position error overflow in high power state.
Check the power cable connection, the robot, the driver and the motor.
When replacing the boards, be careful not to configure them incorrectly.
Installation
Encoder Board 2
(1) Change the position of the jumper pin on the encoder
board 2 to “1-2 short”.
(2) Install the encoder board 2 to the Arm #2.
Cross recessed binding head machine screws:
2-M3×6
Tightening torque: 0.45
±
0.05 N·m
Be careful not to drop the screws inside the Manipulator while removing them.
Make sure to install as the same direction as the figure.
(3) Connect the connectors to the encoder board 2.
Connectors: EB02_CN1
EB0x_CN2 (Joint #2 side)
EB0x_CN2 (Joint #3 side)
Be careful that the jumper pins on the board do not come off.
(4) Install the Arm #2 cover (Arm #1 side).
For details, refer to
Maintenance 3. Covers
.
(5) Turn ON the controller.
(6) Calibrate the Joints #2 and #3.
For details, refer to
Maintenance 8. Calibration
.
NOTE
NOTE
NOTE
Summary of Contents for N6 Series
Page 1: ...Rev 2 EM187R3735F 6 Axis Robots N6 series MANIPULATOR MANUAL ...
Page 2: ...Manipulator manual N6 series Rev 2 ...
Page 8: ...vi N6 Rev 2 ...
Page 14: ......
Page 27: ...Setup Operation 1 Safety N6 Rev 2 15 N6 A850 R C A D F G F E H G F B G F G F F F N6 A850 BR F ...
Page 34: ...Setup Operation 2 Specifications 22 N6 Rev 2 N6 A850 BR Cable direction Upward ...
Page 52: ...Setup Operation 3 Environment and Installation 40 N6 Rev 2 N6 A850 R Maximum motion range 802 ...
Page 66: ...Setup Operation 4 End Effectors 54 N6 Rev 2 N6 A850 R Unit mm ...
Page 104: ......
Page 274: ...Maintenance 4 Cable 262 N6 Rev 2 4 7 1 Signal Power cable ...
Page 275: ...Maintenance 4 Cable N6 Rev 2 263 ...
Page 276: ...Maintenance 4 Cable 264 N6 Rev 2 4 7 2 User Cable ...