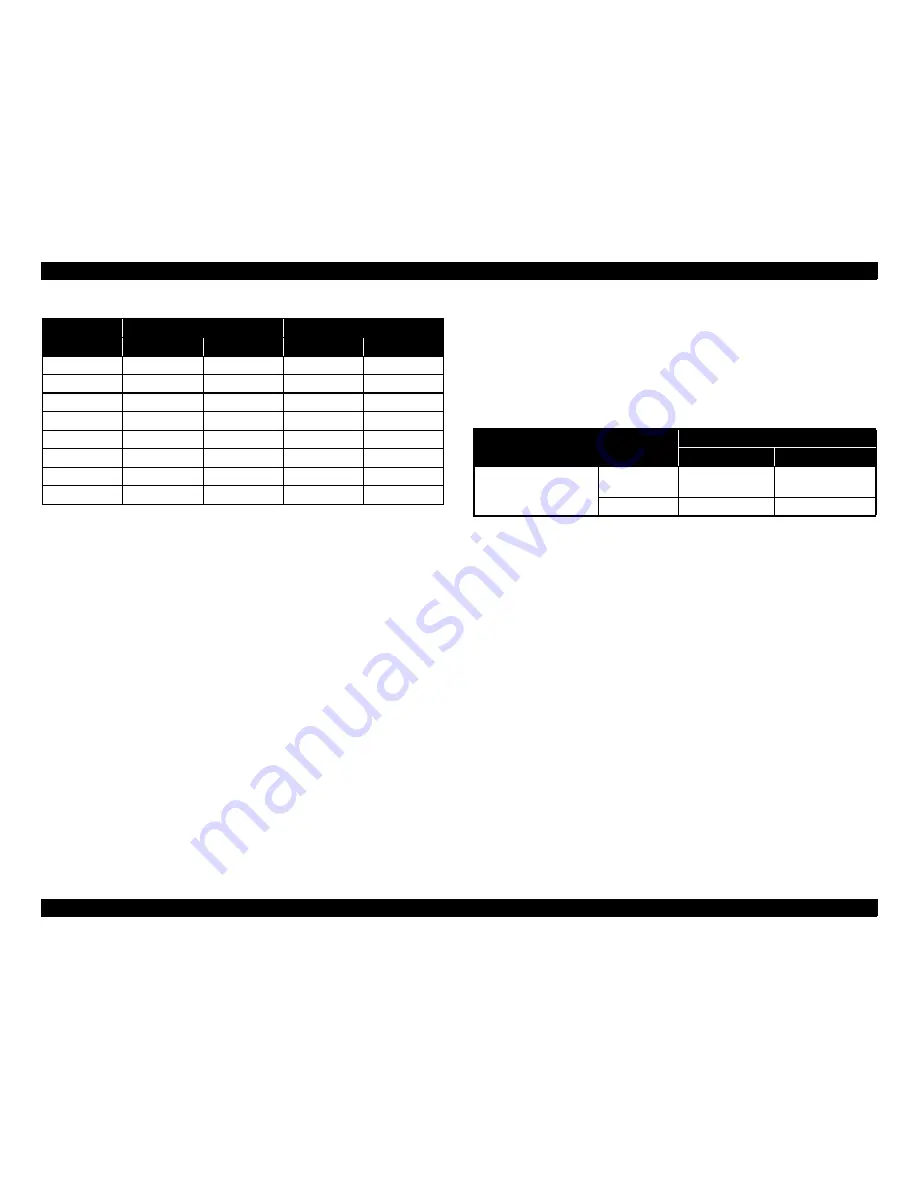
Stylus Photo R1900/R2880/R2000
Revision E
Stylus Photo R2000
Features
176
Confidential
Table 8-5. Communication Speed for 802.11n
*
1
*
2
MCS : Modulation and Coding Scheme GI : Guard Interval
Note *1:
After the decimal point is displayed by the 0.5Mbps.Number in parentheses is
defined value of 802.11n standard.
*2:
For regulation of Radio Law, if Bandwidth is fixed to 20MHz by exporting area,
maximum of Communication Speed is restricted to upper limit of 20MHz.
Switching Wired/Wireless LAN
This printer can be connect to the network via either Wired LAN or Wireless LAN
connection only.
Enabling/disabling the Wireless LAN can be made from the Control Panel. When the
Wireless LAN is enabled, it gets priority over the Wired Lan regardless of whether the
LAN Cable is connected. The default Wireless LAN setting is “Disabled”.
Note * : No service via network is available without connecting the LAN Cable (because
network communication is not established.) except printing a status sheet or the like.
MCS Index
Bandwidth = 20MHz
Bandwidth= 40MHz
GI = 800ns
GI = 400ns
GI = 800ns
GI = 400ns
0
6.5
7 (7.2)
13.5
15
1
13
14 (14.4)
27
30
2
19.5
21.5 (21.7)
40.5
45
3
26
28.5 (28.9)
54
60
4
39
43 (43.3)
81
90
5
52
57.5 (57.8)
108
120
6
58.5
65
121.5
135
7
65
72 (72.2)
135
150
Table 8-6. Wireless LAN Setting from the Control Panel
Setting from Control Panel
LAN Cable Connection State
Connected
Disconnected
Wireless LAN
Disabled
(Default)
Wired LAN
---*
Enabled
Wireless LAN
Wireless LAN
Summary of Contents for R1900 - Stylus Photo Color Inkjet Printer
Page 1: ...EPSONStylusPhotoR1900 R2880 R2000 Color Inkjet Printer SEIJ07010 SERVICE MANUAL Confidential ...
Page 9: ...Confidential C H A P T E R 1 PRODUCTDESCRIPTION ...
Page 28: ...Confidential C H A P T E R 2 OPERATINGPRINCIPLES ...
Page 33: ...Confidential C H A P T E R 3 TROUBLESHOOTING ...
Page 69: ...Confidential C H A P T E R 4 DISASSEMBLYANDASSEMBLY ...
Page 137: ...Confidential C H A P T E R 5 ADJUSTMENT ...
Page 161: ...Confidential C H A P T E R 6 MAINTENANCE ...
Page 170: ...Confidential C H A P T E R 7 APPENDIX ...
Page 172: ...Confidential C H A P T E R 8 STYLUSPHOTOR2000 ...