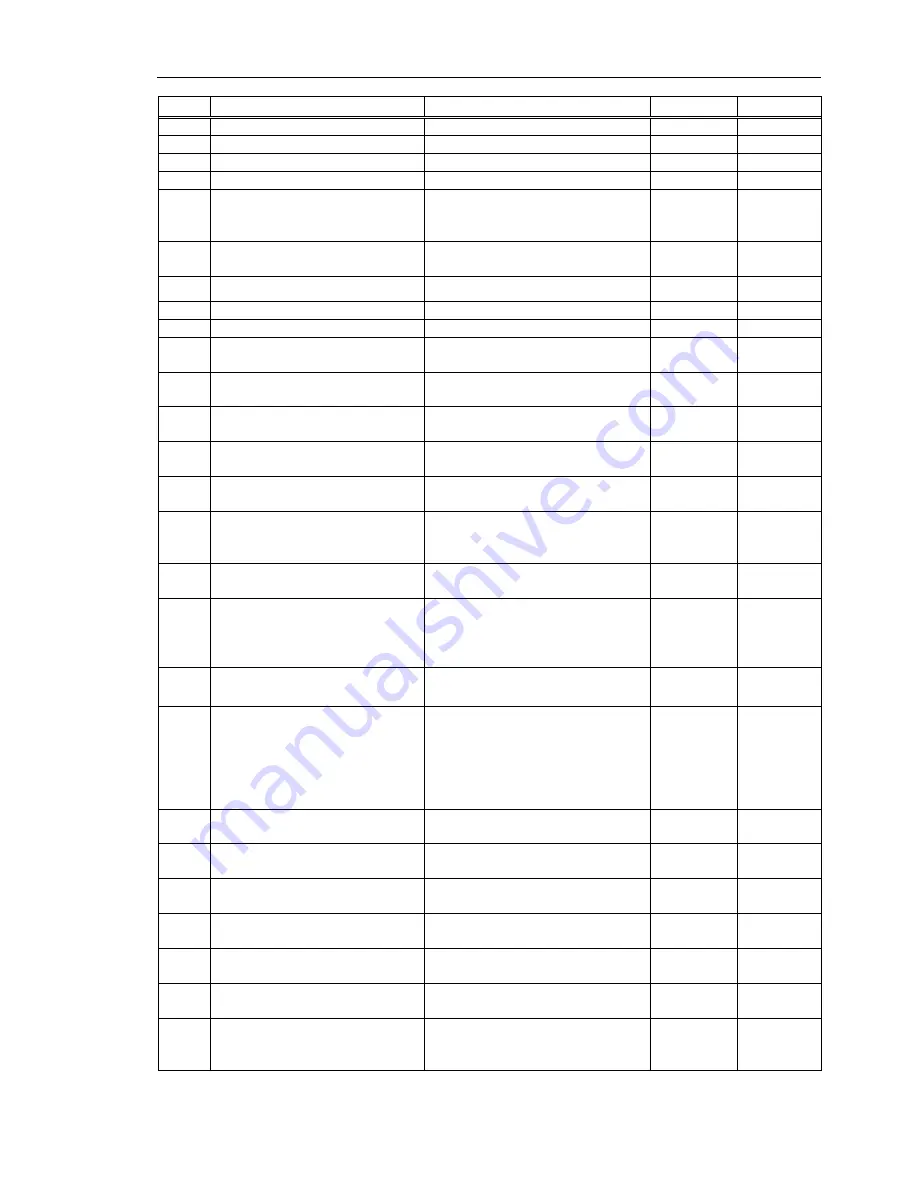
Maintenance 9. Troubleshooting
RC90 (EPSON RC+ 7.0) Rev.8
121
No.
Message
Remedy
Note 1
Note 2
1103
File is not found.
Check whether the file exists.
1104
Project file was not found.
Rebuild the project.
1105
Object file was not found.
Rebuild the project.
1106
Point files were not found.
Rebuild the project.
1107
The program is using a feature that is
not supported by the current controller
firmware version.
Check the compiler version in the
EPSON RC+
7.0-[Project]-[Properties]-[Compiler].
1108
One or more source files are updated.
Please build the project.
Rebuild the project.
1109
Not enough storage capacity.
Increase free space of the USB memory.
1110
File is not found.
-
1111
Conveyor file was not found.
-
1120
File failure.
Setting file is corrupt.
Restore the controller configuration.
1121
File failure.
Project file is corrupt.
Rebuild the project.
1122
File failure.
Point file is corrupt.
Rebuild the project.
1123
File failure.
I/O label file is corrupt.
Rebuild the project.
1124
File failure.
User error file is corrupt.
Rebuild the project.
1126
File failure.
Software option information is
corrupt.
1.
Reboot the controller.
2.
Reinstall the firmware.
3.
Reconfigure the option.
1127
File failure.
Vision file is corrupt.
Rebuild the project.
1128
File failure.
Backup information file is corrupt.
The specified backup information cannot
be restored.
Acquire the backup information again,
and then restore the file.
1130
Error message failure.
No item is found in the error history.
No error history exists.
Reboot the controller.
1131
Cannot access the USB memory.
Insert the USB memory properly. When
this error still occurs after the USB
memory is inserted properly, the
memory may be unrecognizable to
controller. Insert another memory to
check the operation.
1132
File failure.
Failed to copy the file.
-
1133
File failure.
Failed to delete the file.
-
1134
File failure.
GUI Builder file is corrupt.
Rebuild the project.
1140
File failure.
Failed to open the object file.
Rebuild the project.
1141
File failure.
Failed to open the project file.
Rebuild the project.
1142
File failure.
Failed to read the project file.
Rebuild the project.
1143
File failure.
Failed to open the condition save file.
1.
Retry using the same USB memory.
2.
Retry using another USB memory.
3.
Retry after rebooting the controller.
Summary of Contents for RC90
Page 1: ...Rev 8 EM158C3031F ROBOT CONTROLLER RC90 EPSON RC 7 0 ...
Page 2: ...ii ROBOT CONTROLLER RC90 EPSON RC 7 0 Rev 8 ...
Page 10: ...viii RC90 EPSON RC 7 0 Rev 8 ...
Page 17: ...Safety This section contains information for safety of the Robot System ...
Page 18: ......
Page 24: ......
Page 28: ...Setup Operation 1 Specifications 12 RC90 EPSON RC 7 0 Rev 8 1 3 Outer Dimensions Unit mm ...
Page 95: ...Maintenance This section contains maintenance procedures for the Robot Controller ...
Page 96: ......